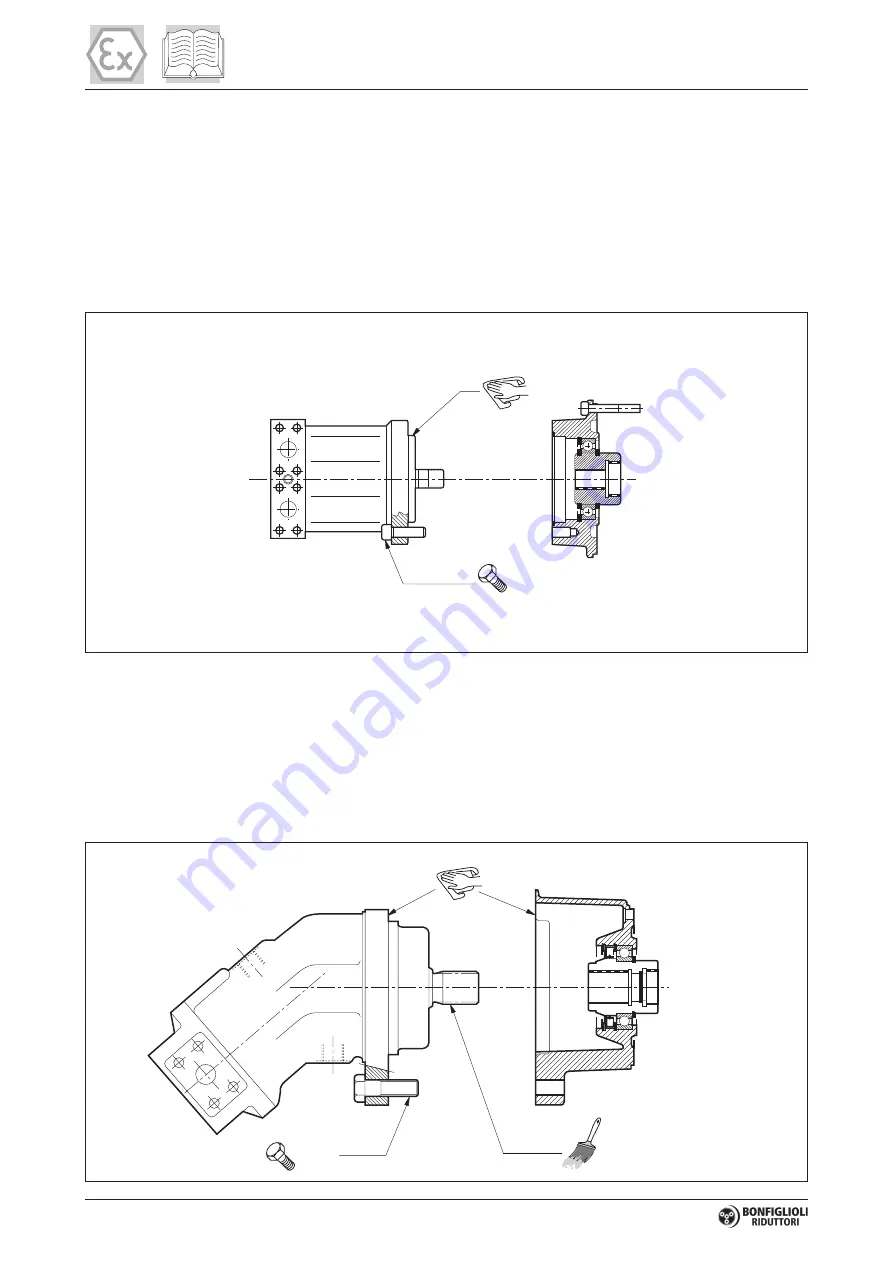
22
5.3 - INSTALLING THE HYDRAULIC MOTOR
Connecting the hydraulic motor
Remove the protective plug.
Hydraulic motor mountings are available in two versions:
a) Version with O-ring oil gasket between motor flange and gear unit.
In this case, mount the gasket to ensure an oil tight seal between the motor and gear unit, taking care to fit it
correctly in its seat without damaging it.
³
8.8
b) Version with gasket already mounted to the coupling.
In this case no special intervention is required to ensure an oil tight seal since this is already provided by the
motor coupling. Merely smear the motor shaft with grease.
In both cases, clean the spigot and the coupling where the motor is to be fitted, fit the motor and tighten
down the flange mounting bolts.
Always use bolts rated to at least class 8.8.
³
8.8
Содержание DP20-4H
Страница 11: ......
Страница 12: ......
Страница 26: ......
Страница 27: ......
Страница 28: ......
Страница 29: ......
Страница 30: ......
Страница 31: ......
Страница 32: ......
Страница 33: ......
Страница 34: ......
Страница 35: ...Service Manual Variable Displacement Pumps MP1 powersolutions danfoss com ...
Страница 93: ...Service Manual MP1 Danfoss July 2017 AX00000244en US0103 59 ...
Страница 94: ...Service Manual MP1 60 Danfoss July 2017 AX00000244en US0103 ...
Страница 95: ...Service Manual MP1 Danfoss July 2017 AX00000244en US0103 61 ...
Страница 110: ......
Страница 111: ......
Страница 112: ......
Страница 113: ......
Страница 115: ......
Страница 154: ......
Страница 156: ...www dexteraxle com OPERATION MAINTENANCE SERVICE MANUAL 600 8 000 lb Axles Related Components ...
Страница 238: ...Service Record Date Service Performed Mileage ...
Страница 239: ...Service Record Date Service Performed Mileage ...
Страница 240: ...Service Record Date Service Performed Mileage ...