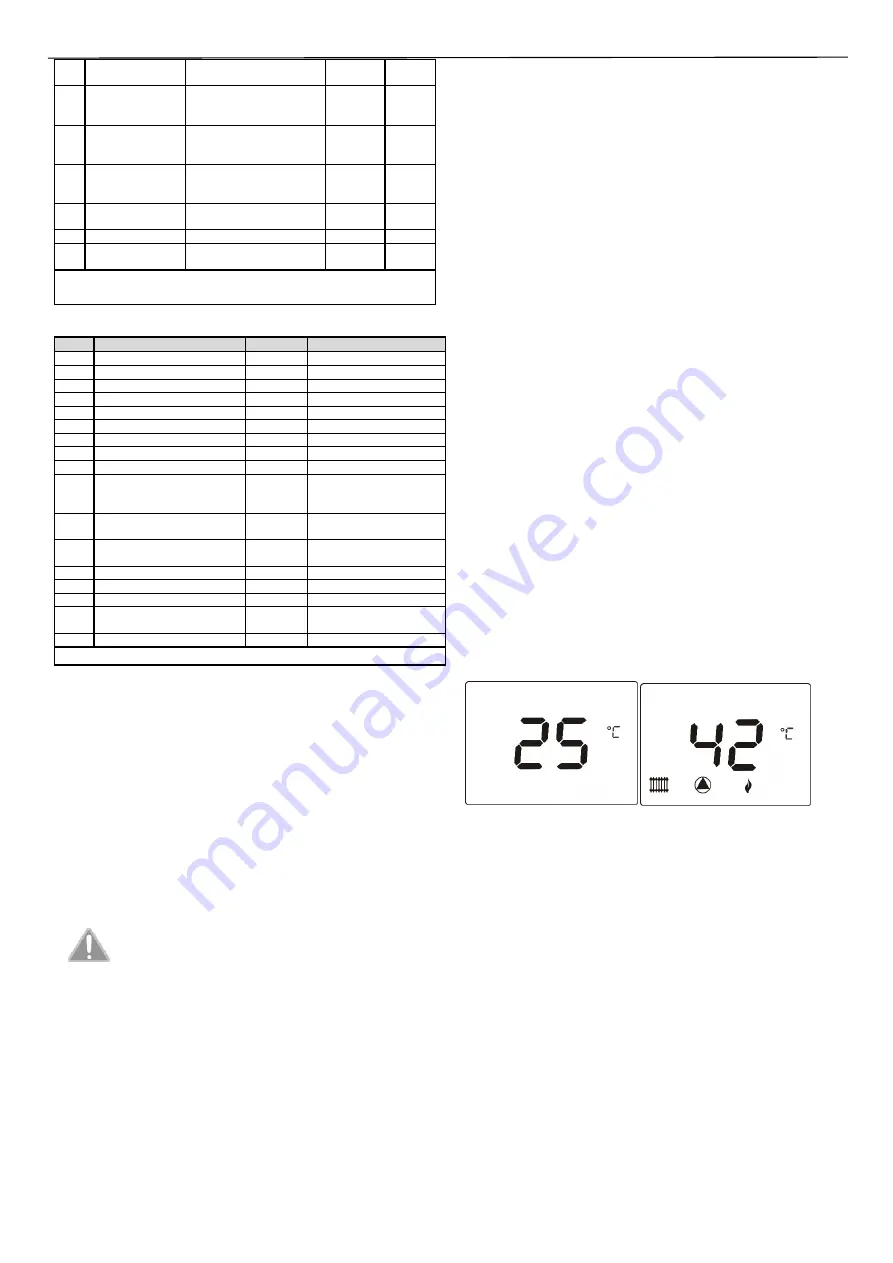
ISU-689:2016/GB
13
P36*
Max. of cascade
pump
Maximum PWM signal for
cascade pump
15-100%
100%
P37*
Quantity of DHW
boilers
Specifies the number of
boilers operating on heating
the domestic water
0 - 6
0
P38*
Antifreeze cascades -
ON
Temperature on the cascade
sensor to activate the
antifreeze function
°
C or
°
F
6
P39*
Antifreeze cascades -
OFF
Temperature on the cascade
sensor to the end of
antifreeze function
°
C or
°
F
15
P40*
Boiler switching
delay
Minimum break time /
operation of boiler in cascade
0-255s
20
P41* Sampling time
PI regulation parameter
P42* Operation mode - OT
0-standard
1-SMILE
0 - 1
0
* Parameters recorded in the boiler display plate
** It is recommended to leave unchanged
Table 4.5.1
–
Controller configuration parameters
No
Parameter
Unit
Description
P01
Ionization current
µ
A
P02
CH supply temperature
°
C
P03
CH return temperature
°
C
P04
DW temperature
°
C
P05
Water pressure
Bar*10
-1
Pressure in CH installation
P06
Power level
%
Level of burner power
P07
Required fan speed
50 * rpm
Required fan speed
P08
Current fan speed
50 * rpm
Measured fan speed
P09
Flue gas temperature
°
C
Inactive
P10*
Cascade supply temperature
°
C
If the temperature sensor
on the coupling is
connected
P11*
Outside temperature
°
C
Temperature measured by
external sensor
P12*
Degree of cascade modulation
%
Current relative degree of
cascade modulation
P13*
CH setting
°
C
P14*
DHW setting
°
C
P15*
Quantity of burners
---
Number of installed burners
P16*
Quantity of operating burners
---
Number of operating
burners
P17*
Quantity of displays
---
Number of boiler modules
* Parameters recorded in the boiler display plate
Table 4.5.1.1
–
Boiler control parameters
5. STARTUP AND OPERATION OF THE BOILER
5.1. Initial startup of the boiler
Before turning on the boiler for use, please check
•
hydraulic and flue installations are compatible with applicable law;
•
ground connection has been made;
•
expansion tank has sufficient capacity, appropriate to the content
of water in the system
;
•
discharge pipe from the safety valve has been connected;
•
type of gas corresponds to the gas to which the device was
designed (
→
name plate of the boiler);
•
gas supply pressure conforms to the expected values
.
After installing the boiler, checking the accuracy and
tightness of its connections and preparing for operation
in accordance to this instruction manual and applicable
regulations, first commissioning and user training for
boiler operation and safety devices may be done only by
AUTHORISED FACTORY SERVICE.
Venting the system:
•
Check whether the plug of boiler's automatic vent item 2.13 Fig
2.2.1.1 is loose, if not - loosen for half a turn.
•
Open the valves on the supply and return from the CH system to
the boiler.
•
Close the gas valve at the boiler connection.
•
Turn on the electrical boiler power.
•
Check the system pressure (see section 4.5.1, P05 parameter). The
pressure should be in the range of
1.2 ÷ 1.8bar.
In case of too low
pressure, fill the installation with a filling valve mounted on the
installation.
•
Start the boiler in the TEST service mode, the boiler will start the
circulation pump and start the ignition. Due to lack of gas after
failure of ignition test, error "01" will be displayed, which will allow
for continuous operation of the pump and removal of the incoming
air. The boiler should remain in this state until the noise of
removed air will disappear. Continue the procedure until vent the
installation.
•
Delete "01" error by using
[B]
button. Recheck the system
pressure.
After venting the system:
•
Check if flue pipe is not blocked and is properly connected to the
flue system;
•
Connect the boiler to a power source. Before starting operation,
the boiler controller performs self-checking;
•
Open gas valve,
•
Using
[E]
and
[D]
buttons, set the required CH water temperature
and accept with
[B]
button;
•
After setting the required temperature on the display, after a few
seconds the actual temperature of heating water will appear;
•
If you run the boiler and still hear a noise in the installation, it is
necessary to repeat priming steps in order to ensure complete
elimination of air from the system
;
•
Check the pressure in installation, if it has been reduced - open the
filling valve again until the display shows a value of 1.5 bar, and
after completing the operation close the filling valve;
•
Check the CO
2
value in flue gas. If the values does not correspond
to the values indicated in the Table 4.3.1, the boiler should be
adjusted in accordance with Section 4.3.
In the waiting state on demand the heat, the boiler displays on the
screen the current temperature measured by the sensor on the
power supply of the CH system, item 2.15, Fig. 2.2.1.1.
In the operating state, the display shows the current temperature on
the supply with the corresponding symbols.
5.2. Operating modes
Startup mode
–
after turns on the power or after a manual reset of
the boiler. In this mode, three-way valve and pump are supplied. If
there is no require for heat within 12 hours, the boiler is reset. Such
action is to prevent blocking of three-way valve and pump.
Standby mode
–
no heat demand.
TEST service mode
–
for a proper setting of the boiler, see section
4.3. In this mode, the fan speed is set between the minimum and
maximum values defined by parameters P27 and P28. The three-way
valve is set on CH. The burner starts at the startup power level
defined by parameter P33 and then goes to the required power
value. TEST mode can not be started if the controller signals an error.
Stand-by mode
–
mode in which the boiler is switched off, only
safety functions operates:
•
Antifreeze protection of the water in CH system, (the boiler
switches on when the boiler water temperature drops below
6°C
and heat the water until temperature reach
15°C ), burner’s power
is set on the lowest lever,
•
Antifreeze protection of the water in DHW system (the boiler
switches on when the boiler water temperature
–
in DHW circuit
–
drops below 6°C and heat the water until temperature reach 15°C
),
burner’s power is set on the lowest lever,