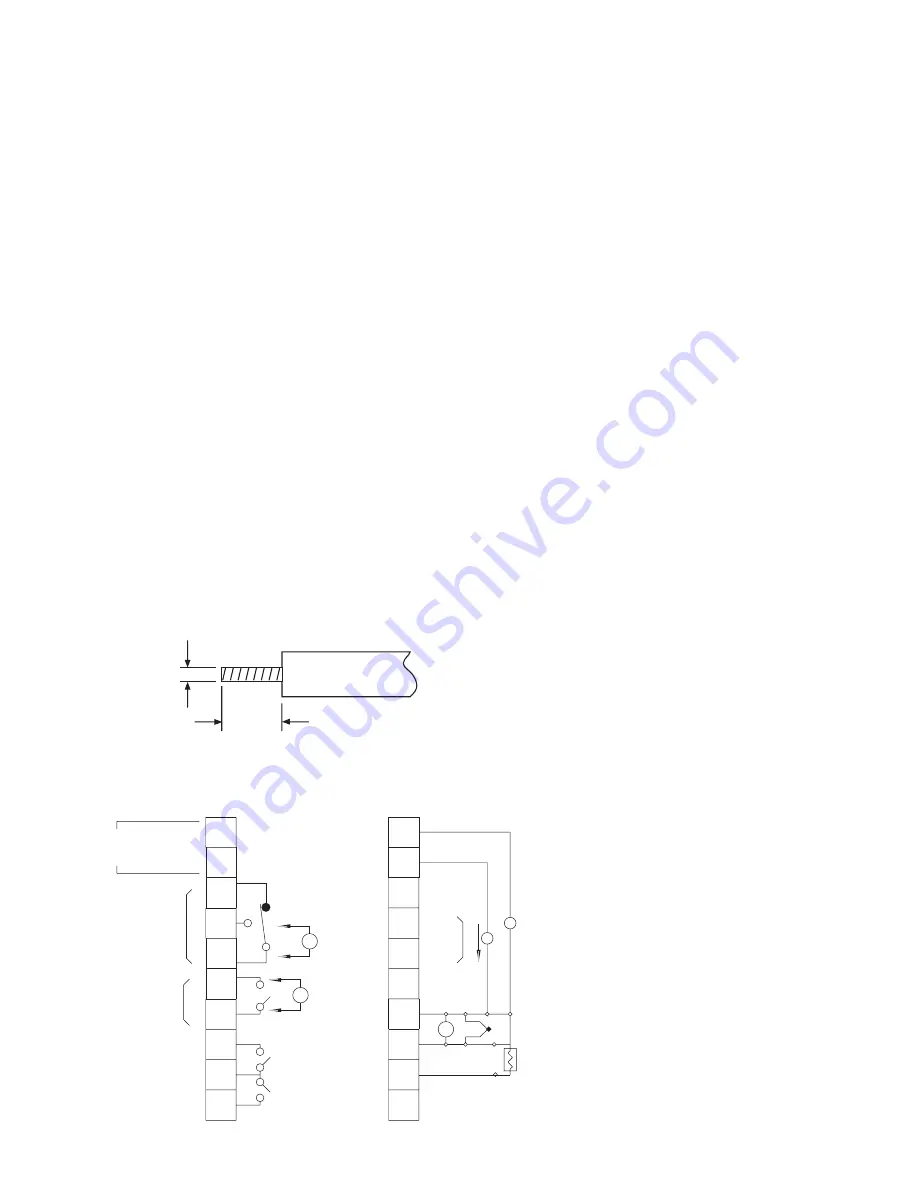
4–3 Wiring Precautions
• Before wiring, check the label to verify the correct model number and options. Switch off the power while checking.
• Care must be taken to ensure that the maximum voltage ratings specified in section 3 are not exceeded.
• It is recommended that the power source for these units be protected by fuses or circuit breakers rated at the minimum
value possible.
• All units should be installed inside a suitably grounded metal enclosure to prevent live parts from being accessible to
human hands and metal tools.
• All wiring must conform to the appropriate standards of good practice and local codes and regulations. Wiring must be
suitable for the voltage, current, and temperature ratings of the system.
• The "stripped" leads as specified in figure 4.2 below are used for power and sensor connections.
• Beware not to over-tighten the terminal screws.
• Unused control terminals should not be used as jumper points as they may be internally connected, causing damage to
the unit.
• Verify that the ratings of the output devices and the inputs are not exceeded.
• Electrical power in industrial environments contains a certain amount of noise in the form of transient voltage and
spikes. This electrical noise can adversely affect the operation of microprocessor-based controls. For this reason we
strongly recommend the use of shielded thermocouple extension wire which connects the sensor to the controller. This
wire is a twisted-pair construction with foil wrap and drain wire. The drain wire is to be attached to ground at one end
only.
4–4 Connection and Wiring
The following connections for outputs and inputs are found on the back of the controller housing.
7
4.5 7.0 mm
0.18" 0.27"
~
~
2.0mm
0.08" max.
Figure .2 Lead Termination
Figure 4.2 Lead Termination
+
-
0-10V
+
-
Interface
RTD
0-20mA or 4-20mA
V-
mA-
AC1
AC2
N/C
I
+
-
V
I
V
V
+
-
PTB/COM.
PTB/TC
PTA
+
-
N/O
-
+
-
+
C
Control
Output 2
Alarm 1
Alarm 2
Alarm Com.
1
2
3
4
5
6
7
8
9
10
11
12
13
14
15
16
17
18
19
20
+12V
Tx1
Tx2
0V
Control
Output 1
90-264 VAC
Power Input
+
-
VAA
Tx1
Tx2
-VAA
Figure 4.3 Rear Terminal Connections