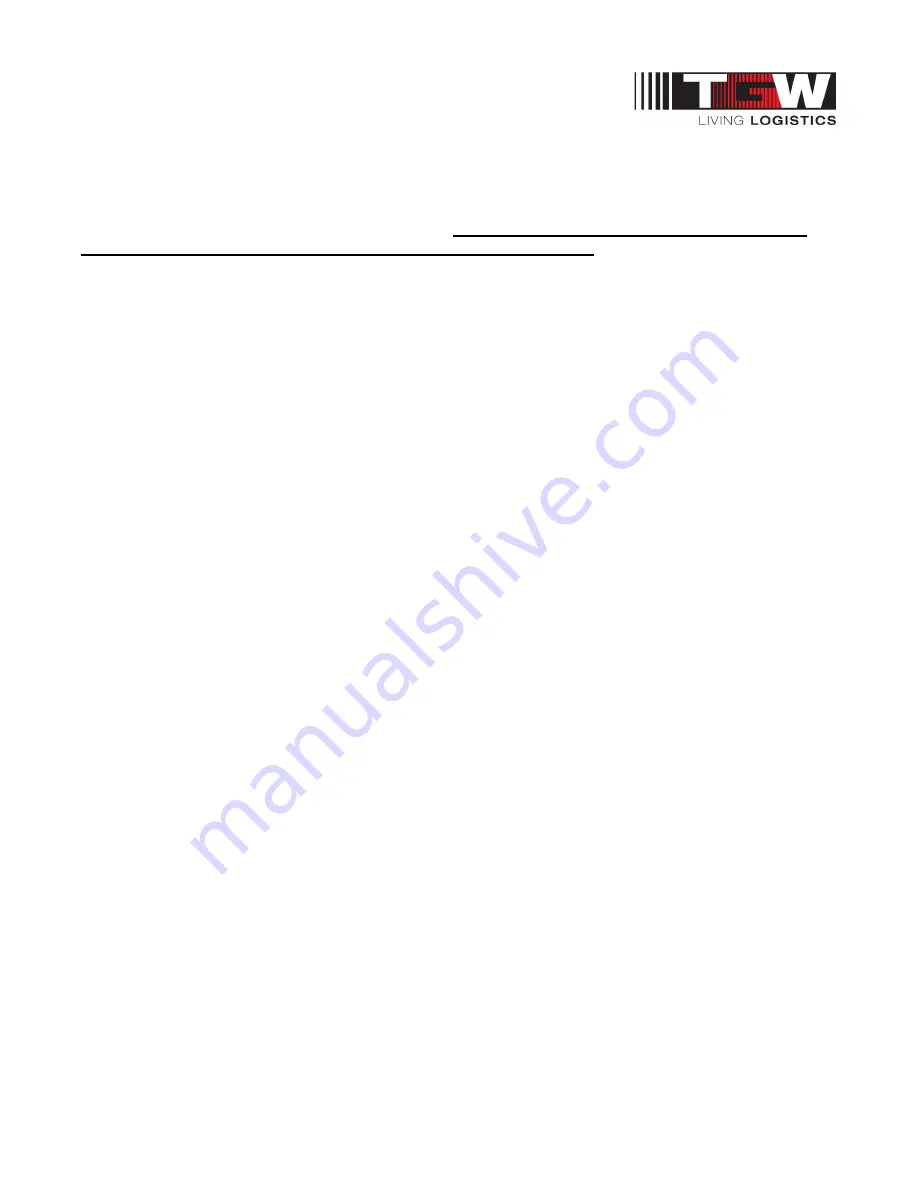
NBS®90 PolySort & SP IOM
P/N: 1193974
Revision Date: 4/25/2019
Page
12
of
83
3.4: TGW
S
YSTEMS
C
ONVEYOR
C
ONTROLS
S
AFETY
G
UIDELINES
The following basic conveyor control safety guidelines are recommended by TGW Systems even
though Business Partner may or may not purchase conveyor controls from TGW Systems. The items
listed deal with applications of controls equipment.
The actual installation of the equipment must
always follow the National Electric Code and all other local codes.
Start-up Warning Horn
Ideally, all conveyors should be within sight of the conveyor start pushbutton. This allows the operator
to verify that no one is touching the conveyor or would be in danger if the conveyor were to start up.
If it is not possible to see the entire conveyor being started from the start pushbutton location, then
some form of audible warning device is required. It could be a horn, buzzer, bell, or anything unique to
that conveyor for that location. It should be loud enough to be heard at any point on the conveyor
system. It should sound for approximately five seconds after the start pushbutton is pushed, prior to the
actual running of conveyor. Any auxiliary equipment such as vertical lifts, turntables, etc., should also
be included in the warning circuitry.
Conveyors that stop and restart under automatic control could also require a horn warning prior to
restarting. If it is not easy to distinguish the difference between a fully stopped conveyor system and a
momentarily stopped conveyor section, then it is advisable to add a warning horn. All conveyor sections
that stop and restart automatically should be marked with appropriate signs or labels.
Start Pushbuttons
Start pushbuttons should be the flush type or guarded such that inadvertently leaning against them will
not actuate the conveyor. They should be provided with a legend plate clearly defining which conveyors
will be started.
Stop Pushbuttons
Stop pushbuttons should be the extended type such that any contact with it is sufficient to stop the
conveyor. They would also be provided with a legend plate clearly defining which conveyors will be
stopped.
Operator Controls
Additional operator controls should be designed into the system with the same guidelines that go into
start and stop pushbuttons, depending upon their function. Devices which are repeated on multiple
control stations, such as emergency stops, should be located at the same relative location on each
station (such as lower right corner).
Emergency Stops
All locations where an operator must work directly at the conveyor should be protected by an
emergency stop. An operator should not have to move from where he is to actuate the emergency stop.
Conveyors in areas of high pedestrian traffic should also be protected by emergency stop devices.
For all other instances, emergency stops should be located throughout a system such that it is possible
to shut down the system without having to walk too far. In these instances the emergency stop is used
more to protect the equipment from damage than to protect personnel.
Emergency stops can be of the pushbutton or cable operated switch type. The pushbutton type should
be a red, mushroom head maintained pushbutton which requires resetting after it is actuated. Cable
operated switches should trip by pulling the cable, and require resetting at the switch.
Содержание NBS 90 PolySort
Страница 29: ...NBS 90 PolySort SP IOM P N 1193974 Revision Date 4 25 2019 Page 29 of 83 ...
Страница 34: ...NBS 90 PolySort SP IOM P N 1193974 Revision Date 4 25 2019 Page 34 of 83 Divert 1 PE ...
Страница 35: ...NBS 90 PolySort SP IOM P N 1193974 Revision Date 4 25 2019 Page 35 of 83 Divert 1 Sol ...