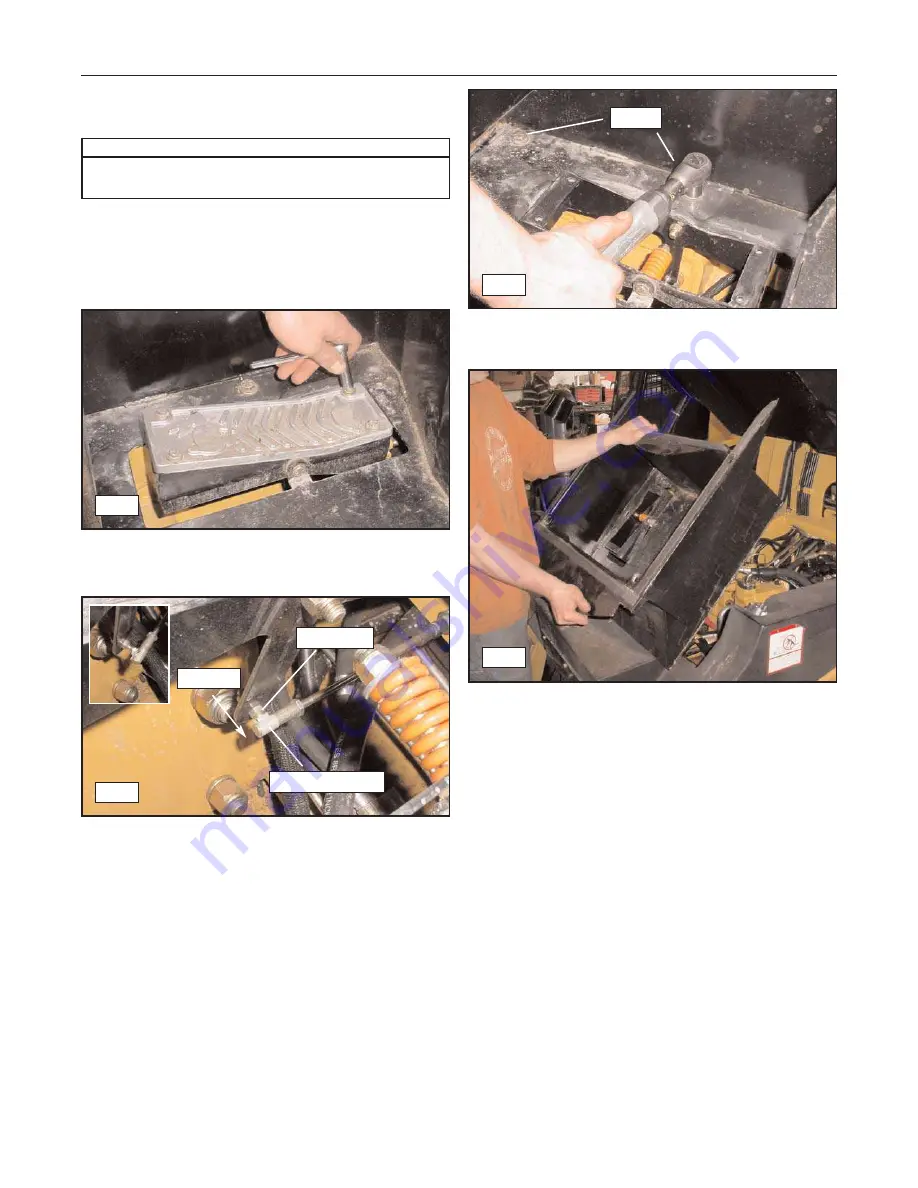
Footwell
Removal
1.
Raise and support the lift arms as described on
page 4-1 of this manual. (optional)
2.
Tilt and support the operator enclosure (cab) as
described on page 4-2 of this manual.
3.
Remove the bolts (4) securing the foot pedal cover
to the pedal, then remove the cover. (fig. 7-14)
4.
Pry the throttle cable off of the ball stud on the foot
pedal. (fig. 7-15)
5.
Remove the bolts (4) securing the footwell assem-
bly to the chassis. (fig. 7-16)
6.
Remove the footwell from the chassis as shown.
(fig. 7-17)
Installation
1.
To install the footwell, reverse the removal proce-
dure.
7-4
Rubber Track Loader
7. Chassis & Fuel Tank
7-14
Screwdriver
Combination/Socket Wrench
Required Tools
7-15
Pry Off
Throttle Cable
Ball Stud
7-16
7-17
Bolts
https://tractormanualz.com/
Содержание ASV SR70
Страница 5: ...IV https tractormanualz com...
Страница 11: ...1 6 https tractormanualz com...
Страница 41: ...4 20 https tractormanualz com...
Страница 87: ...12 8 https tractormanualz com...
Страница 105: ...14 6 https tractormanualz com...
Страница 109: ...15 4 https tractormanualz com...
Страница 125: ...16 16 https tractormanualz com...
Страница 133: ...17 8 https tractormanualz com...
Страница 137: ...18 4 https tractormanualz com...
Страница 139: ...19 2 https tractormanualz com...