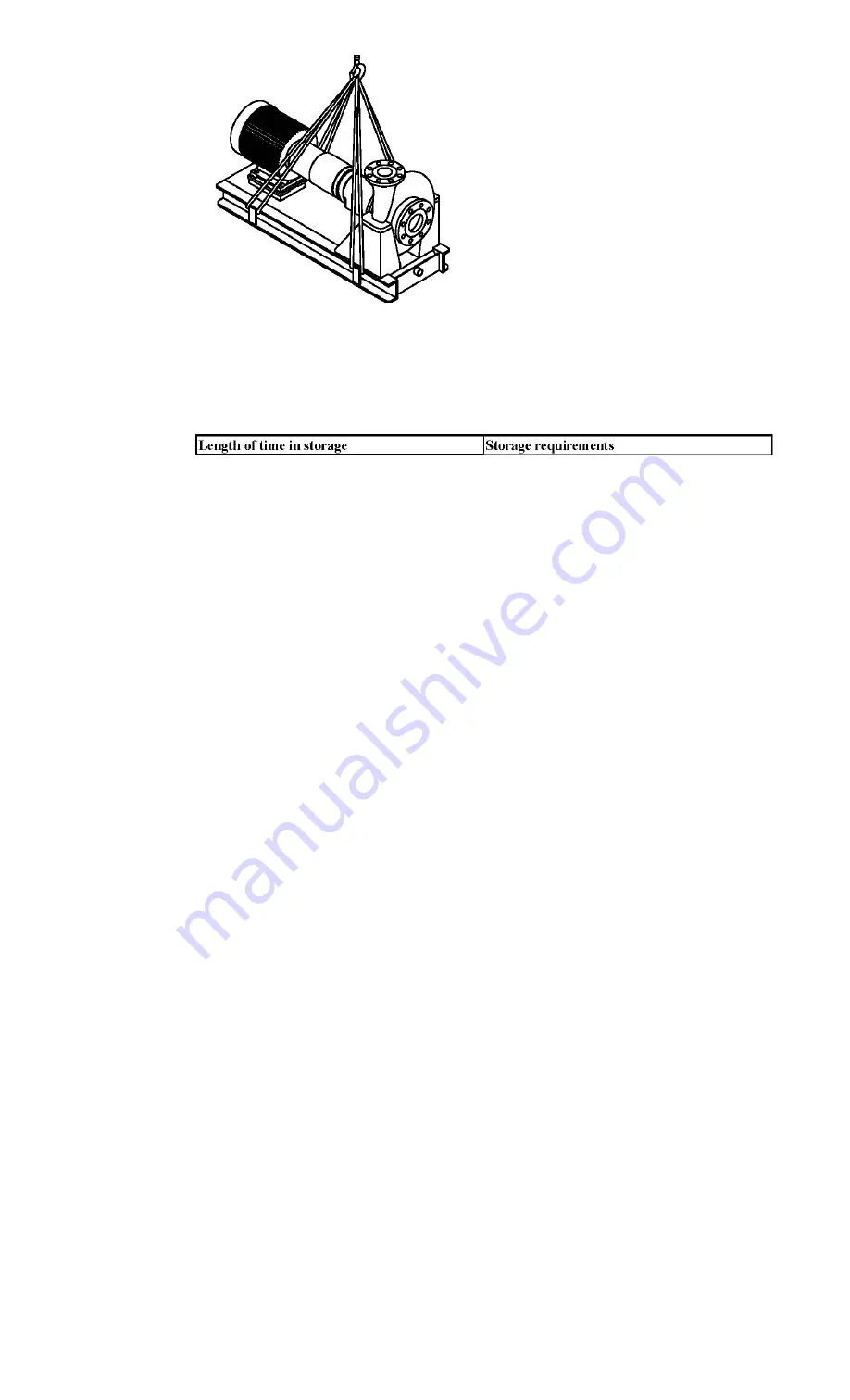
Revision
8
–
November
2011
13
Figure 3: Proper lifting method
Pump storage requirements
Storage requirements are dependent on the amount of time the pump is stored. The normal packaging is
designed only to protect the pump during shipping.
Treat bearing and machined surfaces so that they are well preserved. Refer to drive unit and coupling
manufacturers for their long-term storage procedures. You can purchase long-term storage treatment with the
initial pump order or you can purchase it and apply it after the pumps are already in the field. Contact your local
TRUFLO sales representative.
•
Store in a covered and dry location.
•
Store the unit free from dirt and vibrations.
•
Store in a covered and dry location.
•
Store the unit free from heat, dirt, and vibrations.
•
Rotate the shaft by hand several times at least every three months.
Содержание TSMP Series
Страница 3: ...Revision 8 November 2011 3 PAGE SECTION...
Страница 12: ...12 Revision 8 November 2011 Examples Figure 1 Proper lifting method Figure 2 Proper lifting method...
Страница 37: ...Revision 8 November 2011 37...
Страница 46: ...46 Revision 8 November 2011 Assemble is reverse sequence of disassemble...
Страница 54: ...54 Revision 8 November 2011 SECTIONAL Drawing of Typical TSMP...
Страница 63: ...Revision 8 November 2011 63...