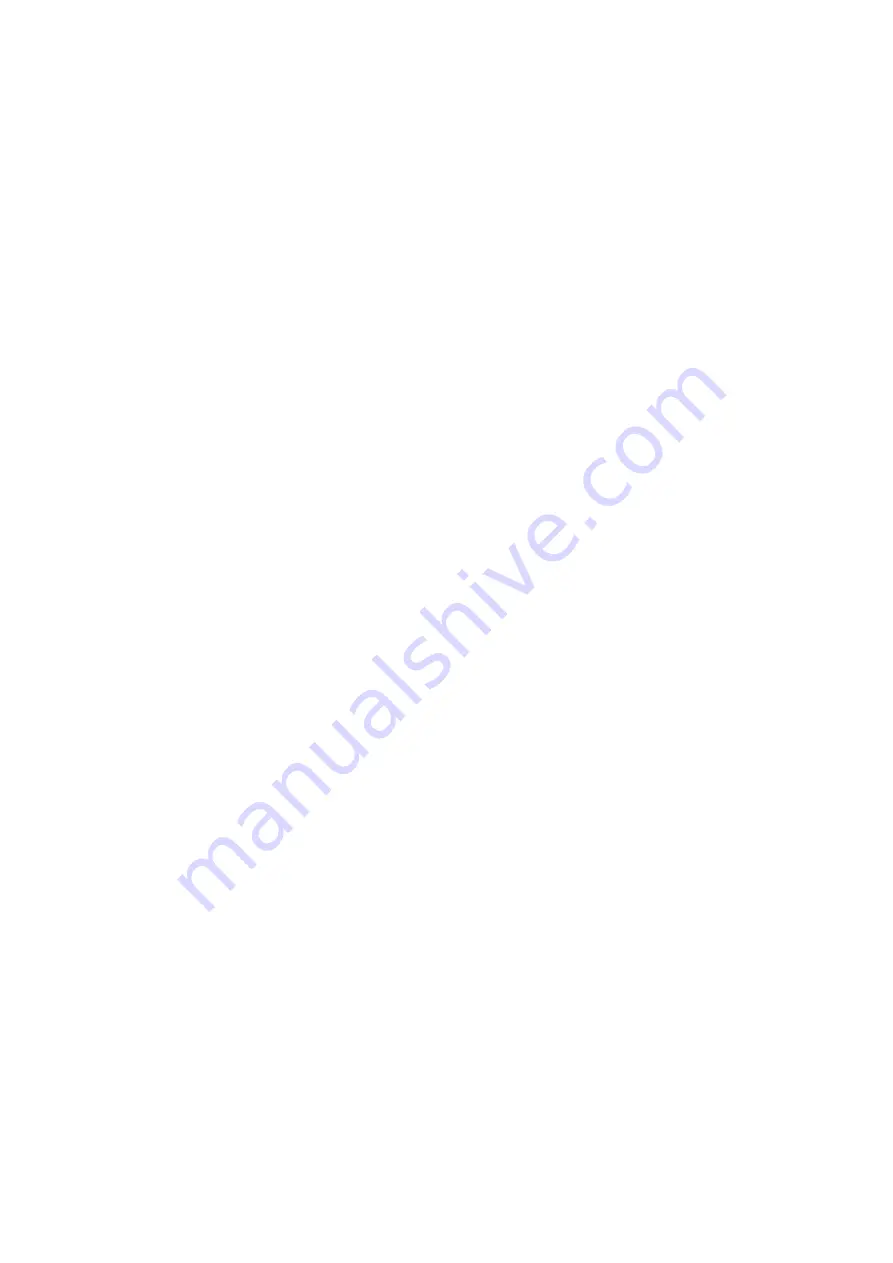
TM 9-1829A, April 1944
14/100
2021-07-07
b)
Field plate eccentric with speed cup:
Loosen field plate and move toward high-registering part of
dial, then tighten screws.
c)
Speed cup not in static balance:
Replace or balance speed cup.
(5)
Excessive Noise:
Too much end play in magnet shaft, or worn gears, may cause noise in instrument. To
correct, flare magnet shaft or replace gears as required.
(6)
Inoperative odometer.
a)
First gear (on magnet shaft) stripped: Replace magnet and shaft.
b)
Excessive end play in second gear: Adjust to proper end play.
c)
Second and third gears stripped or worn: Replace gears.
d)
Odometer bound up: Replace complete odometer assembly. Do not attempt to repair unless so
specified in this manual.
e)
Odometer intermediate gear turning on shaft (Stewart-Warner only): Restake gear on shaft.
(7)
Odometer operates but does not record correctly.
a)
Wrong second and third gears: Replace with correct gears (gears used in speedometers reading in
kilometers are approximately
1
/
3
faster than gears used in speedometers reading in miles.)
Note:
When odometers do not accurately record the distance traveled, it may be caused by the wrong
speedometer drive and driven gears in the transmission of the vehicle, or by a change in the tire size
on the vehicle. Such errors can be corrected by installing the proper ratio drive joint (or adapter)
at the flexible shaft connection on the transmission.