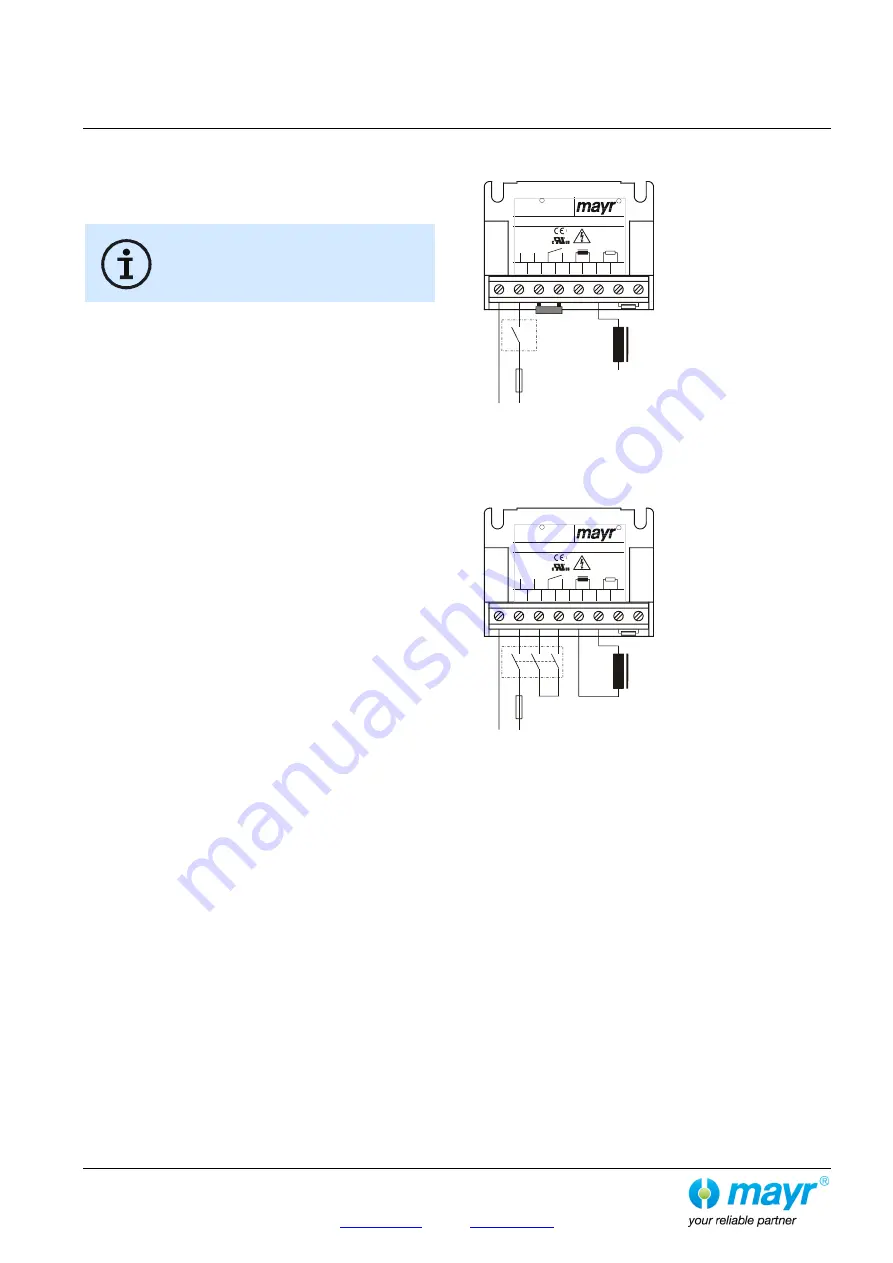
Installation and Operational Instructions for
ROBA-stop
®
-Z Type 892.101.0
Size 125
(E073 01 046 000 4 EN)
14/10/2013 TK/HW/SU
Chr. Mayr GmbH + Co.
KG
Eichenstraße 1, D-87665 Mauerstetten, Germany
Tel.: +49 8341 804-0, Fax: +49 8341 804-421
Page 10 of 14
www.mayr.com
, E-Mail:
Electrical Connection and Wiring
In safety applications, the rules for risk minimisation and error
avoidance (e.g. redundance, diversity, resistance, monitoring
etc.) must be observed during electrical activation.
The power is connected using a 2-core cable (9).
The brake must only be operated with
overexcitation (see Technical Data).
DC current is necessary for operation of the brake. The coil
voltage is indicated on the Type tag as well as on the brake body
and is designed according to the DIN IEC 60038 (± 10 %
tolerance). The brake must only be operated with overexcitation
(e.g. using a ROBA
®
-switch or -multiswitch fast acting rectifier or
phase demodulator). The connection possibilities can vary
dependent on the brake equipment. Please follow the exact
connections according to the Wiring Diagram. The manufacturer
and the user must observe the applicable regulations and
standards (e.g. DIN EN 60204-1 and DIN VDE 0580). Their
observance must be guaranteed and double-checked!
Earthing Connection
The brake is designed for Protection Class I. This protection
covers therefore not only the basic insulation, but also the
connection of all conductive parts to the protective conductor
(PE) on the fixed installation. If the basic insulation fails, no
contact voltage will remain. Please carry out a standardised
inspection of the protective conductor connections to all
contactable metal parts!
Device Fuses
To protect against damage from short circuits, please add
suitable device fuses to the mains cable.
Switching Behaviour
The operational behaviour of a brake is to a large extent
dependent on the switching mode used. Furthermore, the
switching times are influenced by the temperature and the air
gap between the armature disk and the coil carrier (dependent
on the wear condition of the linings).
Magnetic Field Build-up
When the voltage is switched on, a magnetic field is built up in
the brake coil, which attracts the armature disk to the coil carrier
and releases the brake.
Magnetic Field Removal
AC-side Switching
The power circuit is
interrupted before the
rectifier. The magnetic field
slowly reduces. This delays
the rise in braking torque.
When switching times are not
important, please switch AC-
side, as no protective
measures are necessary for
the coil and the switching
contacts.
AC-side switching means
low-noise switching
; however, the
brake engagement time is longer (approx. 6-10 times longer than
with DC-side switching), use for non-critical braking times.
DC-side Switching
The power circuit is
interrupted between the
rectifier and the coil as well as
mains-side. The magnetic
field reduces extremely
quickly. This causes a quick
rise in braking torque.
When switching DC-side, high
voltage peaks are produced
in the coil, which lead to wear
on the contacts from sparks
and to destruction of the
insulation.
DC-side switching means
short brake engagement times (e.g.
for EMERGENCY STOP operation)
; however, louder switching
noises.
Protection Circuit
When using DC-side switching, the coil must be protected by a
suitable protection circuit according to VDE 0580, which is
integrated in
mayr
®
-rectifiers. To protect the switching contact
from consumption when using DC-side switching, additional
protective measures are necessary (e.g. series connection of
switching contacts). The switching contacts used should have a
minimum contact opening of 3 mm and should be suitable for
inductive load switching. Please make sure on selection that the
rated voltage and the rated operating current are sufficient.
Depending on the application, the switching contact can also be
protected by other protection circuits (e.g.
mayr
®
-spark
quenching unit, half-wave and bridge rectifiers), although this
may of course then alter the switching times.
F1: External fuse
Coil
S1
F1
L
N
1
2
3
4
5
6
7
8
1 2 3 4 5 6 7 8
20/017.000.2
200 - 500V~
200 - 300V~
:
R
IN
OUT
U– = 0,45×U~
+
–
S
DC
ROBA -switch
I
= 1,8A
max
–
0,05-2sec
0 -10M
Ω
Ω
t:
R
R
F1: External fuse
Coil
S1
F1
L
N
1
2
3
4
5
6
7
8
1 2 3 4 5 6 7 8
20/017.000.2
200 - 500V~
200 - 300V~
:
R
IN
OUT
U– = 0,45×U~
+
–
S
DC
ROBA -switch
I
= 1,8A
max
–
0,05-2sec
0 -10M
Ω
Ω
t:
R
R
Содержание TW63B
Страница 1: ...thyssenkrupp Aufzugswerke Operating manual TW63B drive...
Страница 84: ...Part No 9950 000 6021 mit 1024 Imp Part No 9950 000 6021 mit 4096 Imp...
Страница 85: ...Part No 00 990 16 03 0 with 1024 pulses...
Страница 86: ...Part No 00 990 19 03 0 mit 1024 Imp...
Страница 87: ......
Страница 103: ...Design for TW63...
Страница 104: ......