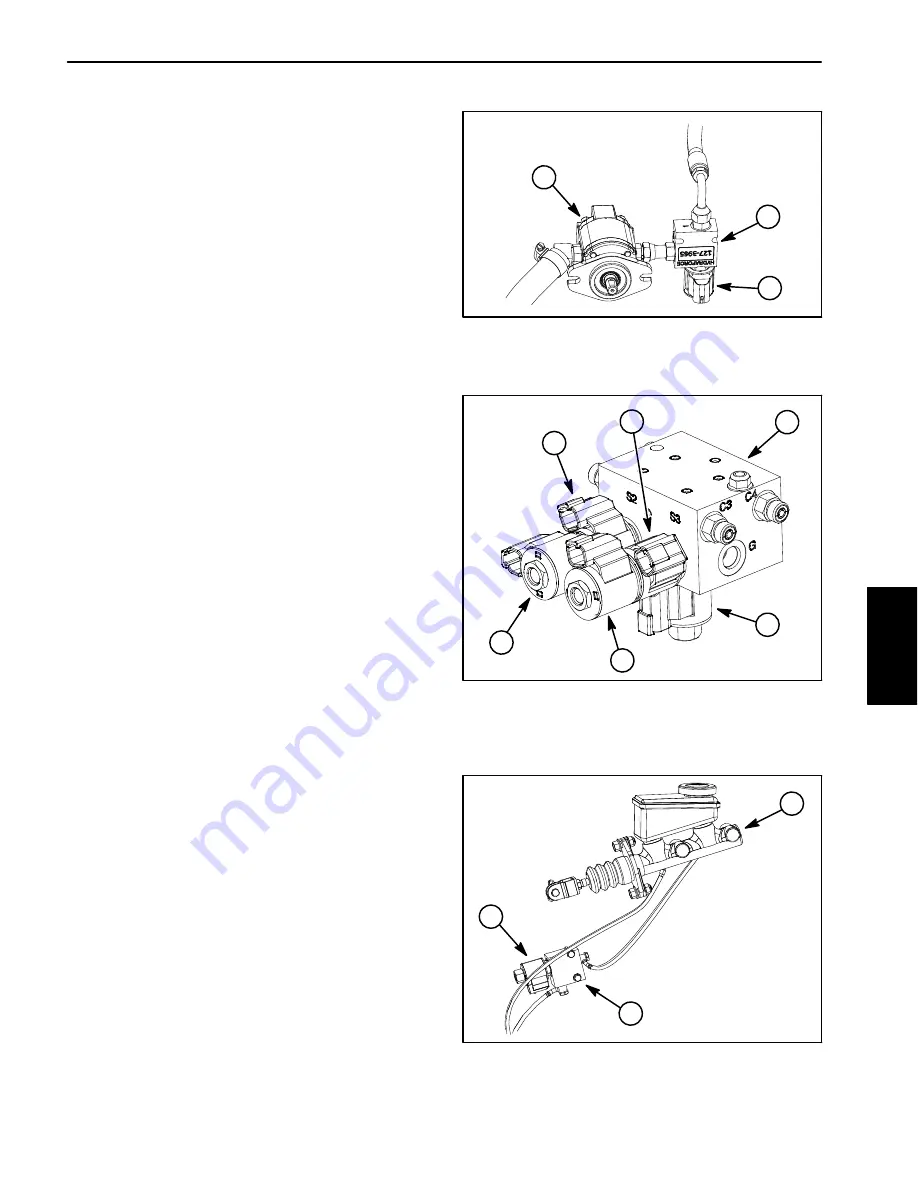
Multi Pro 1750
Page 5 − 58
Electrical System
Hydraulic Solenoid Valve Coils
The Multi Pro 1750 hydraulic system uses several hy-
draulic solenoid valve coils for system control. The hy-
draulics enable valve assembly includes one (1)
solenoid valve (Fig. 77). The boom lift control manifold
includes five (5) solenoid valves (Fig. 78). The brake
hold valve in the brake system also includes a solenoid
valve (Fig. 79). When the solenoid coils are energized,
hydraulic valve shift occurs to control hydraulic flow.
Testing of the coils can be done with the coil installed on
the hydraulic valve.
Testing
1. Park machine on a level surface, stop spray pump,
stop engine and engage parking brake.
2. Locate solenoid valve coil to be tested and discon-
nect wire harness connector from coil.
NOTE: Prior to taking small resistance readings with a
digital multimeter, short the meter test leads together.
The meter will display a small resistance value (usually
0.5 ohms or less). This resistance is due to the internal
resistance of the meter and test leads. Subtract this val-
ue from from the measured value of the solenoid you are
testing.
NOTE: Solenoid coil resistance should be measured
with solenoid at approximately 68F (20C). Resistance
may be slightly different than listed at different tempera-
tures. Typically, a failed solenoid coil will either be
shorted (very low or no resistance) or open (infinite re-
sistance).
3. Using a multimeter (ohms setting), measure resis-
tance between the two (2) connector terminals on the
solenoid valve coil. The resistance for all solenoid coils
used on Multi Pro 1750 machines should be 8.8 ohms.
4. If solenoid coil resistance is incorrect, replace coil
(see Hydraulics Enable Valve Assembly in Chapter 4 −
Hydraulic System, Boom Lift Control Manifold Service in
Chapter 4 − Hydraulic System, or Brake Hold Valve in
Chapter 8 − Chassis in this manual).
NOTE: Because the five (5) solenoid valve coils on the
boom lift control manifold are identical, they can be ex-
changed to assist in troubleshooting. If the problem fol-
lows the exchanged coil, an electrical problem likely
exists with the coil. If the problem remains unchanged,
something other than the solenoid coil is the problem
source (e.g. switch, circuit wiring, hydraulic problem).
5. After testing is completed, connect wire harness
electrical connector to the solenoid valve coil.
Figure 77
1. Gear
pump
2. Hydraulics enable valve
3. Solenoid valve coil
3
2
1
1. Boom lift manifold
2. Coil (S1) (enable)
3. Coil (S2) (RH raise)
4. Coil (S2) (RH lower)
5. Coil (S3) (LH raise)
6. Coil (S3) (LH lower)
Figure 78
5
3
4
2
6
1
1. Brake master cylinder
2. Brake hold valve
3. Brake hold coil
Figure 79
3
2
1
Electrical
System
Содержание 41188
Страница 1: ...Form No 15215SL Rev A Multi Pro 1750 Original Instructions EN...
Страница 4: ...NOTES _...
Страница 6: ...Multi Pro 1750 This page is intentionally blank...
Страница 8: ...Multi Pro 1750 This page is intentionally blank...
Страница 14: ...0 09375 Multi Pro 1750 Page 2 2 Product Records and Maintenance Equivalents and Conversions...
Страница 29: ...Multi Pro 1750 Page 3 11 Kohler Gasoline Engine This page is intentionally blank Kohler Gasoline Engine...
Страница 33: ...Multi Pro 1750 Page 3 15 Kohler Gasoline Engine This page is intentionally blank Kohler Gasoline Engine...
Страница 43: ...Multi Pro 1750 Page 3 25 Kohler Gasoline Engine This page is intentionally blank Kohler Gasoline Engine...
Страница 48: ...Multi Pro 1750 Page 3 30 Kohler Gasoline Engine This page is intentionally blank...
Страница 51: ...Multi Pro 1750 Hydraulic System Page 4 3 This page is intentionally blank Hydraulic System...
Страница 71: ...Multi Pro 1750 Hydraulic System Page 4 23 This page is intentionally blank Hydraulic System...
Страница 81: ...Multi Pro 1750 Hydraulic System Page 4 33 This page is intentionally blank Hydraulic System...
Страница 85: ...Multi Pro 1750 Hydraulic System Page 4 37 This page is intentionally blank Hydraulic System...
Страница 91: ...Multi Pro 1750 Hydraulic System Page 4 43 This page is intentionally blank Hydraulic System...
Страница 97: ...Multi Pro 1750 Hydraulic System Page 4 49 This page is intentionally blank Hydraulic System...
Страница 102: ...Multi Pro 1750 Hydraulic System Page 4 54 This page is intentionally blank...
Страница 121: ...Multi Pro 1750 Page 5 19 Electrical System This page is intentionally blank Electrical System...
Страница 127: ...Multi Pro 1750 Page 5 25 Electrical System This page is intentionally blank Electrical System...
Страница 183: ...Multi Pro 1750 Page 6 9 Spray System This page is intentionally blank Spray System...
Страница 191: ...Multi Pro 1750 Page 6 17 Spray System This page is intentionally blank Spray System...
Страница 195: ...Multi Pro 1750 Page 6 21 Spray System This page is intentionally blank Spray System...
Страница 201: ...Multi Pro 1750 Page 6 27 Spray System This page is intentionally blank Spray System...
Страница 219: ...Multi Pro 1750 Page 6 45 Spray System This page is intentionally blank Spray System...
Страница 226: ...Multi Pro 1750 Page 6 52 Spray System This page is intentionally blank...
Страница 233: ...Multi Pro 1750 Page 7 7 Drive Train This page is intentionally blank Drive Train...
Страница 237: ...Multi Pro 1750 Page 7 11 Drive Train This page is intentionally blank Drive Train...
Страница 278: ...Multi Pro 1750 Page 7 52 Drive Train This page is intentionally blank...
Страница 307: ...Multi Pro 1750 Chassis Page 8 29 This page is intentionally blank Chassis...
Страница 335: ...Multi Pro 1750 Page 9 25 Ultra Sonic Boom Kit Optional This page is intentionally blank Ultra Sonic Boom Opt...
Страница 340: ...Multi Pro 1750 Page 9 30 Ultra Sonic Boom Kit Optional This page is intentionally blank...
Страница 348: ...Page 10 8 Multi Pro 1750 Main Wire Harness Drawing machine serial number below 315000000 121 6568 E...
Страница 349: ...Page 10 9 Multi Pro 1750 Main Wire Harness Diagram machine serial number below 315000000 121 6568 E...
Страница 350: ...Page 10 10 Multi Pro 1750 Main Wire Harness Drawing machine serial number above 315000000 122 0431 C...
Страница 351: ...Page 10 11 122 0431 C Multi Pro 1750 Main Wire Harness Diagram machine serial number above 315000000...
Страница 352: ...Page 10 12 Ultra Sonic Boom Kit Optional Wire Harness Drawing...