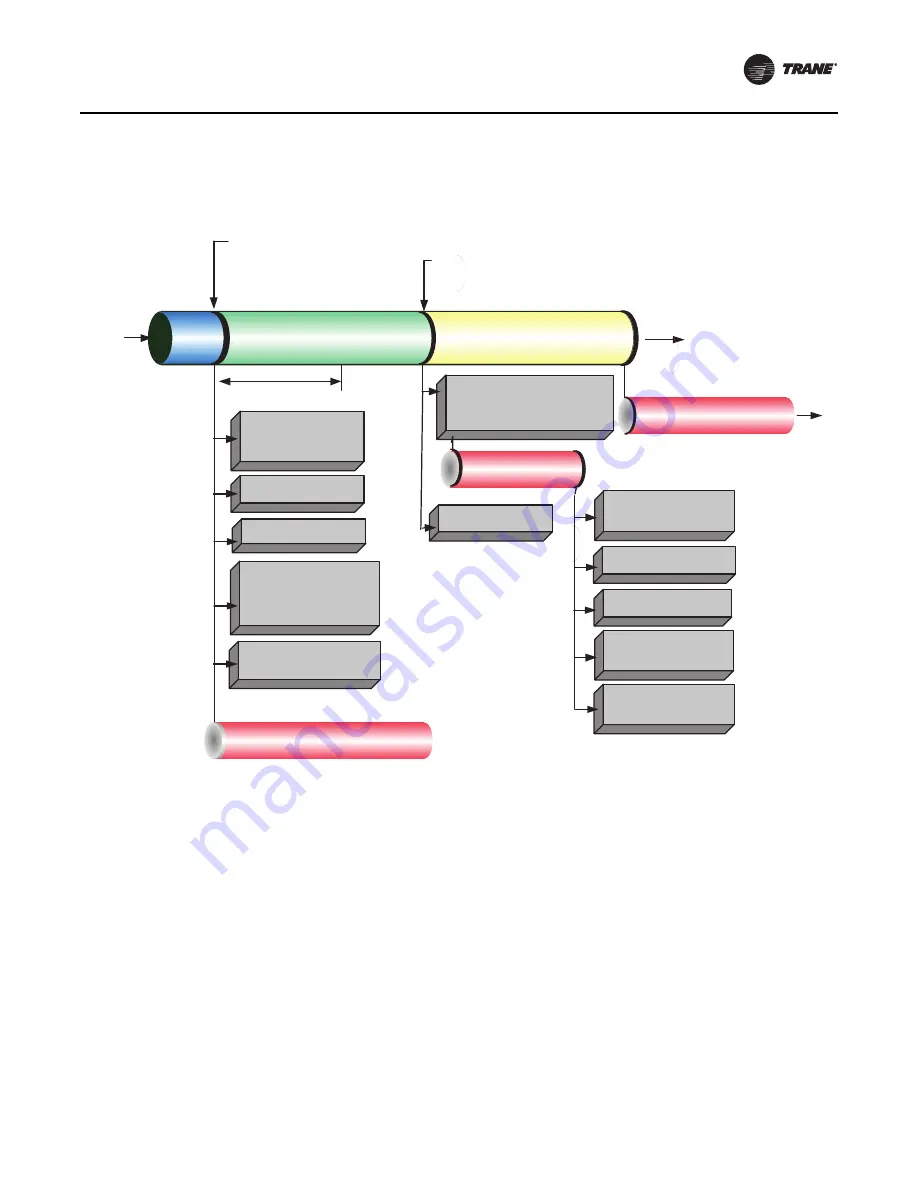
Start-Up and Shutdown
RTAF-SVX001K-EN
71
Ice Making (Auto to Ice Making to Ice Making Complete)
The figure below shows the transition from Auto to Ice
making, to Ice Making Complete.
Figure 49.
Sequence of events: ice making (auto to ice making to ice making complete)
Confirm No
Compressor Currents
g
pp
g
p
Auto
Evap Entering Water
Temp Falls Below the
Ice Termination Setpoint
Run Inhibit –
Submode: Ice
Building Complete
Running
(Unit is Building Ice)
Ice Making Command:
1. Front Panel
2. Tracer
3. External Input
Auto
Shutting Down
Maximum 1:10 to fully
loaded
Run Unload, Close EXVs and
Perform Operational Pumpdown
(if reqd) then Shutoff
Compressors, Energize Heaters
Enforce All Non- Running
Mode Diagnostics
will return to “Auto” and normal cooling
mode with removal of Ice Command
Stage and modulate all
compressors in
sequence to full load
(if not already)
Ignore Softloading and
Set CLS =100%
Energize Ice Building
Relay
Enforce All Limits and
Running Mode Diagnostics
De-energize Heaters,
Control EXVs and Oil
Return Solenoids per
Normal Staging - See other
sequence diagrams
Control Circuit’s
Condenser Fans for Diff
Pressure
Turn off both Circuits’
Condenser Fans
Leave EXVs Closed or
Close EXV for Circuits’
Off Cycle
De-Energize Oil Return
Drain and Fill Solenoids
De-Energize Evaporator
Water Pump Relay (no
delay time applied)
De-Energize Ice
Building Relay
Automatic Evaporator
Isolation Valve control
may close valve