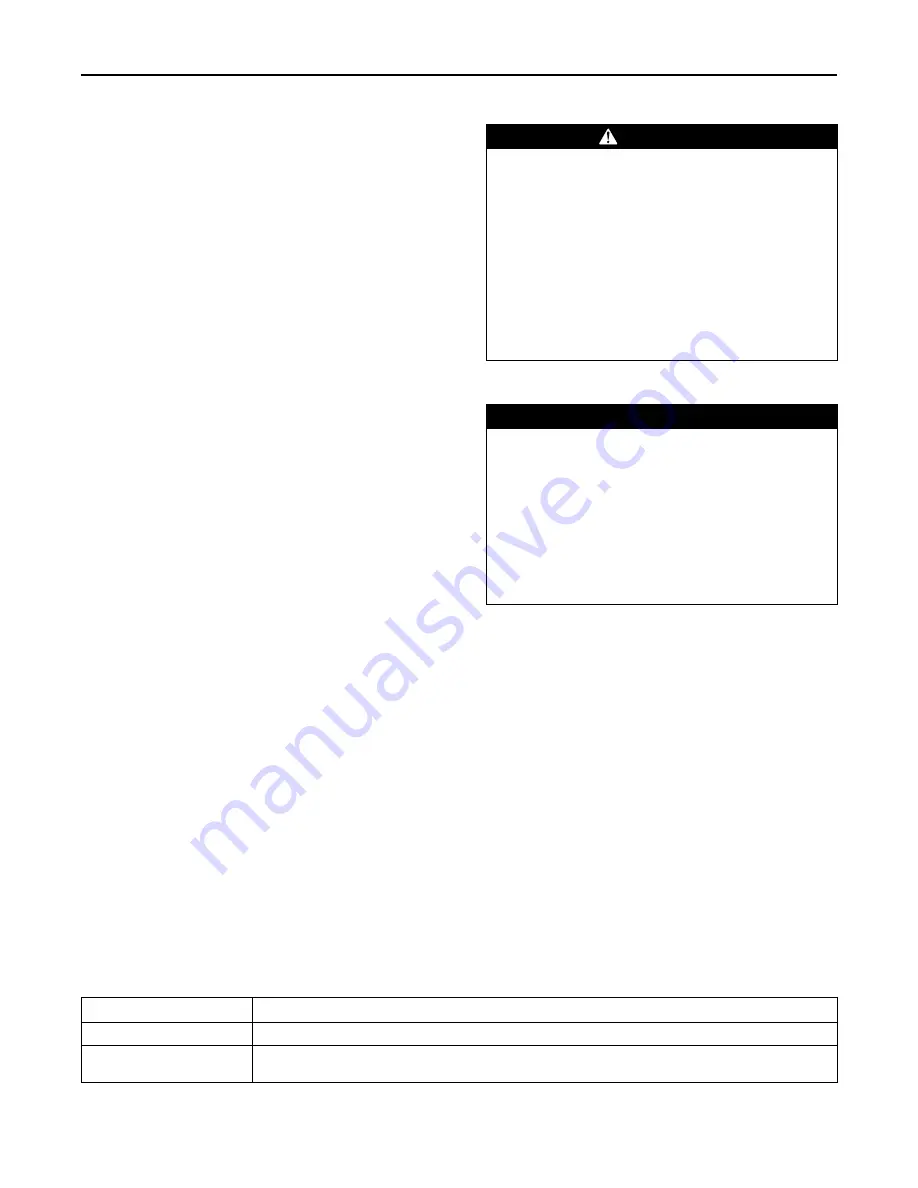
RT-SVX51L-EN
41
–
ambient temperature
–
compressor oil level (each circuit)
–
compressor suction and discharge pressures (each
circuit)
–
superheat and subcooling (each circuit)
Record this data on an “operator’s maintenance log” like
the one shown in Sample maintenance log table in Final
Process Section. If the operating pressures indicate a
refrigerant shortage, measure the system superheat and
system subcooling. For guidelines, refer to
“Compressor
Start-Up,” p.
.
Important:
Do not release refrigerant to the atmosphere! If
adding or removing refrigerant is required, the
service technician must comply with all
federal, state and local laws. Refer to general
service bulletin MSCU-SB-1 (latest edition).
Heating Season
☐
Inspect the unit’s air filters. If necessary, clean or
replace them.
☐
Check supply fan motor bearings; repair or replace the
motor as necessary.
☐
Inspect both the main unit control panel and heat
section control box for loose electrical components and
terminal connections, as well as damaged wire
insulation. Make any necessary repairs.
☐
Verify that the electric heat system operates properly.
Coil Cleaning
Regular coil maintenance, including annual cleaning
enhances the unit’s operating efficiency by minimizing the
following:
•
Compressor head pressure and amperage draw
•
Evaporator water carryover
•
Fan brake horsepower
•
Static pressure losses
•
Airflow reduction
At least once each year, or more often if the unit is located
in a “dirty” environment, clean the condenser coils using
the instructions outlined below. Be sure to follow these
instructions as closely as possible to avoid damaging the
coils.
WARNING
Hazardous Chemicals!
Failure to follow this safety precaution could result in
death or serious injury. Coil cleaning agents can be
either acidic or highly alkaline and can burn severely
if contact with skin or eyes occurs.
Handle chemical carefully and avoid contact with
skin. ALWAYS wear Personal Protective Equipment
(PPE) including goggles or face shield, chemical
resistant gloves, boots, apron or suit as required. For
personal safety refer to the cleaning agent
manufacturer’s Materials Safety Data Sheet and follow
all recommended safe handling practices.
Microchannel (MCHE) Coils
NOTICE
Coil Damage!
Failure to follow instructions below could result in
coil damage.
DO NOT use any detergents with microchannel
condenser coils.
Use pressurized water or air ONLY, with pressure no
greater than 600psi.
For additional information regarding the proper
microchannel coil cleaning procedure, refer to RT-
SVB83*-EN
Due to the soft material and thin walls of the MCHE coils,
the traditional field maintenance method recommended for
Round Tube Plate Fin (RTPF) coils does not apply to
microchannel coils. Moreover, chemical cleaners are a risk
factor to MCHE due to the material of the coil. The
manufacturer does not recommend the use of chemical
cleaners to clean microchannel coils. Using chemical
cleaners could lead to warranty claims being further
evaluated for validity and failure analysis.
The recommended cleaning method for microchannel
condenser coils is pressurized water or air with a non-
pinpoint nozzle and an ECU of at least 180 with pressure
no greater than 600 psi. To minimize the risk of coil
damage, approach the cleaning of the coil with the
pressure washer aimed perpendicular to the face of the coil
during cleaning. Optimum clearance between the sprayer
nozzle and the microchannel coil is 1”–3”.
Final Process
For future reference, record the unit data below in the
blanks provided.
Table 18.
Unit data log
Complete Unit Model Number
Unit Serial Number
Wiring Diagram Numbers (from
unit control panel)
Содержание Foundation GCC180-300
Страница 30: ...30 RT SVX51L EN Figure 31 Through the base gas piping installation Installation...
Страница 42: ...42 RT SVX51L EN Table 18 Unit data log continued schematic s connections Network ID Maintenance...
Страница 49: ...RT SVX51L EN 49 Notes...
Страница 50: ...50 RT SVX51L EN Notes...
Страница 51: ...RT SVX51L EN 51 Notes...