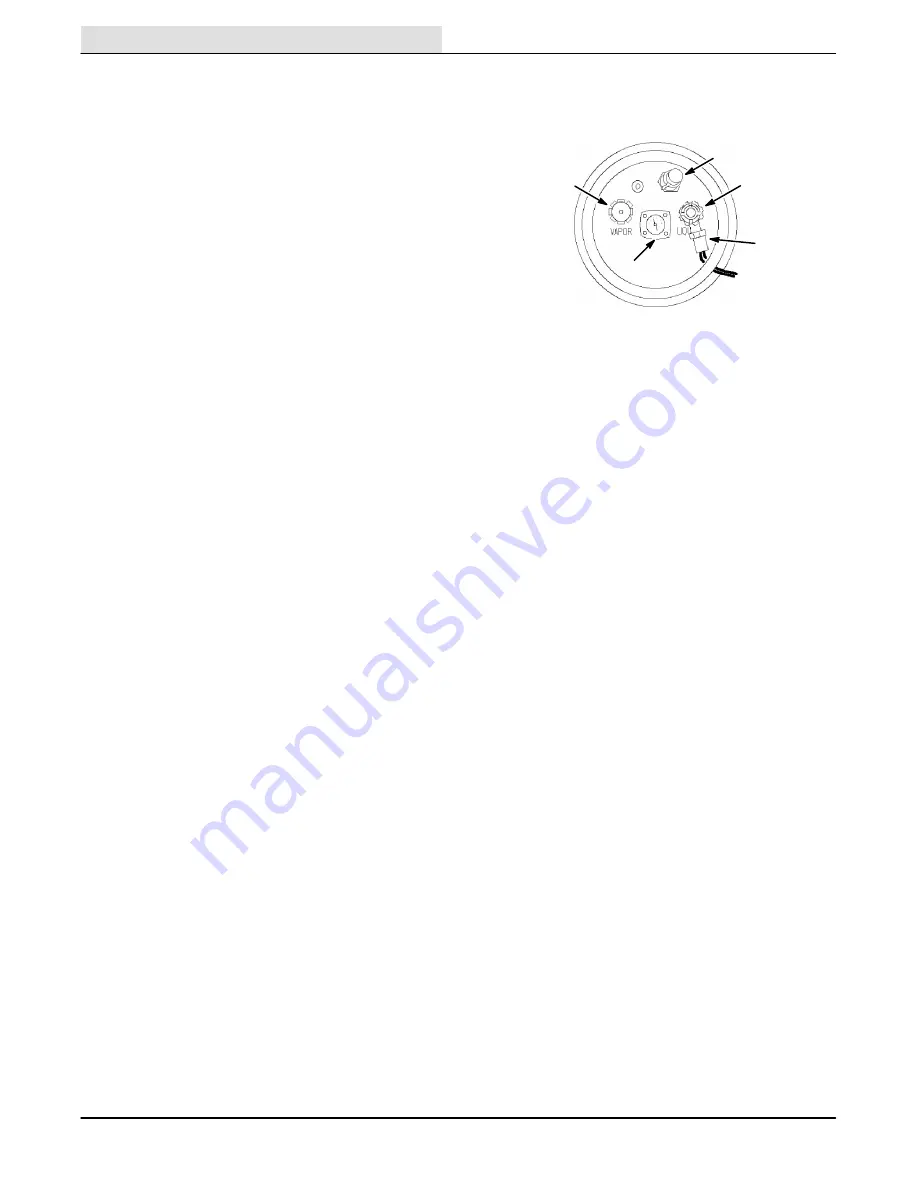
MAINTENANCE
365 MM173 (3---90)
3-22
Never operate an LPG powered machine if the LPG
fuel system is leaking, or if any component in the fuel
system is malfunctioning. Operating the machine
under either of these conditions may cause a fire or
explosion.
Check for frosting. If frosting occurs on or near any
LPG component, there is a possibility of an LPG fuel
leak or a malfunctioning component. To locate the
leak, apply a soapy water solution to the suspected
area. Watch for forming bubbles in the suspected
area. This area may have an LPG fuel leak. Repair or
replace the part. Use Loctite brand Stainless Steel
PST thread sealant when reassembling. This
epoxy-type sealant is not affected by aging or high
humidity. Be sure to follow application directions and
apply proper torque when reconnecting fittings.
Never bypass safety components except to test. If
the safety components are defective, replace them
before operating the machine.
Check routings of all LPG hoses. Keep them away
from sharp edges, exhaust manifolds, or other hot
surfaces. Check for signs of abrasion or
deterioration. Replace hoses found to be worn or
damaged.
FUEL TANKS
The LPG fuel tanks should be inspected for sharp
dents, gouges, leaks, and broken protecting rings
whenever the tanks are refilled. All tank valves must
be inspected for leaks using a soap solution. Valves
must also be checked for dirt, paint, or other debris
in the valve openings. The following specific checks
must also be made:
Filler Valve --- Check for proper functioning and the
presence of the handwheel. Valve must be closed
except during filling.
Vapor and Liquid Tank Service Valves --- Check for
proper functioning and presence of the handwheel.
The valve must be closed except when in service.
Tank Service Valve Coupling --- Check for proper
functioning, thread condition, and damaged or
missing washers or o-rings.
Safety Relief Valve --- Check for damage. Check for
the presence of the relief valve elbow and the proper
direction of the elbow. If the rain cap is missing,
check for foreign matter and replace the rain cap. Do
not tamper with the relief valve setting.
Magnetic Liquid Level Gauge --- Check operation
against the maximum filling point as determined by
weight.
D
C
A
B
E
03485
TYPICAL LPG LIQUID WITHDRAWAL FUEL TANK
A. Filler Valve
B. Safety Relief Valve
C. Liquid Tank Service Valve
D. Magnetic Liquid Level Gauge
E. Tank Service Valve Coupling
An LPG fuel tank with any of the stated defects must
be removed from service and be repaired or
destroyed accordingly.
If an LPG fuel tank is damaged or leaking, it should
be removed to a designated safe area, and the
proper personnel should be notified. Do not attempt
to make repairs to the tank, regardless of condition.
Repairs or disposal must only be made by qualified
personnel.
The care an LPG fuel tank receives has a direct
bearing on how long that tank can be used safely.
LPG fuel tanks must not be dropped or dragged
across any surface. To move LPG fuel tanks, use a
hand truck or roll the tank on its foot ring while it is
being held in a position slightly off vertical.
Whether the storage is inside or outside, fuel tanks
should not be stored in the vicinity of combustible
materials or high temperature sources such as ovens
and furnaces, since the heat may raise the pressure
of the fuel to a point where the safety relief valves
would function. Take care to insure that the tanks are
stored in such a way that if the safety relief valves do
function, they will relieve vapor, rather than liquid.
Valves on empty tanks must be closed during
storage and transportation.
Содержание 365
Страница 1: ...r 365 MM173 ...
Страница 6: ...ABOUT THIS MANUAL 365 MM173 3 90 d ...
Страница 16: ...SPECIFICATIONS 365 MM173 3 90 1 2 ...
Страница 20: ...SPECIFICATIONS 365 MM173 3 90 1 6 ...
Страница 22: ...OPERATION 365 MM173 3 90 2 2 ...
Страница 42: ...OPERATION 365 MM173 3 90 2 22 ...
Страница 56: ...MAINTENANCE 365 MM173 3 90 3 14 03767 HYDRAULIC SCHEMATIC ...
Страница 74: ...MAINTENANCE 365 MM173 3 90 3 32 03768 ELECTRICAL SCHEMATIC For machines below serial number 007000 ...
Страница 75: ...MAINTENANCE 3 33 365 MM173 3 90 03768 ELECTRICAL SCHEMATIC For machines below serial number 007000 ...
Страница 76: ...MAINTENANCE 365 MM173 3 90 3 34 03768 ELECTRICAL SCHEMATIC For machines serial number 007000 and above ...
Страница 77: ...MAINTENANCE 3 35 365 MM173 3 90 03768 ELECTRICAL SCHEMATIC For machines serial number 007000 and above ...
Страница 98: ...MAINTENANCE 365 MM173 3 90 3 56 ...
Страница 100: ...APPENDIX 365 MM 3 90 4 2 ...