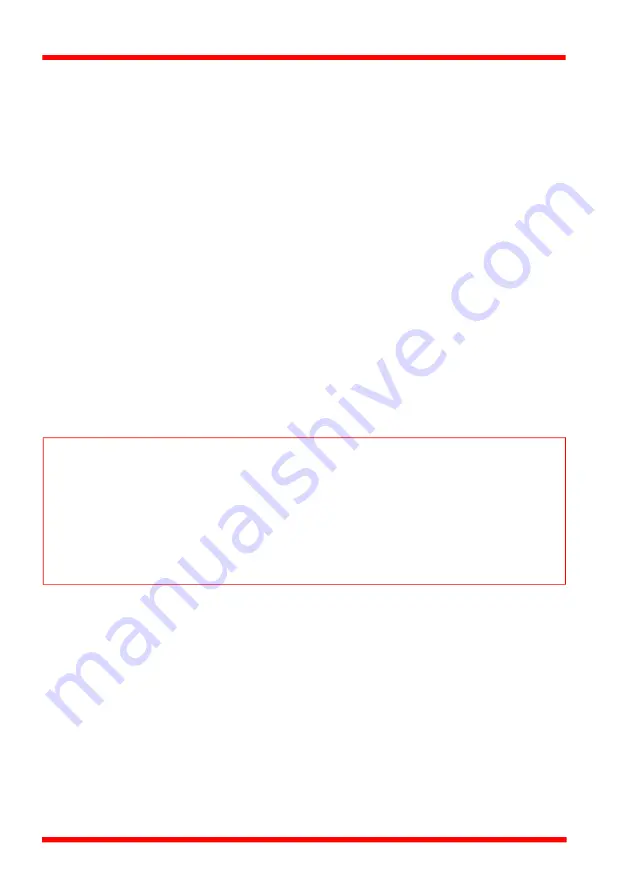
5
HA0114T Rev 10 May 2019
Chapter 3
Chapter 3 Set Up And Operation
3.1 Introduction
The functionality required for a client application to control a number of NanoTrak
units is provided by the NanoTrak Control Object within the APT server, with manual
operation being facilitated via a GUI panel (see Section 3.7.1.). Instances of this
ActiveX control can be dragged from the toolbox in the development software.
Alternatively, the APT User utility allows multiple graphical instrument panels to be
displayed so that multiple APT units can be controlled. All basic operating parameters
can be set through this program, and all basic operations (such as setting circle
diameter) can be initiated.
The APT Software Server System has been designed to allow custom
nanopositioning applications to be developed in a Microsoft Windows environment.
The use of ActiveX interfacing technology means that programming of the unit can be
achieved in any compatible language (LabVIEW, Visual Basic etc.) without the need
for an extensive library of language-specific functions.
Using the methods and properties described in the
APTServer helpfile
, the APT
NanoTrak controller can be programmed as part of an automated alignment
application.
Note
Before using the NanoTrak, ensure that the fibers can be aligned manually using the
actuators on the positioning stage, and that the expected level of power can be
transmitted between them. Set the NanoTrak to Latch and the range control to Auto,
and observe the bar graphs on the front panel for an indication of power.
If the positioning stage incorporates stepper motor actuators, ensure that the motors
are disabled via the stepper motor controller GUI panel before performing any
manual adjustment.