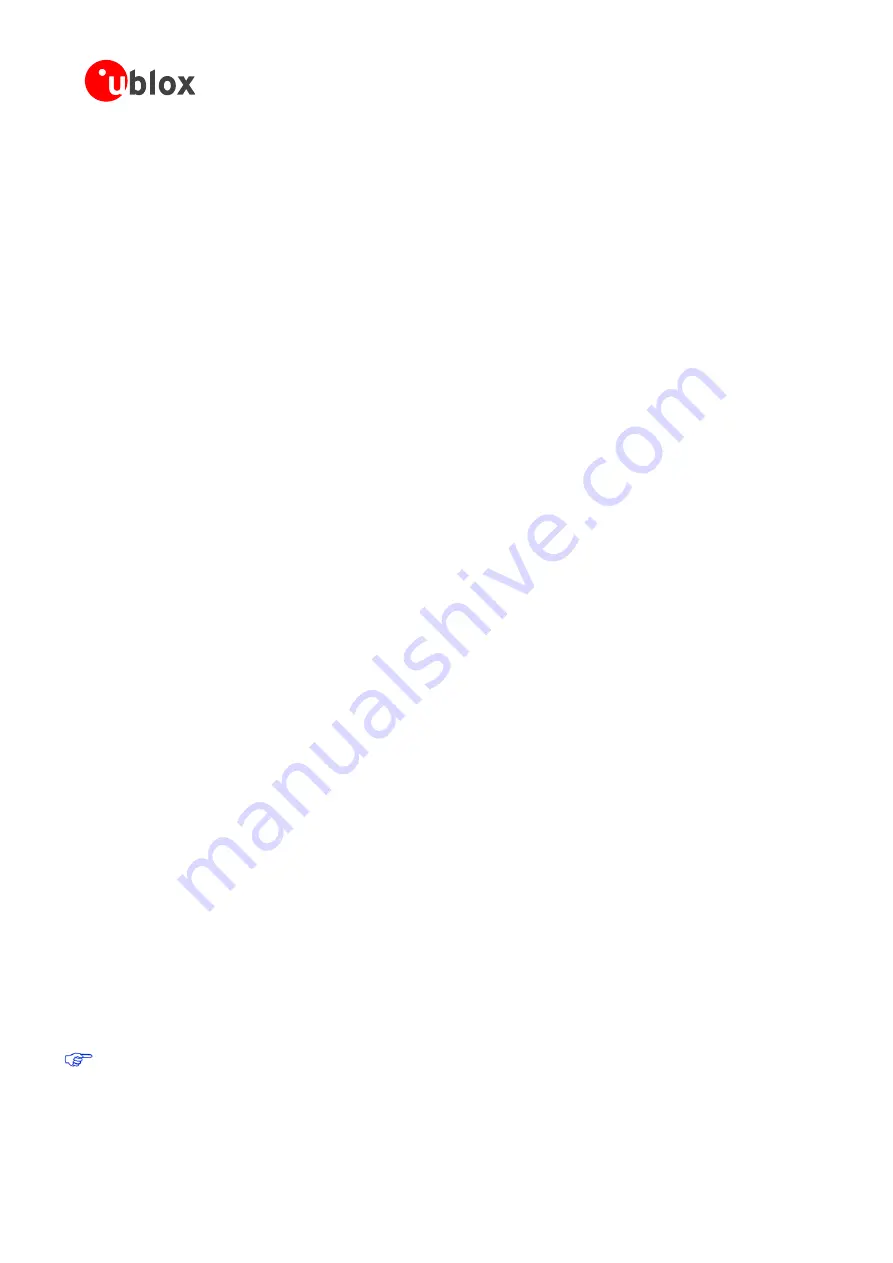
SARA-G3 and SARA-U2 series - System Integration Manual
UBX-13000995 - R26
Design-in
Page 105 of 217
2.2.1.5
Guidelines for VCC supply circuit design using a primary (disposable) battery
The characteristics of a primary (non-rechargeable) battery connected to
VCC
pins should meet the following
prerequisites to comply with the module
VCC
requirements summarized in Table 6:
Maximum pulse and DC discharge current
: the non-rechargeable battery with its output circuit must be
capable of delivering to
VCC
pins the specified maximum peak / pulse current with 1/8 duty cycle, and a DC
current greater than the module maximum average current consumption (refer to the
SARA-G3
series Data
[1] or the
SARA-U2 series Data Sheet
[2]). The maximum pulse and the maximum DC discharge
current is not always reported in battery data sheets, but the maximum DC discharge current is typically
almost equal to the battery capacity in Amp-hours divided by 1 hour.
DC series resistance
: the non-rechargeable battery with its output circuit must be capable of avoiding a
VCC voltage drop greater than 400 mV during transmit bursts.
2.2.1.6
Additional guidelines for VCC supply circuit design
To reduce voltage drops, use a low impedance power source. The resistance of the power supply lines
(connected to the
VCC
and
GND
pins of the module) on the application board and battery pack should also be
considered and minimized: cabling and routing must be as short as possible to minimize power losses.
Three pins are allocated for
VCC
supply. Another twenty pins are designated for
GND
connection. It is highly
recommended to properly connect all the
VCC
pins and all the
GND
pins to supply the module, to minimize
series resistance losses.
To avoid voltage drop undershoot and overshoot at the start and end of a transmit burst during a single-slot 2G
voice/data call (when current consumption on the
VCC
supply can rise up to the maximum peak / pulse current
specified in the
SARA-G3
[1] or in the
SARA-U2 series Data Sheet
[2]), place a bypass capacitor
with large capacitance (more than 100 µF) and low ESR near the
VCC
pins, for example:
330 µF capacitance, 45 m
ESR (e.g. KEMET T520D337M006ATE045, Tantalum Capacitor)
The use of very large capacitors (i.e. greater then 1000 µF) on the
VCC
line should be carefully evaluated, since
the voltage at the
VCC
pins voltage must ramp from 2.5 V to 3.2 V in less than 1 ms to switch on the SARA-U2
modules or in less than 4 ms to switch on the SARA-G3 modules by applying
VCC
supply, that otherwise can be
switched on by forcing a low level on the
RESET_N
pin during the
VCC
rising edge and then releasing the
RESET_N
pin when the
VCC
supply voltage stabilizes at its proper nominal value.
To reduce voltage ripple and noise, especially if the application device integrates an internal antenna, place the
following bypass capacitors near the
VCC
pins:
100 nF capacitor (e.g Murata GRM155R61C104K) to filter digital logic noise from clocks and data sources
10 nF capacitor (e.g. Murata GRM155R71C103K) to filter digital logic noise from clocks and data sources
56 pF capacitor with Self-Resonant Frequency in 800/900 MHz range (e.g. Murata GRM1555C1E560J) to
filter transmission EMI in the GSM/EGSM bands
15 pF capacitor with Self-Resonant Frequency in 1800/1900 MHz range (e.g. Murata GRM1555C1E150J) to
filter transmission EMI in the DCS/PCS bands
A series ferrite bead for GHz band noise can be placed close to the
VCC
pins of the module for additional noise
filtering, but in general it is not strictly required, with the exception of SARA-U201 modules.
On SARA-U201 modules add the following component as close as possible to the
VCC
pins:
Ferrite bead specifically designed for EMI noise suppression in GHz band (e.g. Murata BLM18EG221SN1)
implementing the circuit described in Figure 46 to filter out EMI in all the GSM / UMTS bands. The ferrite
bead can be replaced with a 0 Ohm jumper for other SARA-G3 and SARA-U2 series modules.
For devices integrating an internal antenna, it is recommended to provide space to allocate all the
components shown in Figure 45 or Figure 46 and listed in Table 28. The mounting of each single
component depends on the specific application design.