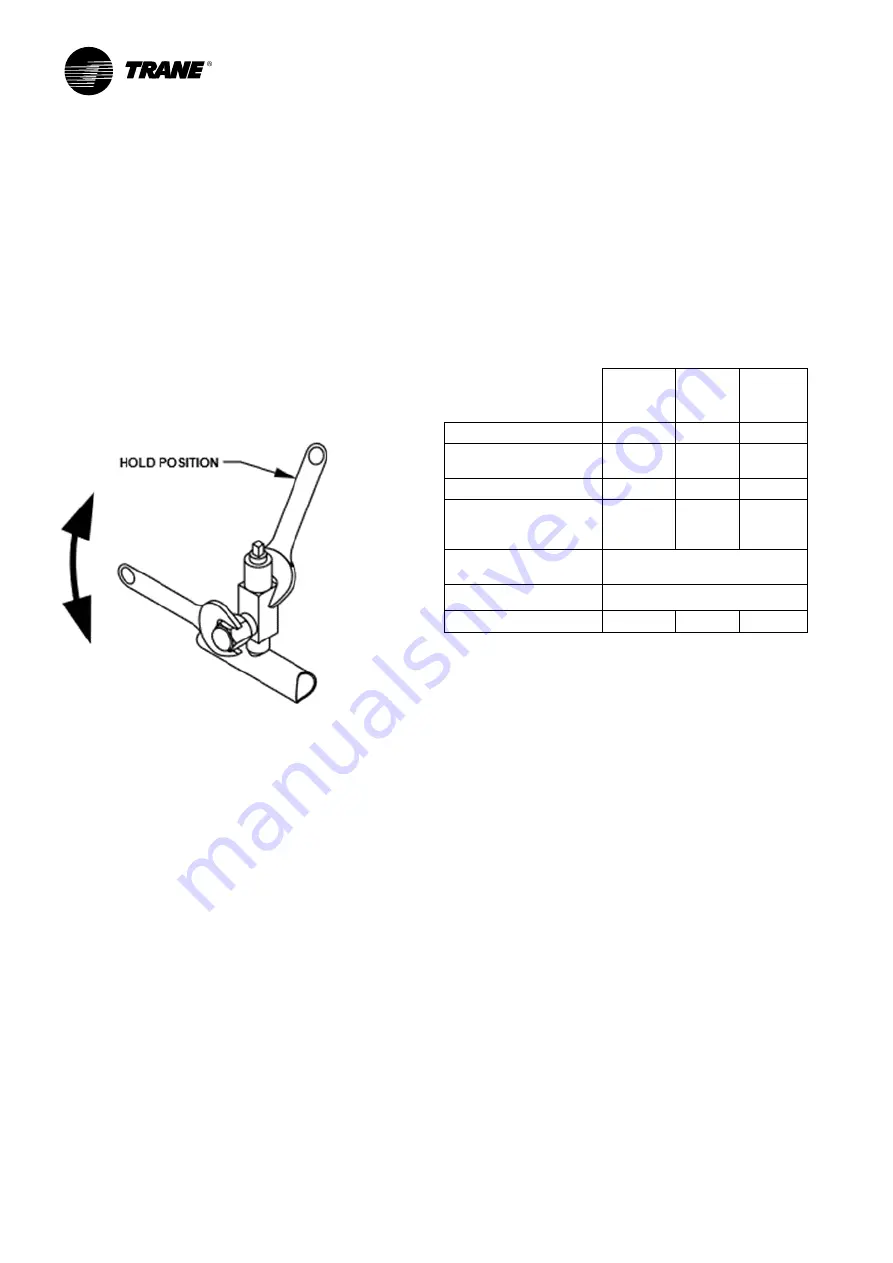
4
UNT-PRC002-GB
Technical Data
FWD
08
12
20
30
45
Power supply
(V/Ph/Hz)
230/1/50
Capacities
Cooling capacity on water (1)
(kW)
5,2
8,3
15
18,8
30,1
Heating capacity on water (2)
(kW)
6,3
11,9
18,9
20,9
38,2
Fan motor
(type)
2 x direct drive centrifugal
Fan power input (3)
(kW)
0,23
0,46
0,65
1,04
1,51
Current amps (3)
(A)
1,1
2,2
3,1
4,7
5,5
Start-up amps
(A)
3,2
5,5
9,3
14,1
16,5
Air flow
minimum
(m
3
/h)
490
980
1400
1800
2700
nominal
(m
3
/h)
820
1650
2300
3000
4500
maximum
(m
3
/h)
980
1970
2600
3600
5400
Main coil
Water entering/leaving connections
(type)
ISO R7 rotating female
(Dia)
3/4"
3/4"
1 1/2"
1 1/2"
1 1/2"
Electric heater (accessory for blower only)
Electric power supply
(V/Ph/Hz)
230/1/50
230/1/50 or 400/3/50
400/3/50
400/3/50
400/3/50
Heating capacity
(kW)
2/4
8
10
12
12
Hot water coil (accessory for blower only)
Heating capacity (4)
(kW)
6,3
12
17,4
22,4
34,5
G2 filter (filter box accessory)
Quantity
2
2
2
2
2
Dimensions ( LxWxth)
(mm)
386x221x8
486x271x8
586x321x8
586*421*8
586*621*8
G4 filter (filter box accessory)
Quantity
-
2
2
2
2
Dimensions ( LxWxth)
(mm)
-
486x264x48
586x314x48
586*414*48
586*614*48
Condensate pump (accessory)
(type)
Centrifugal
Water flow - lift height
(l/h - mm)
24 - 500
Not available for FWD30 and FWD45
Sound level (L/M/H speed)
Sound pressure level (5)
(dB(A))
36/40/43
38/41/44
46/50/53
47/52/57
47/52/58
Sound power level (5)
(dB(A))
46/50/53
48/51/54
56/60/63
57/62/67
57/62/68
Unit dimensions
Width x Depth
(mm)
890 x 600
1090 x 710
1290 x 820
1290 x 970
1290 x 1090
Height
(mm)
250
300
350
450
650
Shipped unit dimensions
Width x Depth
(mm)
933 x 644
1133 x 754
1333 x 864
1333 x 1008
1333*1133
Height
(mm)
260
310
360
460
660
Weight
(kg)
32
46
61
76
118
Colour
galvanised steel
Recommended fuse size
Unit alone (aM/gI)
(A)
8/16
8/16
8/16
8/25
8/25
Unit with electric heater (gI)
(A)
16 (2kW),25 (4kW)
40 (230V),3*16 (400V)
3*20
3*25
3*25
(1) Conditions: Water entering/leaving temperature: 7/12 °C, Air inlet temperature 27/19°C DB/WB - Nominal air flow
(2) Conditions: Water entering/leaving temperature: 50/45 °C, Air inlet temperature 20°C DB - Nominal air flow
(3) At high speed with nominal air flow.
(4) Water entering/leaving temperature 90/70 °C, air inlet temperature 20 °C DB, Nominal air flow.
(5) A rectangular glass wool duct 1m50 long is placed on the blower.The measurement is taken in the room containing the blower unit.
Heat exchanger operating limits:
FWD:
*water temperature: max 100° C
*absolute service pressure: min 1 bar/max 11 bars
Accessories - Hot water coil:
*water temperature: min. +2° C/max. 100° C
*absolute service pressure: min 1 bar/max 11 bars
CG-SVX051A-GB
58
Periodic Maintenance
General
Perform all maintenance procedures and inspections at
the recommended intervals. This will increase the life
of the unit and minimize the possibility of serious and
costly breakdown.
Use an “Operator’s Log” to record the unit’s operating
history. The log serves as a valuable diagnostic tool for
service personnel. By observing trends in operating
conditions, an operator can anticipate and prevent
problem situations before they occur. If the unit is not
operating properly during maintenance inspections,
consult the “Diagnostic and Troubleshooting” section of
this manual. Proper servicing of the service valves is
required. Use a backup wrench as shown in Figure when
loosening or tightening the service valve cap.
Figure 23 - Servicing of service valves
Weekly Maintenance
After the unit has been operating for approximately
30 minutes and the system has stabilized, check the
operating conditions and complete the procedures
below:
1. Check on the TD7 pressure for chilled/hot water
exchangers, and intermediate oil.
Note:
Pressures are referenced at sea level.
2. Inspect the entire system for unusual conditions and
inspect the condenser coils for dirt and debris. If the
coils are dirty, refer to coil cleaning.
Check the electronic expansion valve sight glasses.
Note:
The electronic expansion valve is commanded
closed at unit shutdown and if the unit is off, there will
be no refrigerant flow through the sight glasses. Only
when a circuit is running will refrigerant flow be present.
The refrigerant flow through the sight glasses should
be clear. Bubbles in the refrigerant indicate either low
refrigerant charge or excessive pressure drop in the
liquid line. A restriction in the line can sometimes be
identified by a noticeable temperature differential
between the two sides of the restriction. Frost may often
form on the liquid line at this point. Correct refrigerant
charges is shown in nameplate.
NOTICE:
A clear sight glass alone does not mean that
the system is properly charged. Also check the system
superheat, subcooling and unit operating pressures.
NOTICE:
Use only manifold gauge sets designed for use
with R410A refrigerant.
Use only recovery units and cylinders designed for the
higher pressure of R410A refrigerant and POE oil.
NOTICE:
R410A must be charged in a liquid state.
Check the system superheat, subcooling, chilled/hot
water exchanger temperature drop (Delta-T), water flow
rates, approach temperatures, compressor discharge
superheat, and compressor RLA.
Normal operating conditions are :
Table 12 – Typical approaches / pressures
Cooling
mode
Heat
pump
mode
Heat
Recovery
Mode
Typical Air Temperature
35 °C
7 °C
whatever
Typical leaving water
temperature
7 °C
45 °C
7 / 45 °C
Suction approach
3 to 5 K
8 to 12 K
3 to 5 K
"Discharge approach with :
- approx. 5K water delta T
- approx. 10K water delta T"
"14 to 20 K" "0 to 2 K
-3 to -1 K"
"0 to 2 K
-3 to -1 K"
Compressor Suction
Superheat
5 to 6 K
EXV Liquid Subcooling
4 to 6 K
EXV opening
55 to 65%
50 to 60% 60 to 70%
Note:
CMAF is common with service valves, ensure
the re-opening of them (Item 12 in Refrigerant system
schematic & Oil lube circuit schematic) after refrigerant
transfer.
Note:
If the superheat is unstable, check the suction
temperature sensor. The sensor should be well inserted
into the well and thermal grease should be used to
ensure a good contact between the sensor and the well.
The sensor must be wrapped with insulation as well.
If operating pressures and sight glass conditions seem
to indicate a refrigerant shortage, measure the system
superheat and subcooling. Make sure the drain valve is
well open.
Note:
If the subcooling is unstable, check the liquid
temperature sensor. The sensor shall be well inserted
into the well and thermal grease shall be used to ensure
a good contact between the sensor and the well. The
sensor must be wrapped with insulation as well.
If operating conditions indicate a refrigerant overcharge,
make sure the fill up valve is well open, remove
refrigerant at the liquid line service valve.
Allow refrigerant to escape slowly to minimize oil loss.
Use a refrigerant recovery cylinder and do not discharge
refrigerant into the atmosphere.
WARNING!
Do not allow refrigerant to directly contact
skin as injury from frostbite may result.