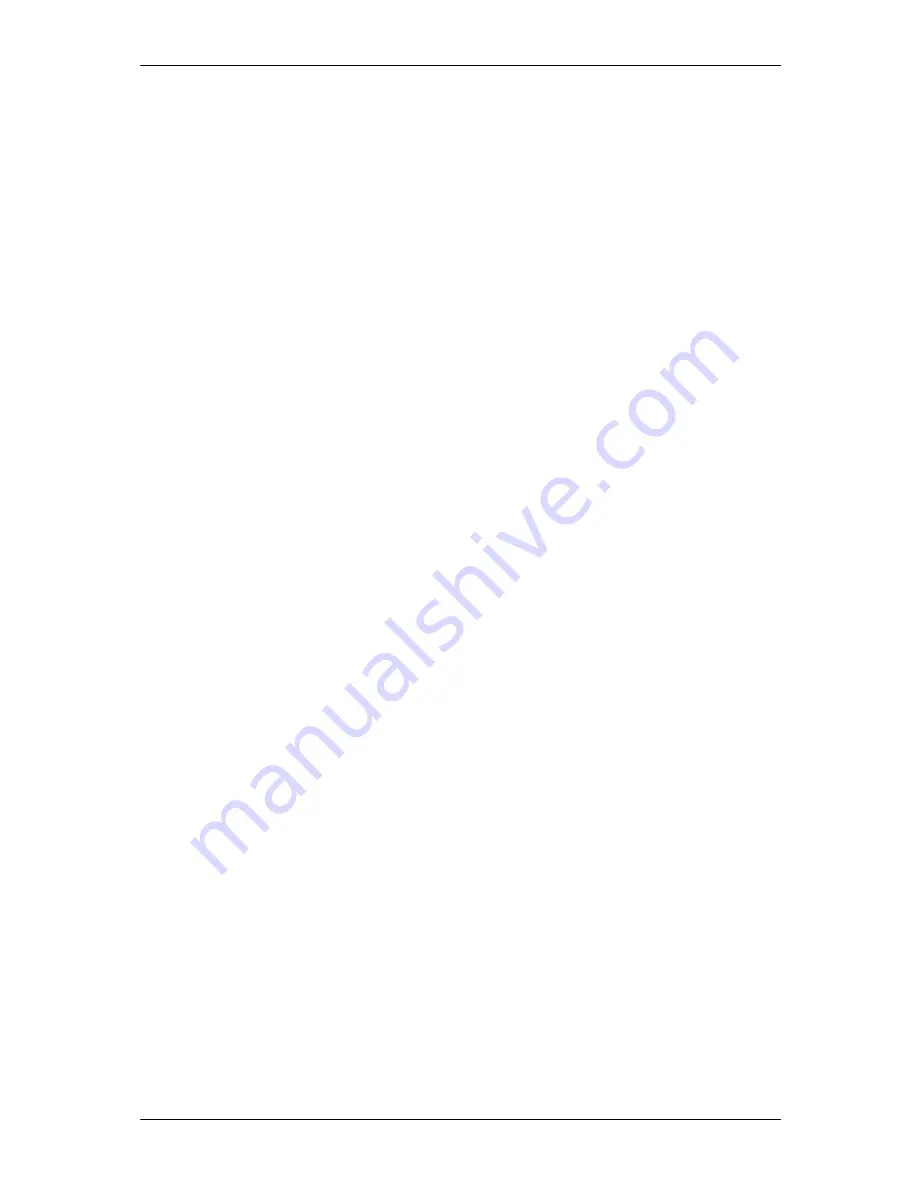
PDx-170-57-E / TMCM-170 Hardware Manual (V1.10 / 2011-NOV-24)
4
Copyright © 2011, TRINAMIC Motion Control GmbH & Co. KG
2
Features
The PD-170-57 is a combination of an intelligent BLDC servo motor controller / driver, an optical
encoder and a 57mm brushless DC motor. As a controller/driver module the TMCM-170 has been
designed for high performance servo drives based on brushless DC motors. It combines the high
resolution known from stepper motors with the high dynamic, high velocity and high reliability of a
BLDC drive. A build-in ramp generator allows parameterized smooth positioning. Its small form factor
allows direct mounting on / into a motor-encoder assembly. The TMCM-170 supports BLDC motors
with nearly any number of poles and incremental encoders with nearly any resolution. The TMCM-170
integrates a position and a velocity regulator.
The module can be remote controlled via an RS232 or RS485 interface (ordering options) and CAN
interface.
Applications
Replacement of servo drive by high reliability / low cost BLDC drive
Fast and precise positioning
Smooth very low to very high constant / variable velocity drives
Very high velocity stability drives
Extremely compact decentralized motor electronics
Motor / Encoder type
Sine (or block) commutated BLDC motors with encoder and with / without additional hall sensors
Hall sensor based motors can be operated without encoder
Motor power from a few watts to 500W
Motor velocity up to 100,000 RPM (electrical field)
Incremental encoder (2 channel with option for N-channel) with resolution from 256 to 30000 /
motor rotation (opt. per electrical field rotation)
12V to 48V nominal motor voltage
Coil current up to 10A nominal (up to 14A current for short time)
PANdrive™ Motor and Encoder data
Motor: TRINAMICs QBL 5704-94-04-032 or QBL 5704-116-04-042, rated torque 0.32 Nm or 0.42 Nm
Encoder: HEDS-5640-A12 with resolution of 2000 per motor rotation
Please refer to the datasheets for detailed motor and encoder information
Highlights
High-efficiency operation, low power-dissipation
CAN interface and RS232 or RS485 integrated
Integrated Protection: reverse polarity and overload / overtemperature / overvoltage
TRINAMIC TMCL™ protocol and TMCL™ software environment for parameterizing and for update
and for programming of standalone mode
1024 entry 10 bit motor sine commutation table
External (stop) switch or encoder N channel can be used for absolute position reference
Different start up modes for automatic commutation calibration