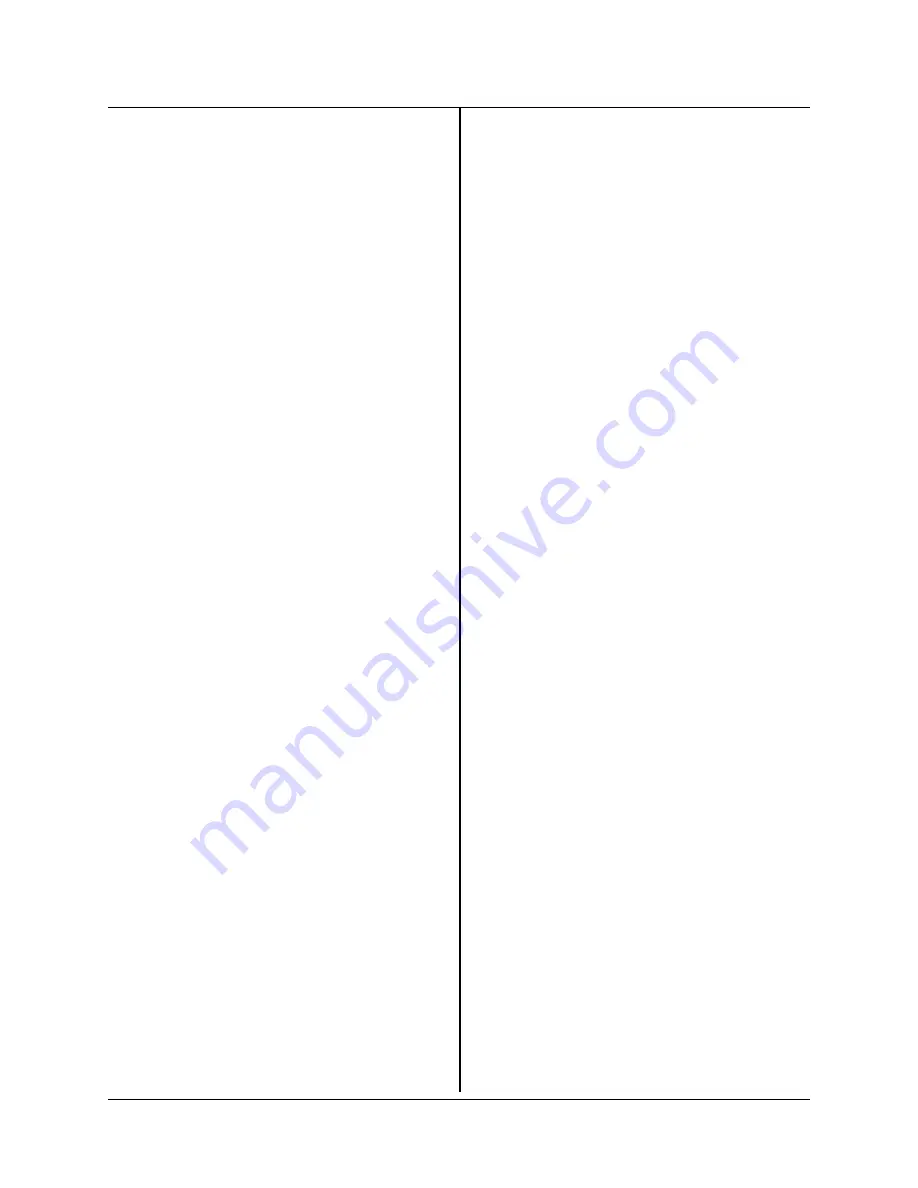
GMAW/FCAW Operation
The GMAW mode on the Ultra Flex
®
350 power
source provides a constant voltage output charac-
teristic. Variable inductance is also provided.
To operate proceed as follows:
1. Connect the wire feeder to the 19 pin amphenol
receptacle on the rear of the power source.
2. Connect the welding leads to the power source
and wire feeder, make sure connections are tight
and polarity is correct.
3. Turn AC power switch to the ON position. The
initial power up sequence will be complete in ap-
proximately 3 seconds.
4. Press the GMAW button to select the GMAW
process. The light next to the button should be on
indicating that GMAW is now the active process.
5. For LOCAL control make sure the REMOTE
light is off by pressing the REMOTE button if nec-
essary. The light should toggle on and off as the
REMOTE button is pressed repeatedly.
6. To adjust output voltage first press the A/V
button and then use the UP and DOWN buttons to
adjust the voltage setting. For remote control, make
sure that the light next to the REMOTE button is on,
by pressing the REMOTE button if necessary. Then
use the voltage control on the wire feeder to preset
output voltage.
7. To adjust the INDUCTANCE setting first press
the AF/IND button, and then use the UP and DOWN
buttons to set an inductance value between 0 and
100. The minimum inductance setting is 0. 100 is
the maximum setting. Lower values give a faster
cooling puddle with a “harsher” type of arc. Higher
inductance settings give a very soft arc and a slower
cooling puddle. As a general rule, most materials
can be welded with a setting around 50. Mild steel
normally runs best from minimum to mid range,
stainless steel normally runs best from mid range to
maximum.
NOTE: The inductance control is primarily
used for the short-circuiting transfer mode
of MIG welding. For globular and spray
transfer modes, the inductance control has
minimal effect.
8. The power source is now ready to weld. To
initiate the weld, activate the torch switch on the MIG
torch.
9. To end the weld, release the torch switch while
holding the torch in place at the end of the weld. This
will allow the wire conditioning circuit in the power
source to condition the end of the wire for the next
weld. The wire conditioning circuit will tend to leave
the wire with a very small ball on the end of the wire,
thus making the next start easier.
Pulsed GMAW
General
Pulsed-GMAW (referred to as Pulse-MIG) is a
welding process that involves the pulsing of the
welding current from a high value (peak current) to
a low value (background current) to produce a clean
spatter-free weld. The intent of this manual is not to
present a comprehensive coverage of this welding
process, but to give an explanation of the terms
used and how they apply to the Ultra Flex
®
350
power source.
Explanation of Terms: (See Figure 5-4)
I
st
: I
st
is the amplitude of the initial pulse of current
during the arc starting interval.
I
pk
: I
pk
is the amplitude of the high pulse of welding
current (peak current). The current is forced to this
high value by the power source for a brief time
(T
peak
). The peak current melts the wire and forms
a droplet. This droplet is then propelled to the weld
pool.
V
pk
: V
pk
is the amplitude of the arc voltage during
the high pulse of weld current.
T
pk
: T
pk
is the amount of time that is spent at the
peak current. This time must be sufficient to form a
droplet.
I
bak
: I
bak
(background current) is the low value of
the weld current. The background current serves to
preheat the wire and maintain the arc between the
wire and the workpiece. The background current
must not be allowed to go too low, or the arc
becomes unstable and difficult to maintain.
V
bak
: V
bak
is the amplitude of the arc voltage
during the background time.
T
bak
: T
bak
(background time) is the amount of time
that the weld current is at the low value. Normally,
this would be a larger amount of time than is spent
at peak current.
Pulse Rate: The pulse rate is the number of
pulses of current that are produced per second. The
Ultra Flex
®
350 allows a pulse rate of approximately
30–300 pulses per second.
Pulsing Frequency: Pulsing frequency is the
same as pulse rate. A pulse rate of 60 Hz means
that the power source produces 60 pulses of current
per second.
430429-465
OPERATION
5-6
February 28, 2000
Содержание ULTRA FLEX 350
Страница 4: ...This page intentionally left blank 430429 465 INTRODUCTION 1 2 February 28 2000...
Страница 15: ...Figure 3 2 Volt Ampere Curves 430429 465 DESCRIPTION OF EQUIPMENT February 28 2000 3 3...
Страница 22: ...This page intentionally left blank 430429 465 INSTALLATION 4 4 February 28 2000...
Страница 34: ...This page intentionally left blank 430429 465 OPERATION 5 12 February 28 2000...
Страница 36: ...This page intentionally left blank 430429 465 MAINTENANCE 6 2 February 28 2000...
Страница 40: ...This page intentionally left blank 430429 465 TROUBLESHOOTING 7 4 February 28 2000...
Страница 42: ...Figure 8 1 Ultra Flex Welder Assembly 430429 465 PARTS LIST 8 2 February 28 2000...
Страница 44: ...Figure 8 2 430429 465 PARTS LIST 8 4 February 28 2000...
Страница 46: ...This page intentionally left blank 430429 465 PARTS LIST 8 6 February 28 2000...
Страница 47: ......
Страница 48: ......
Страница 49: ......