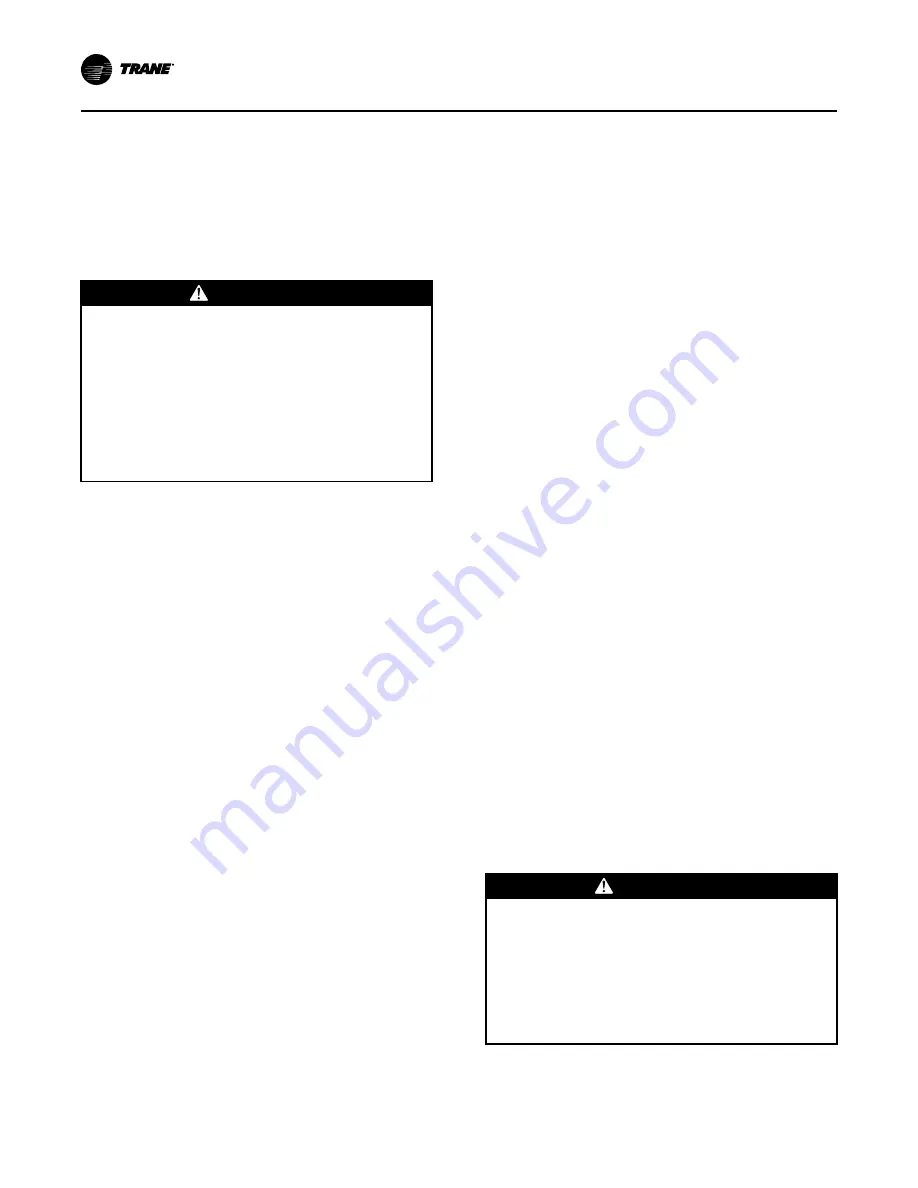
52
ARTC-SVX001B-EN
2. Inspect fuses to ensure they are secure, of correct
amperage ratng, undamaged and functioning.
3. Energize each compressor and check refrigerant
pressures, signs of overheating, and oil leaks.
Check for noises and for leaks with an electronic or
bubble leak detector. Inspect flared fittings,
refrigeration gauges, compressor connections,
braze joints, pressure switches, and access ports on
Schrader valves.
W
WA
AR
RN
NIIN
NG
G
R
Re
effrriig
ge
erra
an
ntt u
un
nd
de
err H
Hiig
gh
h P
Prre
essssu
urre
e!!
F
Fa
aiillu
urre
e tto
o ffo
ollllo
ow
w iin
nssttrru
uccttiio
on
nss b
be
ello
ow
w cco
ou
ulld
d rre
essu
ulltt iin
n
a
an
n e
ex
xp
pllo
ossiio
on
n w
wh
hiicch
h cco
ou
ulld
d rre
essu
ulltt iin
n d
de
ea
atth
h o
orr
sse
erriio
ou
uss iin
njju
urry
y o
orr e
eq
qu
uiip
pm
me
en
ntt d
da
am
ma
ag
ge
e..
S
Sy
ysstte
em
m cco
on
ntta
aiin
nss rre
effrriig
ge
erra
an
ntt u
un
nd
de
err h
hiig
gh
h p
prre
essssu
urre
e..
R
Re
ecco
ov
ve
err rre
effrriig
ge
erra
an
ntt tto
o rre
elliie
ev
ve
e p
prre
essssu
urre
e b
be
effo
orre
e
o
op
pe
en
niin
ng
g tth
he
e ssy
ysstte
em
m.. S
Se
ee
e u
un
niitt n
na
am
me
ep
plla
atte
e ffo
orr
rre
effrriig
ge
erra
an
ntt tty
yp
pe
e.. D
Do
o n
no
ott u
usse
e n
no
on
n--a
ap
pp
prro
ov
ve
ed
d
rre
effrriig
ge
erra
an
nttss,, rre
effrriig
ge
erra
an
ntt ssu
ub
bssttiittu
utte
ess,, o
orr rre
effrriig
ge
erra
an
ntt
a
ad
dd
diittiiv
ve
ess..
4. De-energize each compressor and inspect terminals
for pitting, corrosion, and loose connections.
5. Inspect that the oil level is visible in each
compressor and not discolored. Annual oil samples
should be taken to be analyzed for destructive
acids, corrosive materials, or metal deposits.
6. Inspect and record the compressor amperage
draws and voltage.
7. Record water/glycol mixture flow to ensure it meets
design specifications.
8. Tighten rotalock nuts at the compressors. The
recommended torque is 80 lbf for 2 inch and larger
and 60 lbf for rotalock nuts smaller than 2 inch.
9. Inspect all copper lines and control capillary tubing
to ensure that the lines are separated and not
vibrating against one another or the frame or
housing.
10. Ensure all refrigeration lines are properly supported
to prevent vibration from causing premature failure
of copper piping.
11. Inspect all insulation on piping and control sensors.
Repair and replace as necessary.
12. Inspect entire plumbing system for leaks.
13. Review logged alarms and look for repetitive
trends. The chiller can retain the previous 200
alarms with time and date of occurrence.
14. If equipped, inspect crankcase heaters to verify
proper operation.
15. Sample refrigerant to analyze for moisture or acid.
16. Inspect operating pressures and temperatures and
ensure the chiller has a full refrigerant charge.
Pump and Tank Maintenance Tasks
For chillers equipped with a tank and pump module,
additional maintenance steps are required at least
every six months:
1. Ensure that the pump, motor, and the immediate
area are clear of dirt, debris, leaves, animal nests,
and so forth.
2. Ensure pump mountings are secure and fasteners
are tight to prevent pipe movement and eventual
failure.
3. Inspect pump for proper rotation.
4. Check pump for leaks and excessive noise while in
operation.
5. Lubricate pumps as recommended by the
manufacturer. Refer to the pump manufacturer’s
operating and maintenance manual for lubricating
instructions, if any are required.
6. Test and record the motor amp draw under full
load.
7. Test the pump overload protection device. Adjust if
necessary.
Maintenance Tasks
The maintenance tasks described herein present the
basic, minimal, steps required to successfully complete
a task. Local policies and protocols may require more
elaborate procedures with additional checks and
inspections.
Inspection Methods
Appropriate inspection for modern chillers can be
described as “hands on.” Where possible and
appropriate, visual inspection should include touching
the component or apparatus being inspection. The
sense of touch provides additional feedback regarding
temperature, texture, tightness, and dryness that “eyes
only” inspection cannot match. Habitually touching
each item to be inspected also ensures that items are
not subconsciously skipped during the inspection
process. For a summary of tasks, see , Recommended
Chiller Service Intervals.
W
WA
AR
RN
NIIN
NG
G
H
Ha
azza
arrd
do
ou
uss V
Vo
olltta
ag
ge
e!!
F
Fa
aiillu
urre
e tto
o d
diisscco
on
nn
ne
ecctt p
po
ow
we
err b
be
effo
orre
e sse
errv
viicciin
ng
g cco
ou
ulld
d
rre
essu
ulltt iin
n d
de
ea
atth
h o
orr sse
erriio
ou
uss iin
njju
urry
y..
D
Diisscco
on
nn
ne
ecctt a
allll e
elle
eccttrriicc p
po
ow
we
err,, iin
nccllu
ud
diin
ng
g rre
em
mo
otte
e
d
diisscco
on
nn
ne
eccttss b
be
effo
orre
e sse
errv
viicciin
ng
g.. F
Fo
ollllo
ow
w p
prro
op
pe
err
llo
occkko
ou
utt//tta
ag
go
ou
utt p
prro
occe
ed
du
urre
ess tto
o e
en
nssu
urre
e tth
he
e p
po
ow
we
err
cca
an
n n
no
ott b
be
e iin
na
ad
dv
ve
errtte
en
nttlly
y e
en
ne
errg
giizze
ed
d.. V
Ve
erriiffy
y tth
ha
att n
no
o
p
po
ow
we
err iiss p
prre
esse
en
ntt w
wiitth
h a
a v
vo
ollttm
me
ette
err..