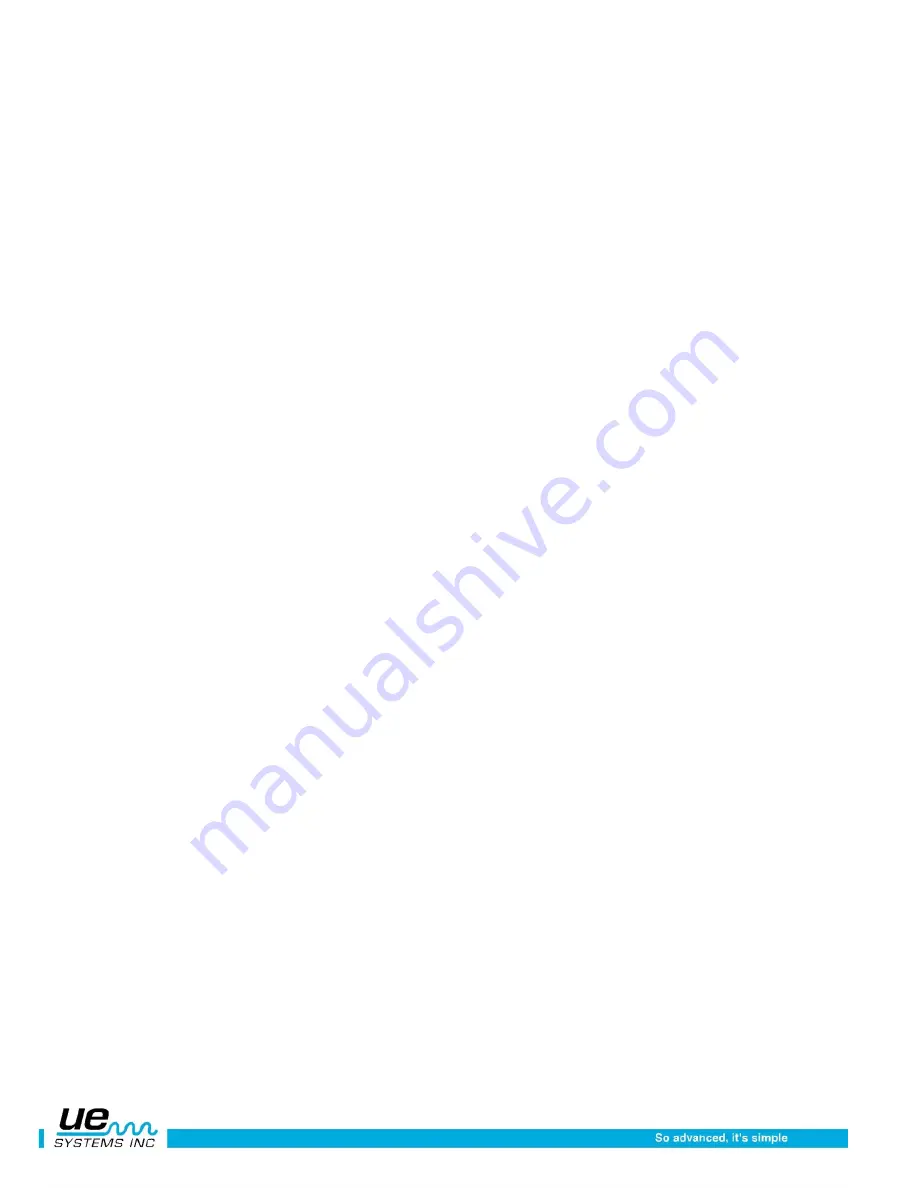
Version 1
20
It is important to consider two elements of potential failure. One is lack of lubrication while the other is over
lubrication.
Normal bearing loads causes an elastic deformation of the elements in the contact area which give a
smooth elliptical stress distribution. But bearing surfaces are not perfectly smooth. For this reason, the
actual stress distribution in the contact area will be affected by a random surface roughness. In the
presence of a lubricant film on a bearing surface, there is a dampening effect on the stress distribution
and the acoustic energy produced will be low. Should lubrication be reduced to a point where the stress
distribution is no longer present, the normal rough spots will make contact with the race surfaces and
increase the acoustic energy. These normal
microscopic disuniformities will begin to produce wear and
the possibilities of small fissures may develop which contributes to the "Pre-Failure" condition. Therefore,
aside from normal wear, the fatigue or service life of a bearing is strongly influenced by the relative film
thickness provided by an appropriate lubricant.
Lack of Lubrication
To avoid lack of lubrication, note the following:
1. As the lubricant film reduces, the sound level will increase. A rise of about 8 dB over baseline
accompanied by a uniform rushing sound will indicate lack of lubrication.
2. When lubricating, add just enough to return the reading to base line.
3. Use caution. Some lubricants will need time to run to uniformly cover the bearing surfaces. Lubricate
a little at a time. DO NOT OVER-LUBRICATE
Over-Lubrication
One of the most common causes of bearing failure is over-lubrication. The excess stress of lubricant
often breaks bearing seals or causes a build-up of heat which can create stress and deformity.
To avoid over-lubrication:
1. Don't lubricate if the base line reading and base line sound quality is maintained.
2. When lubricating, use just enough lubricant to bring the ultrasonic reading to baseline.
3. As mentioned in 3 above, use caution. Some lubricants will need time to uniformly cover the
bearing surfaces.
SLOW SPEED BEARINGS
Monitoring slow speed bearings is possible with the Ultraprobe 2000. Due to the sensitivity range, it is
quite possible to listen to the acoustic quality of bearings. In extremely slow bearings (less than 25 RPM),
it is often necessary to disregard
the meter and listen to the sound of the bearing. In these extreme
situations, the bearings are usually large (1"-2" and up) and greased with high viscosity lubricant. Most
often no sound will be heard as the grease will absorb most of the acoustic energy. If a sound is heard,
usually a crackling sound, there is some indication of deformity occurring.
On most other slow speed bearings, it is possible to set a bas
e line and monitor as described. It is suggested
that the Attenuator Transfer Curve method be used since the sensitivity will usually have to be higher than normal.
FFT INTERFACE
The Ultraprobe may be interfaced with FFT's via the UE-MP-BNC-2 Miniphone to BNC connector or the UE DC2 FFT
Adapter. The Miniphone plug is inserted into the headphone jack of the Ultraprobe and the BNC connector is attached
to the analog-in connector of the FFT. Using the heterodyned - converted low frequency signal, the FFT will be able to
receive the ultrasonic information detected from the Ultraprobe. In
this instance it can be used to monitor and trend
low speed bearings. It can also extend the use of the FFT to record all types of mechanical information such as
leaking valves, cavitation, gear wear, etc.