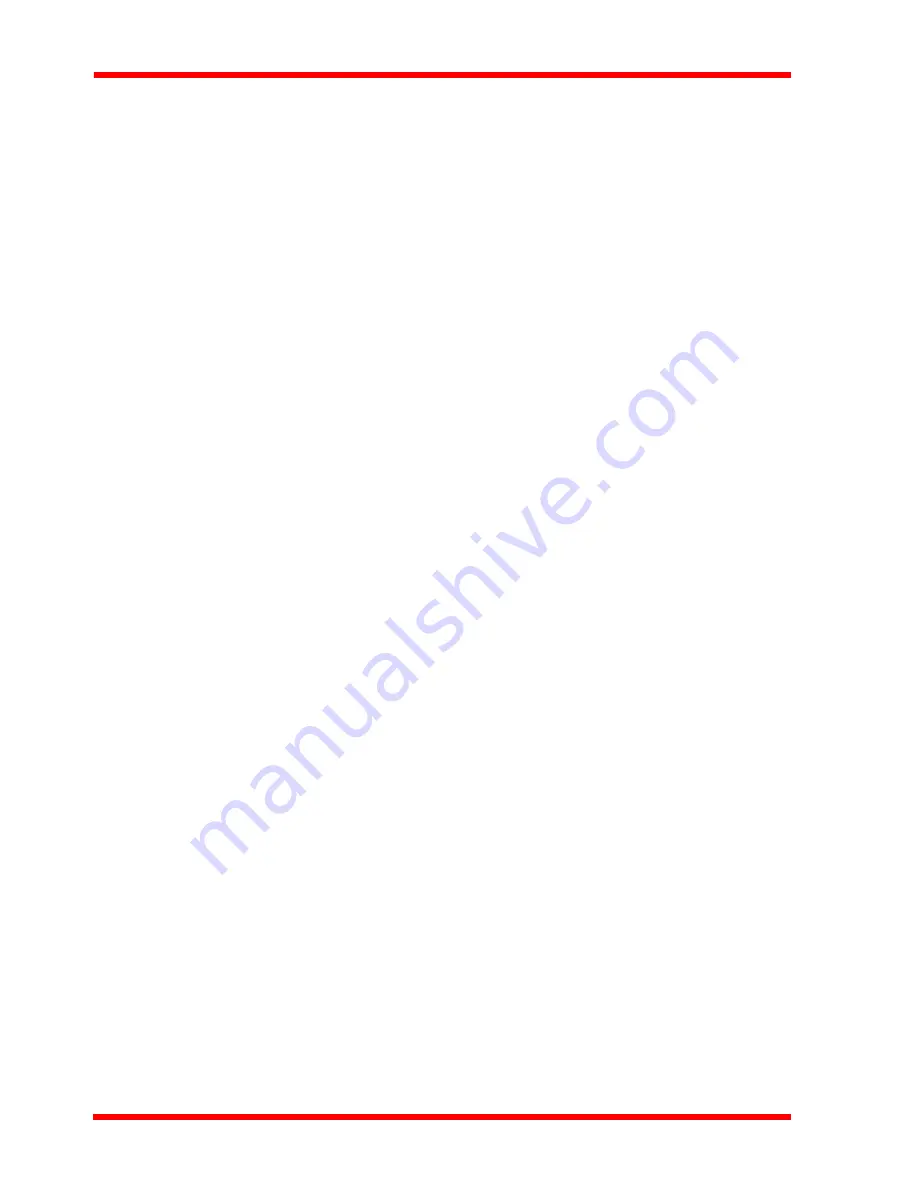
64
Appendix B
PID Tutorial
The TPA101 implements a PID control loop for closed loop control. A PID
(Proportional-Integral-Derivative) controller is a widely used feedback mechanism
that is relatively easy to tune.
The reason why tuning is required in most cases is because individual setups can be
very different. Different systems, consisting of complex electrical and opto-
mechanical components will respond to external stimuli in different ways. For
example, opto-mechanical components, such as turning mirrors usually have
mechanical resonance points due to their inertial mass and elasticity; in addition
electrical controllers cannot force them to move instantaneously. One practical way
of dealing with widely varying systems parameters is by making the control loop
tuneable so that the loop can be optimized for a given system and application.
The aim of closed loop control is to ensure that the beam is always centered in the
middle of the detector; tuning the closed loop parameters will determine how the
system responds to any disturbance that attempts to move the beam out of the centre
position. Tuning the controller involves finding a set of values that results in a system
that is stable and responds to any disturbance as quickly as possible, restoring the
centre position of the beam.
In general, start with a low values for Proportional (P) and Integral (I). The default
values for these is 10 and 5 which normally result in an unconditionally stable system.
Usually, with low P and I values, the system is very stable but responds to
disturbances quite slowly. Low P and I values tend to dampen the internal mechanical
resonance of the system as well. As the P and I values are increased, the system
becomes quicker, which can be advantageous because it rejects external
disturbance, such as mechanical vibrations, more efficiently. If the P and I values are
increased further, at some point the system will become unstable and oscillate. In this
case the increasing the Differential (D) parameter can help, together with reducing the
PI parameters. The drawback of adding and increasing the Differential parameter is
that it also tends to accentuate noise in the system.
With some PID parameters, the opto-mechanical actuators used in typical setups can
sometimes show conditional stability as well. This means that while the system is
stable and in some cases appears relatively good at rejecting low-level disturbance,
such as small mechanical vibrations, large disturbances can provoke instability. This
can happen because opto-mechanical systems can exhibit non-linearity over large
excursions. In some cases this behaviour can be useful, especially when maximum
vibration rejection is needed and large disturbances are not likely to occur.