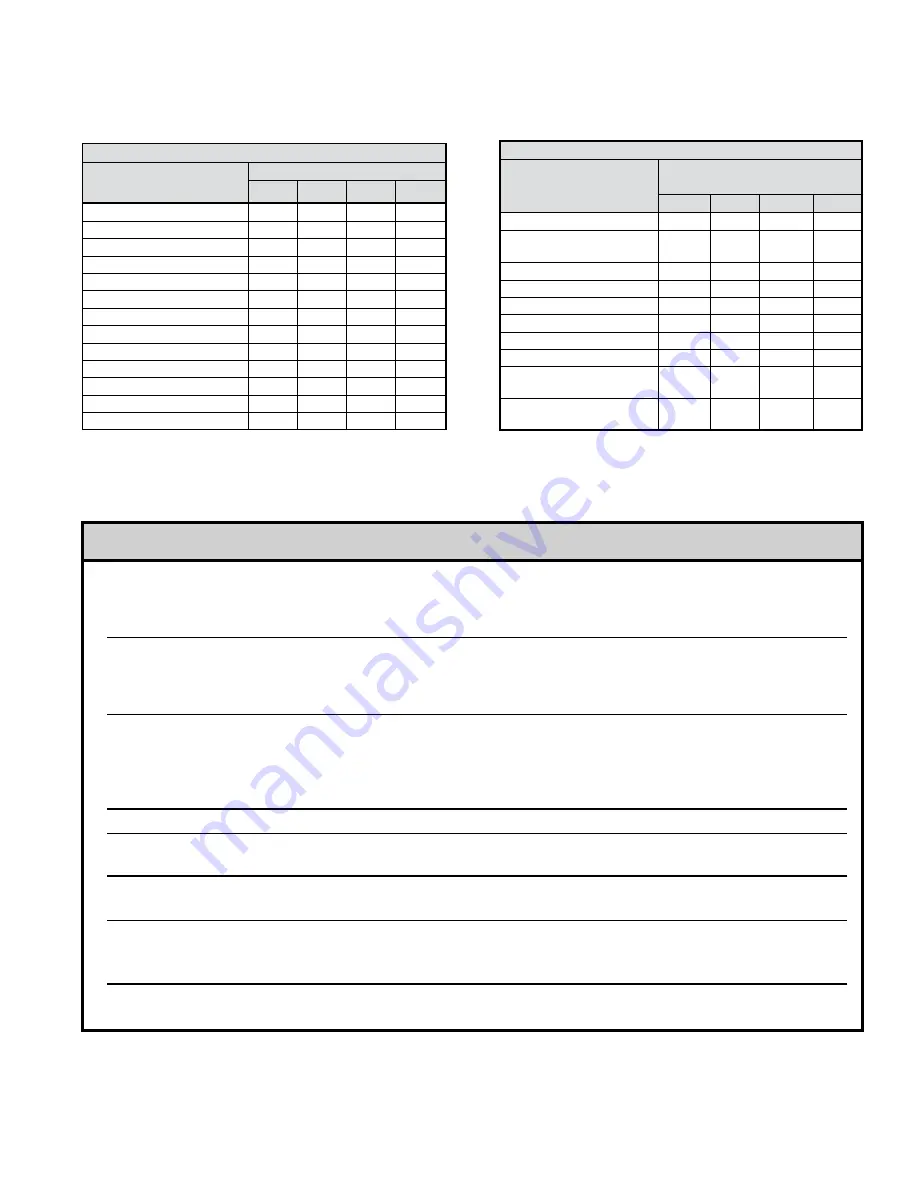
47
Vi. Water Piping and Trim
(continued)
Table 27: Fitting and Valve Equivalent Length
Copper Fitting and Sweat Valve Equivalent Length (Ft)
Fitting or Valve
Description
Copper Pipe or Valve Size
1
1¼
1½
2
90° Elbow
2.5
3.0
4.0
5.5
45° Elbow
1.0
1.2
1.5
2.0
Tee (through flow)
0.5
0.6
0.8
1.0
Tee (Branch flow)
4.5
5.5
7.0
9.0
Diverter Tee (typical)
23.5
25.0
23.0
23.0
gate Valve
0.3
0.4
0.5
0.7
globe Valve
25.0
36.0
46.0
56.0
angle Valve
5.3
7.8
9.4
12.5
Ball Valve (standard port)
4.3
7.0
6.6
14.0
Ball Valve (full port)
1.9
1.4
2.2
1.3
Swing Check Valve
4.5
5.5
6.5
9.0
Flow-Check Valve (typical)
54.0
74.0
57.0
177.0
Butterfly Valve
2.7
2.0
2.7
4.5
Threaded Fitting and Valve Equivalent Length (Ft)
Fitting or Valve
Description
Black Threaded Pipe or
Valve Size
1
1¼
1½
2
90° Elbow
2.6
3.5
4.0
5.2
Long radius
Elbow (45° or 90°)
1.4
1.8
2.2
2.8
Tee (through flow)
1.8
2.3
2.7
3.5
Tee (Branch flow)
5.3
6.9
8.1
10.0
Close return Bend
4.4
5.8
6.7
8.6
gate Valve (full open)
0.7
0.9
1.1
1.4
globe Valve (full open)
30.0
39.0
46.0
59.0
angle Valve (full open)
13.0
17.0
20.0
26.0
Swing Check Valve
(full open)
8.7
12.0
13.0
17.0
Flow-Check Valve
(typical)
42.0
60.0
63.0
83.0
Table 27: Fitting and Valve Equivalent Length
(cont’d)
NOTE: Table 27 is provided as reference to assist in piping design and specifies equivalent length of typical piping
fittings and valves.
nOTiCE
The alpine boiler heat exchanger is made from stainless steel tubular coil having relatively narrow
waterways. Once filled with water, it will be subject to the effects of corrosion. Failure to take the
following precautions to minimize corrosion and heat exchanger waterways overheating could result in
severe boiler damage.
•
Before connecting the boiler, insure the system is free of impurities, grease, sediment, construction
dust, sand, copper dust, flux and any residual boiler water additives. Flush the system thoroughly
and repeatedly, if needed, with clear water mixed with concentrated rinse agent to remove these
contaminants completely.
•
iron oxide (red oxide sludge Fe
2
O
3
) is produced during oxygenation. To minimize any oxygen pres-
ence in the system, the system must be air free and leak tight. Do not connect the boiler to radiant
tubing without an oxygen barrier. Using automatic water refill is not recommended, however, if such
refill is employed, a water meter must be added to evaluate the makeup water volume taken after ini
-
tial fill and eliminate any water leakage as early as possible.
•
Maintain the water pressure in the boiler at a minimum of 14.50 psi (100 kPa).
•
The boiler water pH must be within 7.5 < pH < 9.5. if the system contains any aluminum components,
pH must be less than 8.5.
•
Black oxide sludge (magnetite Fe
3
O
4
) forms as the result of continuous electrolytic corrosion in any
system not protected by an inhibitor.
•
Scale deposit is made up of lime scale contained in most distributed water and settles over the warm-
est surfaces of boiler heat exchanger causing subsequent overheating and eventual failure. Water
hardness must be maintained within 3 to 9 grain/gal range.
•
refer to Section Xi “Service and Maintenance” for recommended heating system water treatment products
(corrosion/scale inhibitors, cleaners etc) and their suppliers.
Содержание Alpine ALP500C
Страница 14: ...14 III Pre Installation and Boiler Mounting H Boiler Stacking continued Figure 5 Boiler Stacking ...
Страница 48: ...48 VI Water Piping and Trim continued Figure 28 Near Boiler Piping Heating Only ...
Страница 60: ...60 Figure 37 PCB Locations for Field Wiring Figure 38 120 VAC Field Wiring VIII Electrical continued ...
Страница 62: ...62 Figure 40 Ladder Diagram VIII Electrical continued ...
Страница 63: ...63 VIII Electrical continued 2 Figure 41 Wiring Connections Diagram ...
Страница 67: ...67 VIII Electrical continued Figure 45 Boiler to Boiler Communication with Zone Control Circulator Panel ...
Страница 72: ...72 IX System Start up continued Figure 48 Operating Instructions ...
Страница 124: ...124 XIII Repair Parts continued ...
Страница 126: ...126 XIII Repair Parts continued ALP600C ALP700C and ALP800C ALP800C shown ...
Страница 130: ...130 XIII Repair Parts continued ...
Страница 133: ...133 XIII Repair Parts continued 10A 10B 10C 10D 10G ...
Страница 143: ...143 ...
Страница 144: ...144 U S Boiler Company Inc P O Box 3020 Lancaster PA 17604 1 888 432 8887 www usboiler net ...