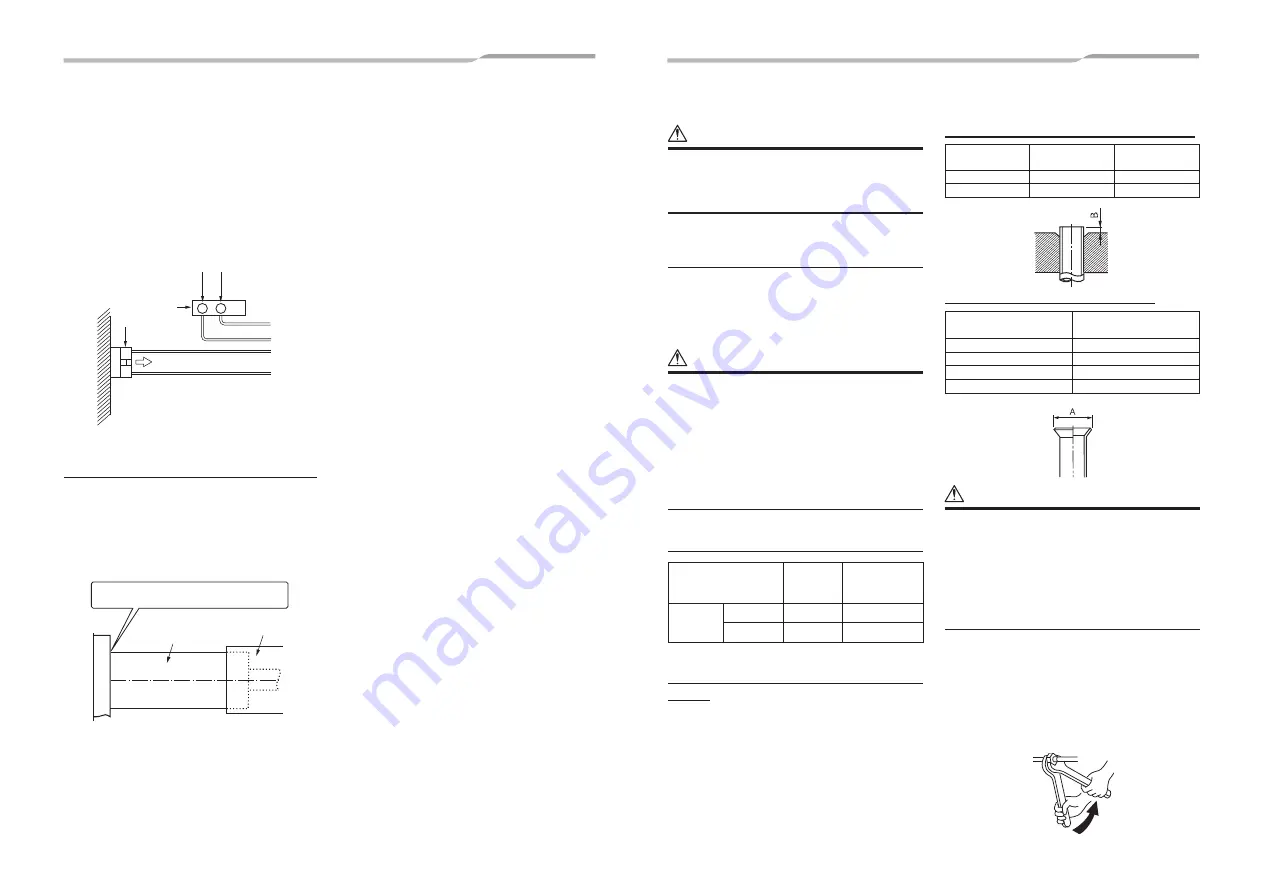
24-EN
23-EN
– 12 –
EN
6
Refrigerant piping
CAUTION
When the refrigerant pipe is long, provide support
brackets at intervals of 2.5 m to 3 m to clamp the
refrigerant pipe. Otherwise, abnormal sound may be
generated.
Permissible piping length and
height difference
They vary depending on the outdoor unit. For details,
refer to the Installation Manual attached to the outdoor
unit.locally procured so that it overlaps with the
attached heat insulator of the drain connecting section.
CAUTION
IMPORTANT 4 POINTS FOR PIPING WORK
1. Reusable mechanical connectors and
fl
ared joints are
not allowed indoors. When mechanical connectors are
reused indoors, sealing parts shall be renewed. When
fl
ared joints are reused indoors, the
fl
are part shall be
refabricated.
2. Tight connection (between pipes and unit)
3. Evacuate the air in the connecting pipes by using
VACUUM PUMP.
4. Check the gas leakage. (Connected points)
Pipe size
Model name
HM56 Type
HM80, HM90,
HM110, HM140,
HM160 Type
Pipe size
Gas side
12.7 mm
15.9 mm
Liquid side
6.4 mm
9.5 mm
Connecting refrigerant piping
Flaring
•
Cut the pipe with a pipe cutter.
Remove burrs completely.
Remaining burrs may cause gas leakage.
•
Insert a
fl
are nut into the pipe, and
fl
are the pipe.
As the
fl
aring sizes of R32 differ from those of
refrigerant R22, the
fl
are tools newly manufactured
for R32 are recommended. However, the
conventional tools can be used by adjusting
projection margin of the copper pipe.
•
Test water drain while checking the operation sound
of the drain pump motor.
(If the operation sound changes from continuous
sound to intermittent sound, water is normally
drained.)
After the check, the drain pump motor runs,
connecting the
fl
oat switch connector.
(In case of check by pulling out the
fl
oat switch
connector, be sure to return the connector to the
original position.)
1
2
Power
terminals
CN34
(RED)
Black
Red
White
Black
Pull out connector CN34 (Red)
from P.C. board.
Single phase
220-240V
Perform heat insulating
•
As shown in the
fi
gure, cover the
fl
exible hose and
hose band with the attached heat insulator up to the
bottom of the indoor unit without gap.
•
Cover the drain pipe seamlessly with a heat insulator
locally procured so that it overlaps with the attached
heat insulator of the drain connecting section.
Wrap the attached heat insulator seamlessly from
the surface of the indoor unit.
Heat insulator of the
drain connecting
section (Accessory)
Indoor unit
Heat insulator
(Locally procured)
* Direct the slits and seams of the heat insulator
upward to avoid water leakage.
Projection margin in
fl
aring: B (Unit: mm)
Outer dia. of
copper pipe
Tool used
Conventional
tool used
6.4, 9.5
0.5 to 1.1
1.0 to 1.5
12.7, 15.9
0.5 to 1.1
1.5 to 2.0
Flaring diameter size: A (Unit: mm)
Outer dia. of copper pipe
A
+
0
– 0.4
6.4
9.1
9.5
13.2
12.7
16.6
15.9
19.7
CAUTION
•
Do not scratch the inner surface of the
fl
ared part
when removing burrs.
•
Flare processing under the condition of scratches on
the inner surface of
fl
are processing part will cause
refrigerant gas leak.
•
Check that the
fl
ared part is not scratche, deformed,
stepped, or other problems, after
fl
are processing.
•
Do not apply refrigerating machine oil to the
fl
are
surface.
*
In case of
fl
aring with the conventional
fl
are tool, pull
it out approx. 0.5 mm more than that for R22 to adjust
to the speci
fi
ed
fl
are size. The copper pipe gauge is
useful for adjusting projection margin size.
•
The sealed gas was sealed at the atmospheric
pressure so when the
fl
are nut is removed, there
will no “whooshing” sound: This is normal and is not
indicative of trouble.
•
Use two wrenches to connect the indoor unit pipe.
Work using double spanner