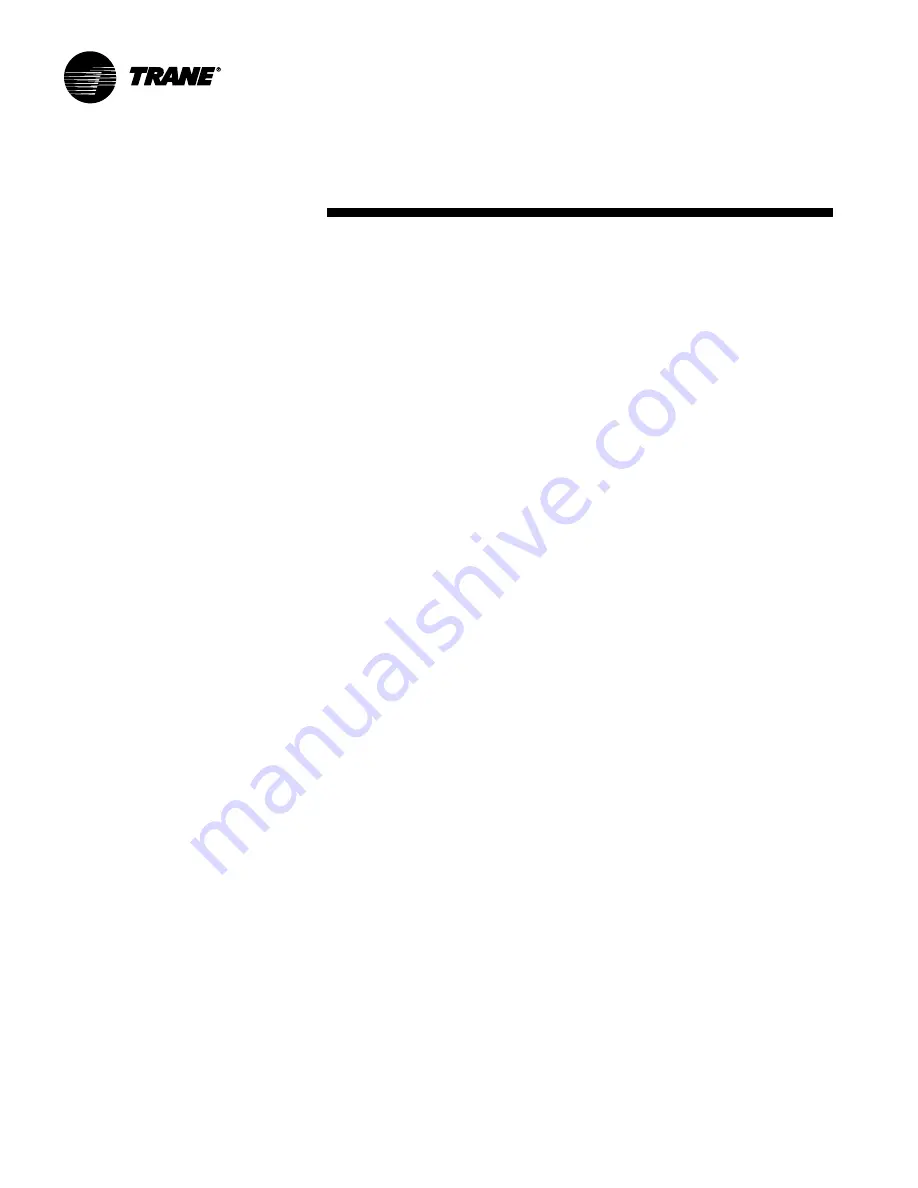
4
LPC-SVX01C-EN
General
Packaged Climate Changer
units are
draw-through air handlers that are
designed for cooling and/or heating
conditions of 1,500 to 15,000 nominal cfm.
Basic unit components consist of coil(s),
condensate drain pan, filter, one fan
wheel, motor and drive.
Unit control options range from the
simple control interface for field-mounted
controllers to the sophisticated Tracer
AH540. For more information on the
Tracer AH540 controls, see the Operation
section of this manual.
Refrigerant Handling
Procedures
Environmental Accountability Policy
Trane urges that all HVAC servicers to
make every effort to eliminate, if possible,
or vigorously reduce the emission of CFC,
HCFC, and HFC refrigerants to the
atmosphere. Always act in a responsible
manner to conserve refrigerants for
continued usage even when acceptable
alternatives are available.
Recover and Recycle Refrigerants
Never release refrigerant to the
atmosphere! Always recover and/or
recycle refrigerant for reuse,
reprocessing (reclaimed), or properly
dispose if removing from equipment.
Always determine the recycle or reclaim
requirements of the refrigerant before
beginning the recovery procedure. Obtain
a chemical analysis of the refrigerant if
necessary. Questions about recovered
refrigerant and acceptable refrigerant
quality standards are addressed in ARI
Standard 700.
general
information
Refrigerant Handling and Safety
Consult the manufacturer’s material
safety data sheet (MSDS) for information
on refrigerant handling to fully
understand health, safety, storage,
handling, and disposal requirements. Use
the approved containment vessels and
refer to appropriate safety standards.
Comply with all applicable transportation
standards when shipping refrigerant
containers.
Service Equipment and Procedures
To minimize refrigerant emissions while
recovering refrigerant, use the
manufacturer’s recommended recycling
equipment per the MSDS. Use
equipment and methods which will pull
the lowest possible system vacuum while
recovering and condensing refrigerant.
Equipment capable of pulling a vacuum of
less than 1,000 microns of mercury is
recommended.
Do not open the unit to the atmosphere
for service work until refrigerant is fully
removed/recovered. When leak-testing
with trace refrigerant and nitrogen, use
HCFC-22 (R-22) rather than CFC-12 (R-
12) or any other fully-halogenated
refrigerant . Be aware of any new leak
test methods which may eliminate
refrigerants as a trace gas. Perform
evacuation prior to charging with a
vacuum pump capable of pulling a
vacuum of 1,000 microns of mercury or
less. Let the unit stand for 12 hours and
with the vacuum not rising above 2,500
microns of mercury.
A rise above 2,500 microns of mercury
indicates a leak test is required to locate
and repair any leaks. A leak test is
required on any repaired area.
Charge refrigerant into the equipment
only after equipment does not leak or
contain moisture. Reference proper
refrigerant charge requirements in the
maintenance section of this manual to
ensure efficient machine operation. When
charging is complete, purge or drain
charging lines into an approved refriger-
ant container. Seal all used refrigerant
containers with approved closure devices
to prevent unused refrigerant from
escaping to the atmosphere. Take extra
care to properly maintain all service
equipment directly supporting refrigerant
service work such as gauges, hoses,
vacuum pumps, and recycling equipment
.
When cleaning system components or
parts, avoid using CFC-11 (R-11) or CFC-
113 (R-113). Use only cleaning-solvents
that do not have ozone depletion factors.
Properly dispose of used materials.
Refrigeration system cleanup methods
using filters and driers are preferred.
Check for leaks when excessive purge
operation is observed.
Keep abreast of unit enhancements,
conversion refrigerants, compatible
parts, and manufacturer’s recommenda-
tions that will reduce refrigerant emis-
sions and increase equipment operating
efficiencies.
Содержание LPC
Страница 50: ...50 LPC SVX01C EN Operation general information Figure O GI 9 Tracer AH540 termination board ...
Страница 89: ...LPC SVX01C EN 89 Operation sequence of operation Table O SO 19 Comm LED yellow Table O SO 20 Required inputs ...
Страница 91: ...LPC SVX01C EN 91 Maintenance diagnostics Table M D 2 Tracer AH540 541 diagnostics ...
Страница 92: ...92 LPC SVX01C EN Maintenance diagnostics Table M D 2 continued Tracer AH540 541 diagnostics ...
Страница 94: ...94 LPC SVX01C EN Maintenance troubleshooting Table M T 2 Valves stay open ...
Страница 95: ...LPC SVX01C EN 95 Maintenance troubleshooting Table M T 3 Valves stay closed ...
Страница 96: ...96 LPC SVX01C EN Maintenance troubleshooting Table M T 4 Outdoor air damper stays open ...
Страница 97: ...LPC SVX01C EN 97 Maintenance troubleshooting Table M T 5 Outdoor air damper stays closed ...
Страница 98: ...98 LPC SVX01C EN Maintenance troubleshooting Table M T 6 DX cooling binary outputs do not energize ...
Страница 99: ...LPC SVX01C EN 99 Maintenance troubleshooting Table M T 7 Electric heat binary outputs do not energize ...
Страница 104: ...104 LPC SVX01C EN Maintenance appendix Figure M A 1 Flowchart EnteringWaterTemperature Sampling Function ...
Страница 107: ...LPC SVX01C EN 107 Maintenance appendix Table M A 6 Hard wired CO2 sensor values ...
Страница 109: ......