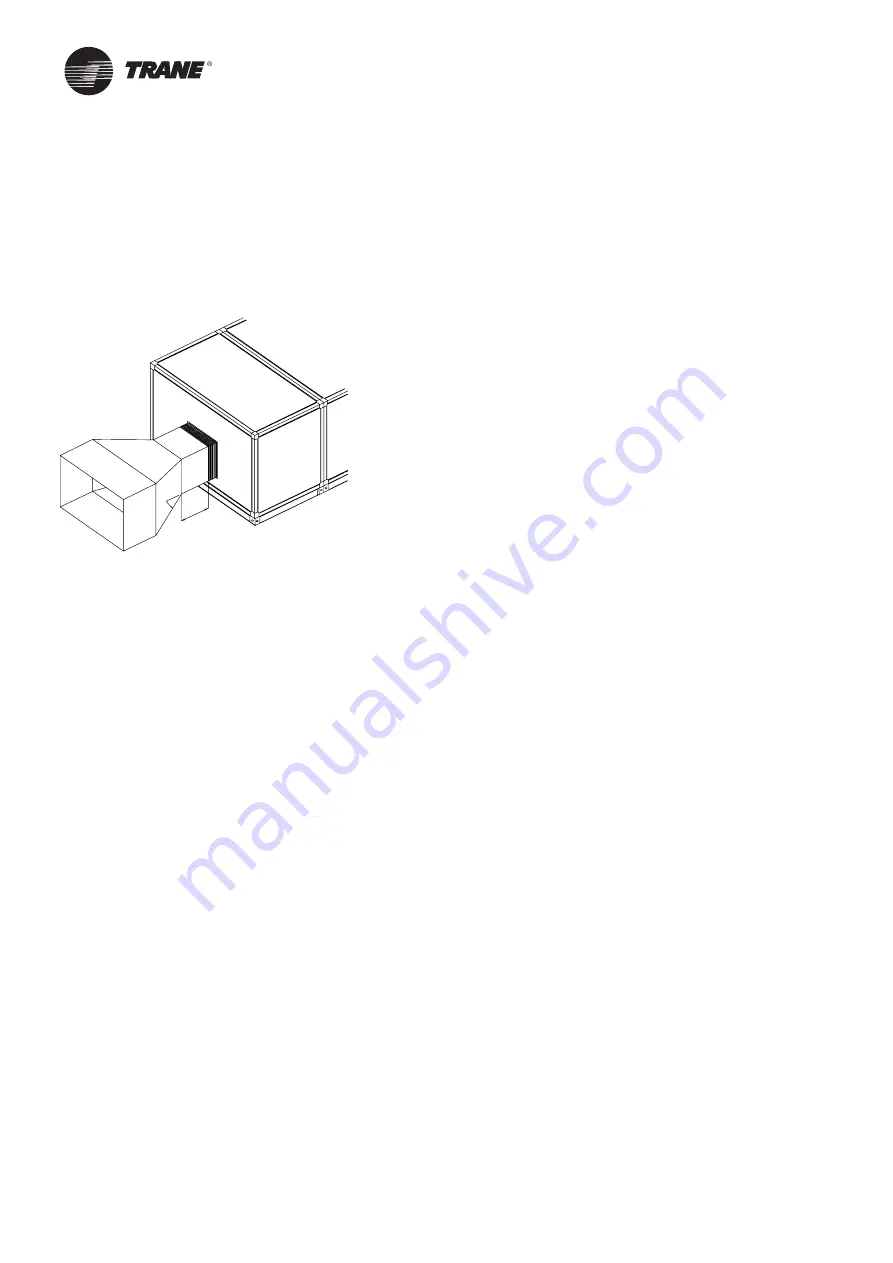
14
4
UNT-PRC002-GB
Technical Data
FWD
08
12
20
30
45
Power supply
(V/Ph/Hz)
230/1/50
Capacities
Cooling capacity on water (1)
(kW)
5,2
8,3
15
18,8
30,1
Heating capacity on water (2)
(kW)
6,3
11,9
18,9
20,9
38,2
Fan motor
(type)
2 x direct drive centrifugal
Fan power input (3)
(kW)
0,23
0,46
0,65
1,04
1,51
Current amps (3)
(A)
1,1
2,2
3,1
4,7
5,5
Start-up amps
(A)
3,2
5,5
9,3
14,1
16,5
Air flow
minimum
(m
3
/h)
490
980
1400
1800
2700
nominal
(m
3
/h)
820
1650
2300
3000
4500
maximum
(m
3
/h)
980
1970
2600
3600
5400
Main coil
Water entering/leaving connections
(type)
ISO R7 rotating female
(Dia)
3/4"
3/4"
1 1/2"
1 1/2"
1 1/2"
Electric heater (accessory for blower only)
Electric power supply
(V/Ph/Hz)
230/1/50
230/1/50 or 400/3/50
400/3/50
400/3/50
400/3/50
Heating capacity
(kW)
2/4
8
10
12
12
Hot water coil (accessory for blower only)
Heating capacity (4)
(kW)
6,3
12
17,4
22,4
34,5
G2 filter (filter box accessory)
Quantity
2
2
2
2
2
Dimensions ( LxWxth)
(mm)
386x221x8
486x271x8
586x321x8
586*421*8
586*621*8
G4 filter (filter box accessory)
Quantity
-
2
2
2
2
Dimensions ( LxWxth)
(mm)
-
486x264x48
586x314x48
586*414*48
586*614*48
Condensate pump (accessory)
(type)
Centrifugal
Water flow - lift height
(l/h - mm)
24 - 500
Not available for FWD30 and FWD45
Sound level (L/M/H speed)
Sound pressure level (5)
(dB(A))
36/40/43
38/41/44
46/50/53
47/52/57
47/52/58
Sound power level (5)
(dB(A))
46/50/53
48/51/54
56/60/63
57/62/67
57/62/68
Unit dimensions
Width x Depth
(mm)
890 x 600
1090 x 710
1290 x 820
1290 x 970
1290 x 1090
Height
(mm)
250
300
350
450
650
Shipped unit dimensions
Width x Depth
(mm)
933 x 644
1133 x 754
1333 x 864
1333 x 1008
1333*1133
Height
(mm)
260
310
360
460
660
Weight
(kg)
32
46
61
76
118
Colour
galvanised steel
Recommended fuse size
Unit alone (aM/gI)
(A)
8/16
8/16
8/16
8/25
8/25
Unit with electric heater (gI)
(A)
16 (2kW),25 (4kW)
40 (230V),3*16 (400V)
3*20
3*25
3*25
(1) Conditions: Water entering/leaving temperature: 7/12 °C, Air inlet temperature 27/19°C DB/WB - Nominal air flow
(2) Conditions: Water entering/leaving temperature: 50/45 °C, Air inlet temperature 20°C DB - Nominal air flow
(3) At high speed with nominal air flow.
(4) Water entering/leaving temperature 90/70 °C, air inlet temperature 20 °C DB, Nominal air flow.
(5) A rectangular glass wool duct 1m50 long is placed on the blower.The measurement is taken in the room containing the blower unit.
Heat exchanger operating limits:
FWD:
*water temperature: max 100° C
*absolute service pressure: min 1 bar/max 11 bars
Accessories - Hot water coil:
*water temperature: min. +2° C/max. 100° C
*absolute service pressure: min 1 bar/max 11 bars
AH-SVX03C-GB
Duct connection
The air handling connections must be made symmetrically and stress free.
To avoid noise transmission, the fitting of an intermediate flexible connection of at least 140 mm depth, between duct
work and the unit is recommended. This should be unstressed when initially positioned. To ensure the best possible
performance of the units whilst avoiding excessive pressure loss in the duct system and minimizing air stream noise,
compliance with good practice in duct assembly and acoustic layout, is essential.
Figure 9 –
Duct connection
L
alfa
Generally, the length 'L' of the first duct section should be greater than 1½ times the size of the fan diameter.
The angle 'a' of the transition duct should be less than 30° and shall be avoided section reduction just after the
connection of duct to the unit (see Figure 9).
Note: If the air inlet and/or outlet on the ducts are very close to the air handling unit and if there are no bends along
this section, the fitting of a sound attenuator is recommended.
CAUTION!
Ducts must never be disconnected during fan operation. The fan must never be run when ducts are
disconnected. The absence of pressure drops would increase current absorption causing the motor windings to burn.
CAUTION!
Ducts must be self supporting and must not load the air handling unit or its components (damper,
flanges, etc) with their weight.
Trane cannot be held responsible of any damages on casing, dampers, structure due to direct connection of duct to
the unit without placing a flexible connection between duct and unit.
Damper movement is factory-tested. At unit reception, carefully check that dampers move freely. If they do not move
freely, they have been damaged during handling or duct connection.
CAUTION!
Never drill into the machine casing on-site. Risk of electrical shock.
Electrical connection
The unit is designed to run with 400 V +/- 5%/50 Hz/ 3 ph.
Over current protection
The branch circuit feeding the unit must be protected in accordance with national or local codes and maximum unit
amps indicated unit documentation provided.
Power wiring
The unit's power supply must be provided by 5-wire cable with crosssectional areas complying with legislation.
Note:
1. Earthing must be executed in compliance to national and local legislation.
2. The machines are designed for a short-circuit current of 10 kA. In the event of a higher application, contact your
local Trane sales office.
The electrical work must be carried out in accordance with all international, national, and local regulations. Electrical
connections passing from the casing to the fan motor should be carried out in a flexible conduit. Cables passing
through the casing must be made with a gland or grommet. Glands can be already installed in the unit as option.
All wiring to other accessories must be carried out in the same manner. If you have any queries, please contact your
local Trane sales office.
Installation