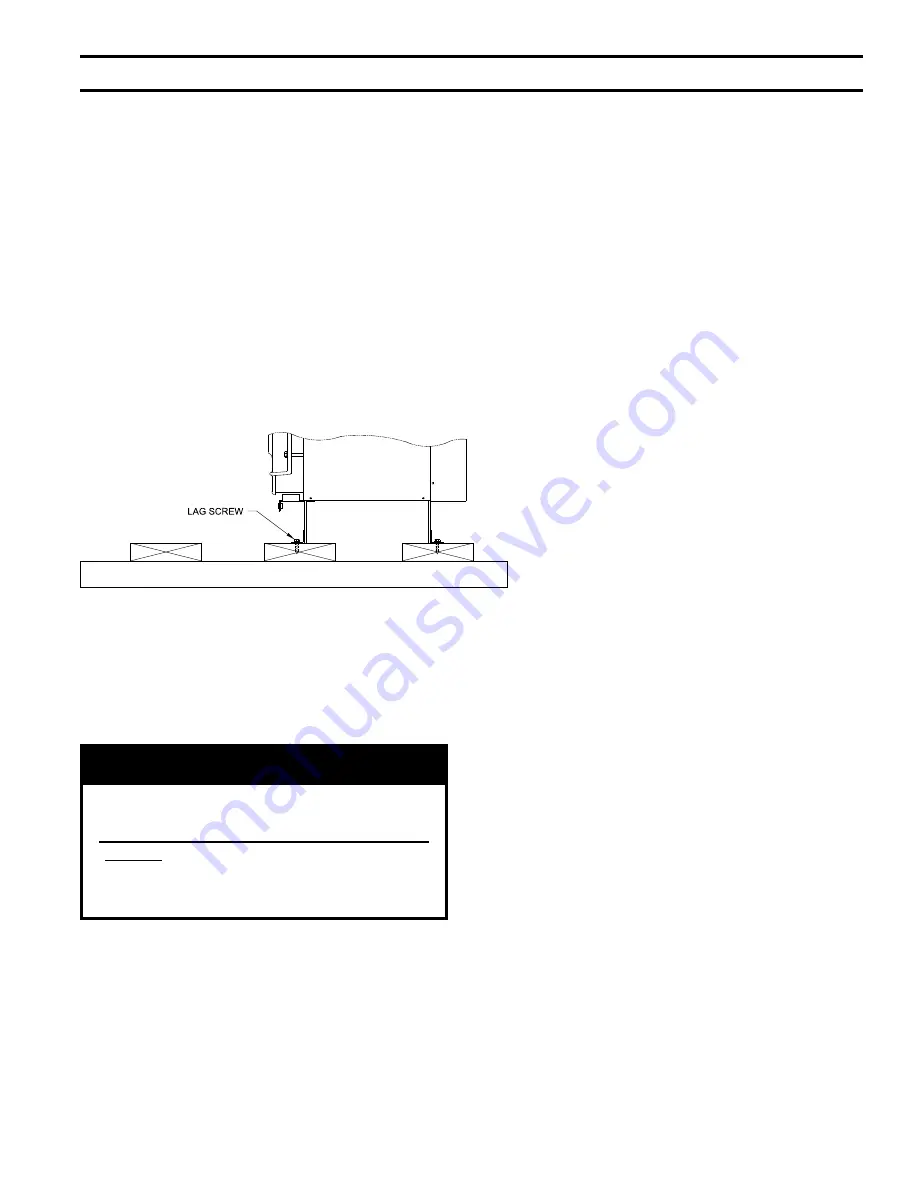
9
II. PRE-INSTALLATION (continued)
C.
REMOVE CRATE
1. Remove all fasteners at crate skid.
2. Lift outside container and remove all other inside
protective spacers and bracing. Remove parts bags
and Circulator Flange Kit from inside flue collar.
Parts bag contains Safety Relief Valve and Boiler
Drain Valve.
D.
REMOVAL OF BOILER FROM SKID
1. Tilt boiler, "walk" boiler backward, and set rear legs
down on floor. Tilt boiler backward, pull skid
forward and set front legs down on edge of skid.
Install close nipple, tee, and plug in return coupling
located between the legs on bottom of boiler shell.
See Figures 1A and 1B and Figures 8A and 8B.
Point tee toward permanent return location.
Figure 3: Legs Secured to Skid
2. Tilt boiler backward and remove skid. Be careful not
to damage Burner and Jacket.
E.
PROVIDE COMBUSTION AND VENTILATION
AIR. Local code provisions may apply and should be
referenced.
WARNING
Adequate combustion and ventilation air must
be provided to assure proper combustion and
to maintain safe ambient air temperatures.
DO NOT install boiler where gasoline or other
flammable vapors or liquids, or sources of
hydrocarbons (i.e. bleaches, fabric softeners,
etc.) are used or stored.
1. Determine volume of space (boiler room). Rooms
communicating directly with the space in which the
appliances are installed, through openings not
furnished with doors, are considered a part of the
space.
Volume(ft
3
) = Length(ft) x Width(ft) x Height(ft)
2. Determine total input of all appliances in the space.
Add inputs of all appliances in the space and round
the result to the nearest 1000 BTU per hour.
3. Determine type of space. Divide Volume by total input
of all appliances in space. If the result is greater than
or equal to 50 ft
3
/1000 BTU per hour, then it is
considered an
unconfined space
. If the result is less
than 50 ft
3
/1000 BTU per hour then the space is
considered a
confined space
.
4. For boiler located in an
unconfined space of a conven
-
tionally constructed building
, the fresh air infiltration
through cracks around windows and doors normally
provides adequate air for combustion and ventilation.
5. For boiler located in a confined space or an unconfined
space in a building of unusually tight construction,
provide outdoor air with the use of two permanent
openings which communicate directly or by duct with
the outdoors or spaces (crawl or attic) freely
communicating with the outdoors. Locate one opening
within 12 inches of top of space. Locate remaining
opening within 12 inches of bottom of space. Minimum
dimension of air opening is 3 inches. Size each opening
per following:
a.
Direct communication with outdoors.
Minimum
free area of 1 square inch per 4,000 BTU per hour
input of all equipment in space.
b.
Vertical ducts.
Minimum free area of 1 square inch
per 4,000 BTU per hour input of all equipment in
space. Duct cross-sectional area shall be same as
opening free area.
c.
Horizontal ducts.
Minimum free area of 1 square
inch per 2,000 BTU per hour input of all equipment
in space. Duct cross-sectional area shall be same
as opening free area.
Alternate method for boiler located within confined
space.
Use indoor air if two permanent openings
communicate directly with additional space(s) of
sufficient volume such that combined volume of
all spaces meet criteria for unconfined space. Size
each opening for minimum free area of 1 square
inch per 1,000 BTU per hour input of all equipment
in spaces, but not less than 100 square inches.
6. Louvers and Grilles of Ventilation Ducts
a. All outside openings should be screened and
louvered. Screens used should not be smaller
than 1/4 inch mesh. Louvers will prevent the
entrance of rain and snow.
b. Free area requirements need to consider the
blocking effect of louvers, grilles, or screens
protecting the openings. If the free area of the
louver or grille is not known, assume wood
louvers have 20-25 percent free area and metal
louvers and grilles have 60-75 percent free area.
c. Louvers and grilles must be fixed in the open
position, or interlocked with the equipment to
open automatically during equipment operation.
Содержание LE DV Series
Страница 5: ...5 I General Information Figure 1A LEDV Packaged Water Boiler with Beckett AFII Burner ...
Страница 6: ...6 I General Information continued Figure 1B LEDV Packaged Water Boiler with Riello BF Burner ...
Страница 19: ...19 v venting continued Figure 11 Vent Installation Figure 12 Vent Connector Un Assembled ...
Страница 20: ...20 v venting continued Figure 13 Vent Connector Assembled Figure 14 Air Intake Installation ...
Страница 48: ...48 xiii Repair Parts continued Figure 29 LEDV Bare Boiler Assembly ...
Страница 50: ...50 xiii Repair Parts continued Figure 30 LEDV Boiler Jacket Insulation ...
Страница 55: ...55 xiii Repair Parts continued Figure 33 Vent Kit Repair Parts ...
Страница 60: ...60 U S Boiler Company Inc P O Box 3020 Lancaster PA 17604 1 888 432 8887 www usboiler net ...