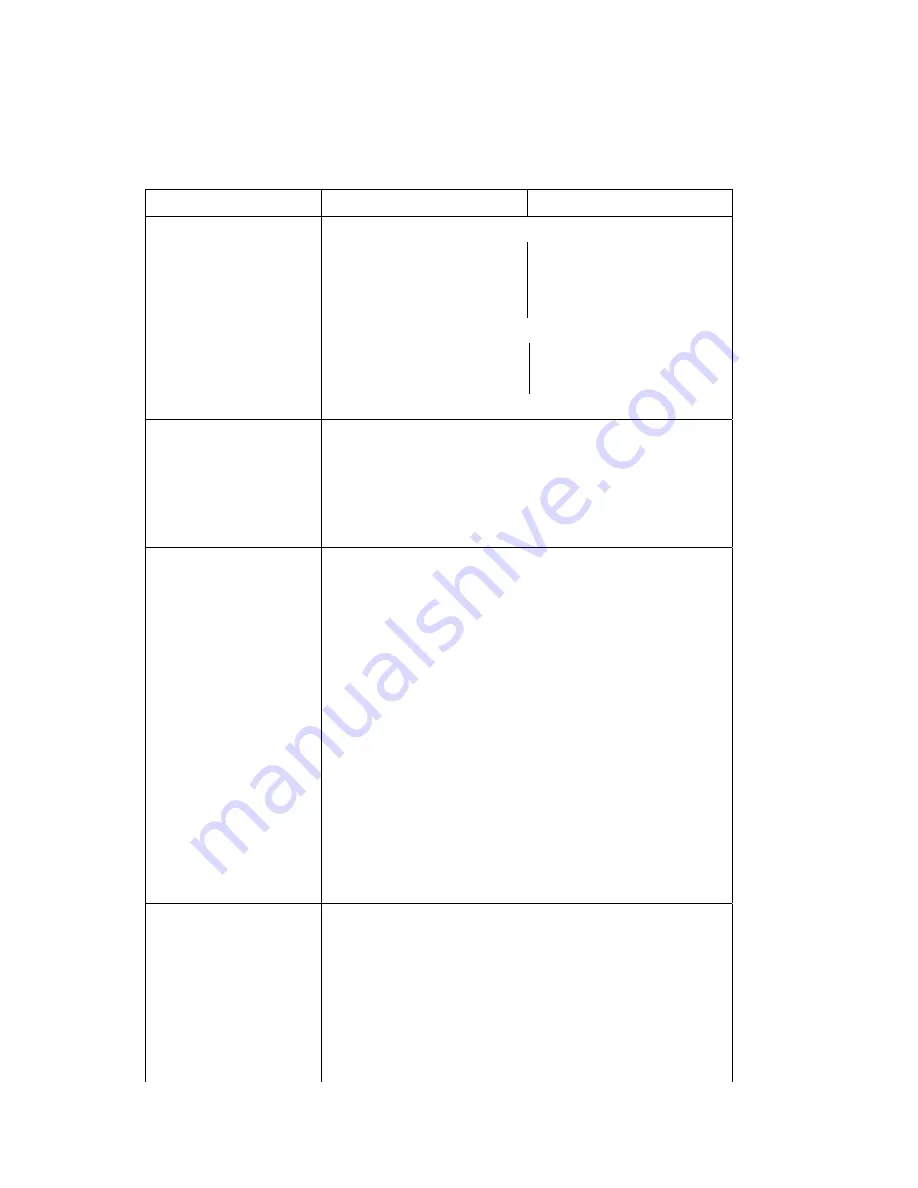
30
7. Specifications
7.1 Printer Specifications
Item TTP-245 TTP-343
Mechanism
Resolution 203
dpi
300 dpi
Max. Print Width
108 mm
104 mm
Max. Print Length
1000 mm ( 39” )
420 mm (16.53”)
Ribbon Capacity
300 meter with 1” core (Max. OD 67 mm)
Printing Speed
2, 3, 4 and 5 ips
2, 3 ips
Peeler function
2, 3 ips
2 ips
Printing Method
Direct thermal and thermal transfer printing.
Enclosure
Structure
Dimension
Operation Panel
Double-walled plastic.
Standard Model: 314mm(L) x 213mm(W) x 188mm(H)
One push switch, and one indicator LED (Green,
Orange, Red colors).
Hardware
Sensor
Transmissive sensor (offset 6 mm from liner
edge).
Reflective sensor (position adjustable).
Head open micro switch.
Ribbon end sensor
Memory
2M byte Flash memory
2M bytes DRAM
Interface
RS-232C (max baud rate, 19,200 bps).
USB: V1.1.
Centronics.
Power
AC input: 100-240V universal auto switching power
supply.
DC output: 24V 3.75A.
Firmware
Font Type
8 alpha-numeric bitmap fonts, and 1 true type font.
Rotation
0, 90,180 and 270 degrees.
Barcode Format
1D Bar code
Code 39, Code 93, Code 128UCC, Code128 subsets
A.B.C, Codabar, Interleave 2 of 5, EAN-8, EAN-13,
EAN-128, UPC-A, UPC-E, EAN and UPC2(5) digits
Содержание TTP-245 series
Страница 1: ...USER S MANUAL TTP 245 343 THERMAL TRANSFER DIRECT THERMAL BAR CODE PRINTER ...
Страница 3: ...ii Update History 35 ...
Страница 5: ...2 8 Dieses das Gerät kann bis zu einer Außentemperatur von maximal 40 betieben werden ...
Страница 31: ...26 5 blinks red amber 5 blinks solid green 4 Printer will be interrupted to run the AUTO BAS program ...