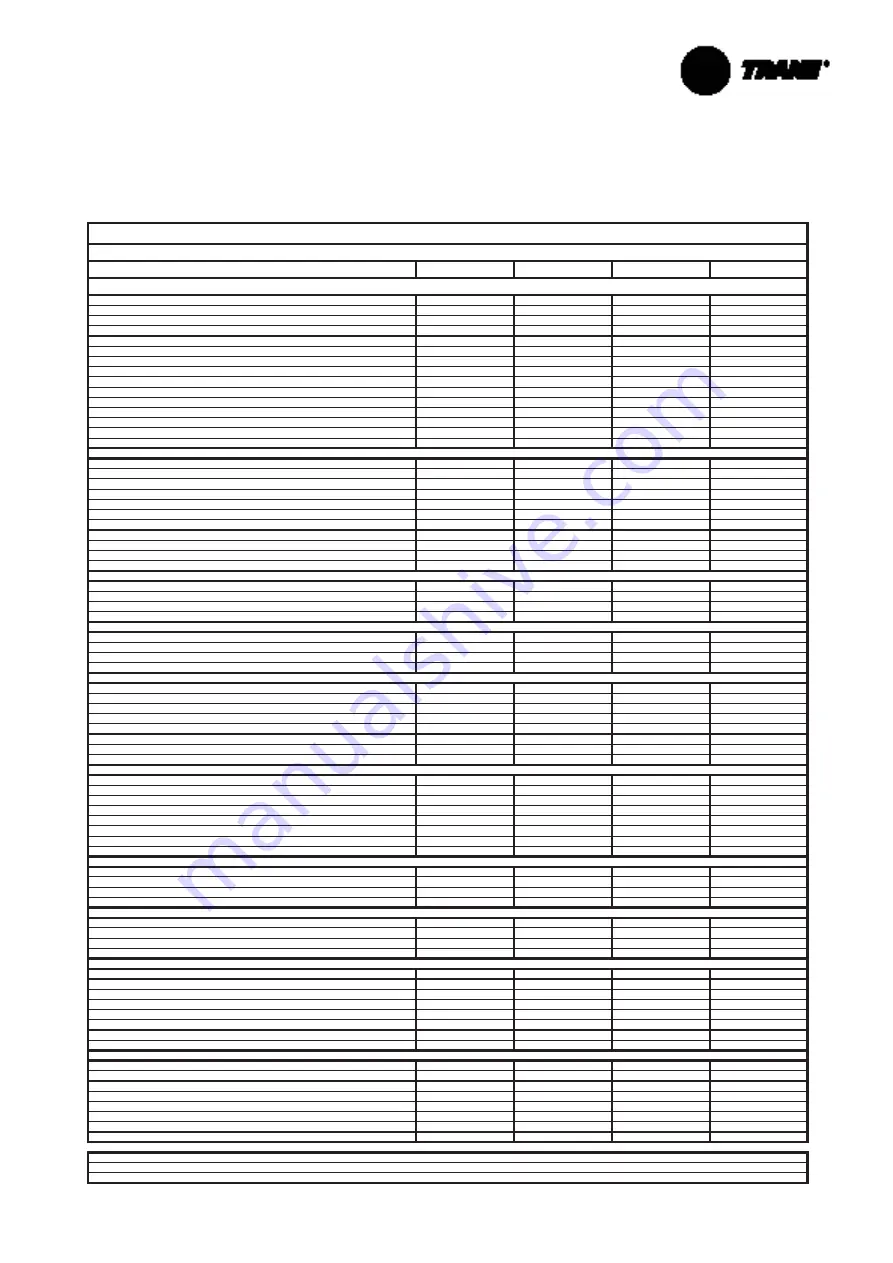
RLC-SVX19J_SHORT-GB
45
The operator log sheet are included for use as appropriate, for installation completion verifi cation before
Trane Start-up is scheduled, and for reference during the Trane Start-up.
Operator Log
Sintesis RTAF chiller with UC800 Controller - Tracer AdaptiView Reports - Log Sheet
Start
15 minutes
30 minutes
1 hour
Evaporator
Active Chilled Water Setpoint
Entering Water Temperature
Leaving Water Temperature
Ckt 1
Saturated Refrigerant Temperature (°C)
Refrigerant Pressure (kPa)
Approach Temperature (°C)
Water
fl
ow Status
EXV % Open
Ckt 2
Saturated Refrigerant Temperature (°C)
Refrigerant Pressure (psia)
Approach Temperature (°C)
Water
fl
ow Status
EXV % Open
Condenser
Outdoor Temperature
Ckt 1
Air
fl
ow (%)
Saturated Refrigerant Temperature (°C)
Refrigerant Pressure (kPa)
Subcooling in °C
Ckt 2
Air
fl
ow (%)
Saturated Refrigerant Temperature (°C)
Refrigerant Pressure (kPa)
Subcooling in °C
Compressor 1A
Running Status
Starts
Running Time (Hr:min)
Oil Pressure (kPa)
Compressor 1B
Running Status
Starts
Running Time (Hr:min)
Oil Pressure (kPa)
Motor 1A
Active Demand Limit Setpoint
Average Motor Current (%)
Percent Speed
AFD Average Input Current (Amps)
AFD Average Input Voltage (Volts)
AFD Input Power (KW)
AFD Output Power (KW)
AFD Speed (rpm)
Motor 1B
Active Demand Limit Setpoint
Average Motor Current (%)
Percent Speed
AFD Average Input Current (Amps)
AFD Average Input Voltage (Volts)
AFD Input Power (KW)
AFD Output Power (KW)
AFD Speed (rpm)
Compressor 2A
Running Status
Starts
Running Time (Hr:min)
Oil Pressure (psia)
Compressor 2B
Running Status
Starts
Running Time (Hr:min)
Oil Pressure (psia)
Motor 2A
Active Demand Limit Setpoint
Average Motor Current (%)
Percent Speed
AFD Average Input Current (Amps)
AFD Average Input Voltage (Volts)
AFD Input Power (KW)
AFD Output Power (KW)
AFD Speed (rpm)
Motor 2B
Active Demand Limit Setpoint
Average Motor Current (%)
Percent Speed
AFD Average Input Current (Amps)
AFD Average Input Voltage (Volts)
AFD Input Power (KW)
AFD Output Power (KW)
AFD Speed (rpm)
Date:
Technician:
Owner:
Log Check Sheet