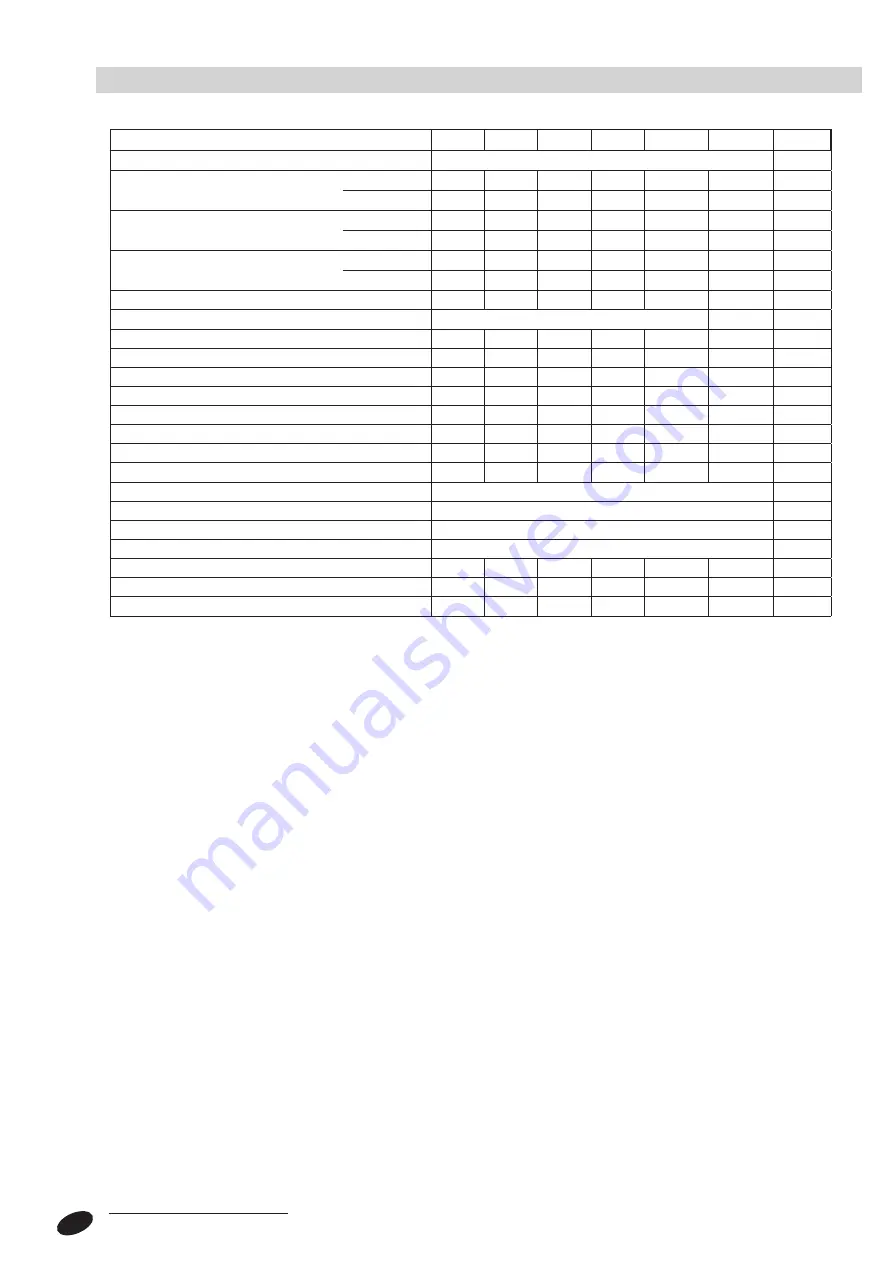
12
TECHNICAL DATA FOR BOILERS WITH GAS BURNERS <400 KW
(*) Heating appliance marketed before 1 January 2018, intended exclusively for replacement under the terms of EU
Regulation 813/2013, article 1,section 2, letter (g).
THE/TG 3S
90(*)
115(*)
166(*)
217(*)
255(*)
349(*)
Fuel
Gas
Rated heat input
minimum
70,0
90,0
115,0
166,0
217,0
255,0
kW
maximum
90,0
115,0
166,0
217,0
255,0
349,0
kW
Rated useful heat output Pn
minimum
66,6
85,5
109,6
158,7
206,2
243,0
kW
maximum
85,1
108,3
157,4
207,5
244,0
334,7
kW
Useful efficiency
at min. Pn
95,2
95,0
95,3
95,6
95,0
95,3
%
at max. Pn
94,5
94,2
94,8
95,6
95,7
95,9
%
Useful efficiency at 30% (Pn Max)
98,5
98,5
98,5
98,5
98,5
98,5
%
Constant pressure drop (Pn Max)
< 1,4
< 1,2
%
Flue gas temperature (∆T°)
106
103
103
106
100
106
°C
Flue gas mass flow rate (Pn Max)
0,040
0,050
0,072
0,094
0,110
0,151
Kg/s
Furnace pressure
1,0
1,4
1,8
2,7
2,9
3,6
mbar
Furnace volume
75,0
121,0
176,0
176,0
240,0
296,0
dm
3
Total volume of flue gas side
112
176
2.535
2.615
3.575
443
dm
3
Surface area for heat exchange
3,8
5,3
7,3
8,2
10,1
12,9
m
2
Volumetric heat load (Pn Max)
1.203
947
941
1.229
1.066
1.180
kW/m
3
Specific heat load (Pn Max)
22,6
20,4
21,4
25,4
24,3
26,0
kW/m
2
Maximum operating pressure
6
bar
Maximum admissible temperature
110
°C
Maximum operating temperature
95
°C
Min. admissible water return temper.
50
°C
Pressure drop ∆T 10° C
22
25
27
45
43
75
mbar
Pressure drop ∆T 20° C
7
5
5
10
13
20
mbar
Water capacity
176
255
319
309
408
495
l
Содержание 20034707
Страница 1: ...THE TG INSTALLATION OPERATION MAINTENANCE AND SYSTEM MANAGEMENT MANUAL...
Страница 39: ...39 ENGLISH GENERAL 39...