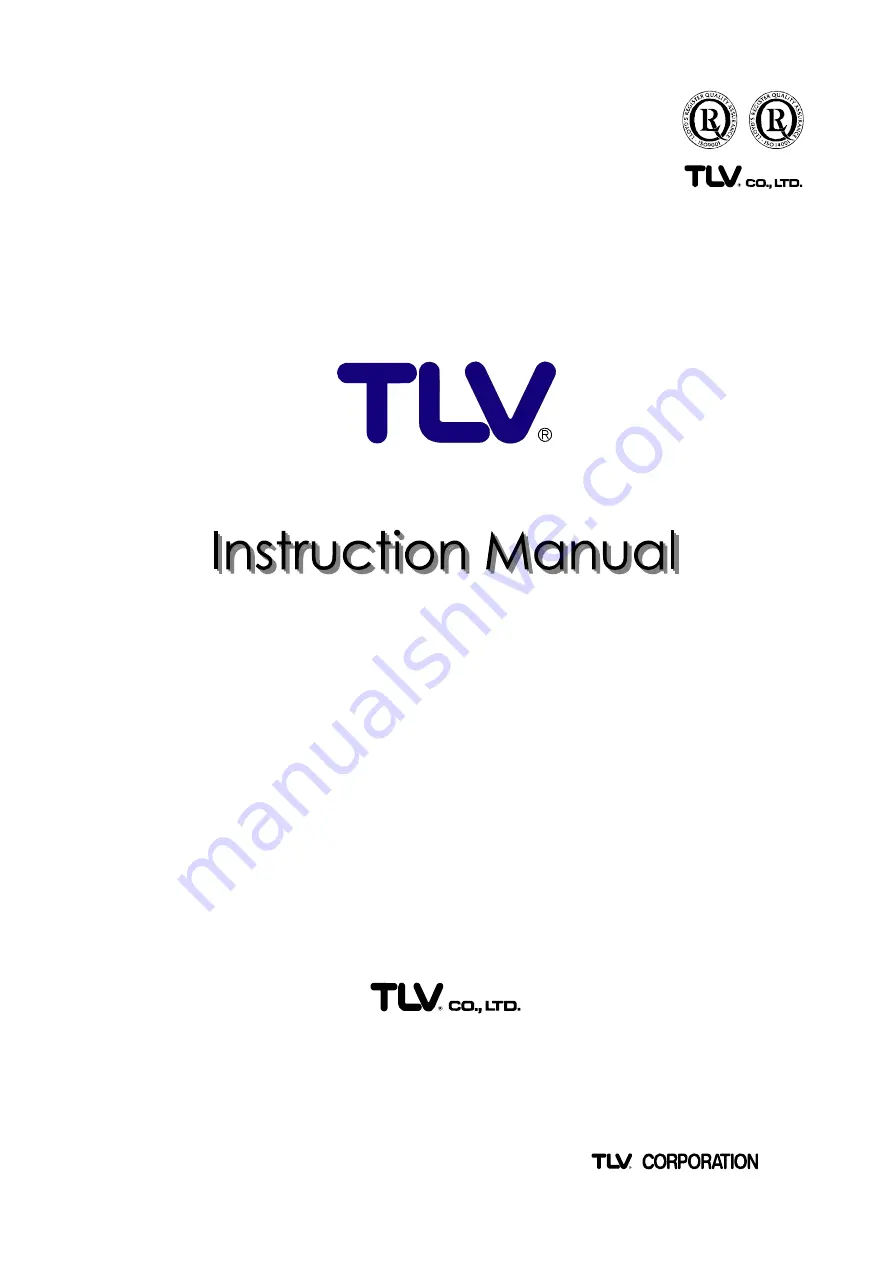
172-65185A-08 (MC-COSR Multi-control Valve) 20 November 2014
Manufacturer
881 Nagasuna, Noguchi, Kakogawa, Hyogo, 675-8511 Japan
Tel: [81]-(0)79-422-1122 Fax: [81]-(0)79-422-0112
Copyright © 2014 by TLV Co., Ltd. All rights reserved
ISO 9001/ ISO 14001
Manufacturer
Kakogawa, Japan
is approved by LRQA LTD. to ISO
9001/14001
High-precision Multi-control Valve for Steam
MC-COSR-3/MC-COSR-16
Actuator: MC-GA2