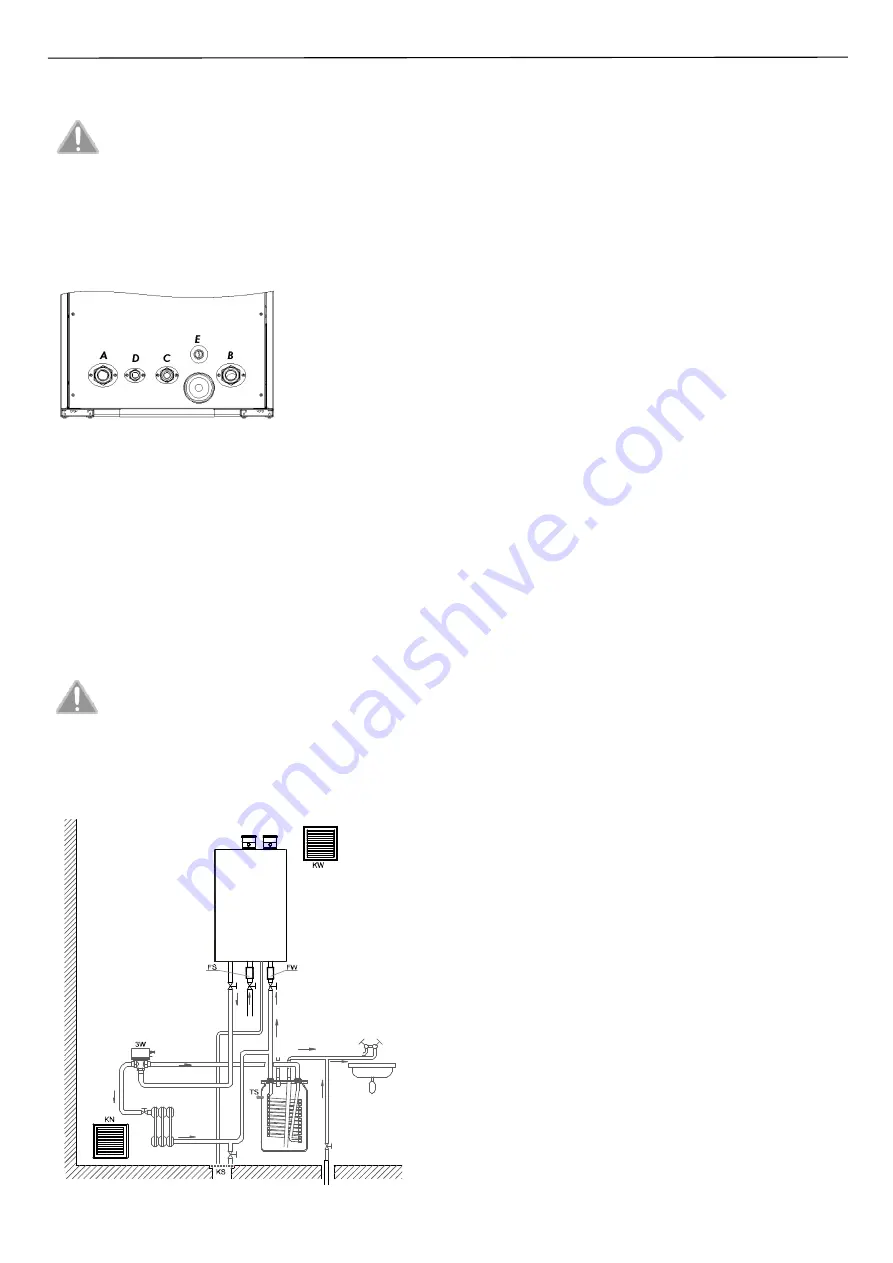
ISU-689:2016/GB
6
3.4. Connection to the gas installation
All connections should be made by an appropriately
qualified person, in accordance with applicable standards
and regulations, in particular those relating to safety.
Connect a gas supply pipe directly to the connector of the boiler gas
unit by means of standard connector subassembly. It is necessary to
install a gas filter on the gas supply pipe. This filter is not included in
the standard boiler equipment. The gas filter is necessary for a
proper operation of a gas unit and a burner. Install a cut-off valve on
the gas pipe in an accessible place.
A - (
G5/4”
)
–
Power supply of the CH
installation
B
–
(G5/4”)
–
return from the CH
installation
C
–
(G1”)
–
Gas connection
D
–
(G3/4”)
- Drain from the safety
valve / emptying the boiler
E
–
(
Ø
25)
- Condensate drain
Fig. 3.4.1
–
Description of the connectors
3.5. Connection of the boiler to a water system
Power connector and connector of return of the central heating
boiler should be screwed to the installation. Install a water filter on a
water return from central heating system (in front of the connection
with the pump). The filter is not included in standard boiler
equipment. The central heating system should be thoroughly rinsed
out before the boiler is connected. In the central heating system it is
permitted to use as a heat carrier any antifreeze fluids which can be
used in central heating systems.
The cut-off valves needs to be installed between the boiler and
central heating system so that the boiler could be dismounted
without draining the system.
Before installing the boiler thoroughly flush the central
heating system to free it from any solid impurities.
It is recommended that after first start-up of the boiler
and heating up of the installation drain the water from
the system to remove residues of pastes metallurgical
and precautionary measures of heaters. These activities
would benefit for the operation of the device, its
parameters and components life.
Fig. 3.5.1
–
Installation requirements
KW
–
Exhaust ventilation,
KN
–
Air inlet,
3W
–
three-way valve,
TS
–
Tank temp.
sensor,
KS
–
Floor drain,
FW
–
Water filter,
FS
–
gas filter.
After the boiler installation it is necessary to:
•
Fill the heating system with water. Filling the system should be
done slowly to allow the air outflow through the air vent valve
mounted in the boiler; also check the complete air outlet from all
components of the system.
The pressure in the cold installation
should be 1.2 ÷ 1.5 bar.
•
Check whether connections of the boiler and in the central heating
system are tight.
•
Ensure that pipes of water and heating installation are not used as
grounding the electrical installation.
•
Connect the outlet of safety valves to the floor drain to avoid
flooding the room (where the boiler is installed) as a result of
protection devices. Such outlets should be carried out so as to
avoid damage in the case of opening of the valve and outflowing of
the hot fluid.
3.5.2. Cleaning the installation and water treatment for
filling the CH installation
In all elements of the CH installation there are processes of scaling,
corrosion and similar phenomena. The boiler is the most expensive
part of the installation and it is important to ensure that the heat
exchanger and other components are protected against these
processes. Correct preparation of the CH system for the operation
shall be carried out by two operation: cleaning the installation and
water treatment for the operation of the installation.
Cleaning the installation
In new installation there may be remnants of the installation such as
solder residues, welding residues, flux residues, oil residues, grease
residues, or corrosion products - especially in old installation. In the
first place, both new and old installations should be cleaned with
clean water to remove solid waste. his operation must be carried out
without the boiler installed. The next step is to chemical cleaning the
installation. For cleaning new and old installations, use a suitable
cleaning agent, like Fernox Cleaner F3 (for old and heavily
contaminated installations use Cleaner F5). After this cleaning the
system should be rinsed with mains water.
Water treatment for filling the installation
Use the water with following parameters to fill the installation: pH
from 6,5 to 8,5 units, general hardness not more than
10 °n (~ 18°F).
For filling do not use demineralized water or distilled water. For
proper protection against scale and corrosion of the installation, use
a suitable inhibitor (passivator) e.g. Fernox Protector F1. In addition,
there can also be used a liquid heat carrier such as HP-5 or antifreeze
such as Fernox Alphi 11. In situations where water is very hard, the
use of the HP-5 liquid heat carrier effectively reduces the risk of
scaling of the heat exchanger.
Low-temperature circuits
In low-temperature zones it is recommended to treat the water by
using HP-5 liquid heat carrier or alternatively Fernox biocide AF10.
Filtering technology
In addition, modern filters with magnetic and cyclone effects are
recommended for the high quality of the current heating system.
The method and amount of use of the particular products for
cleaning the installation and for water treatment should be used
according to the instructions of the product given by the
manufacturer.
Cleaning the installation and water treatment should be made by
authorized installers or service personnel.