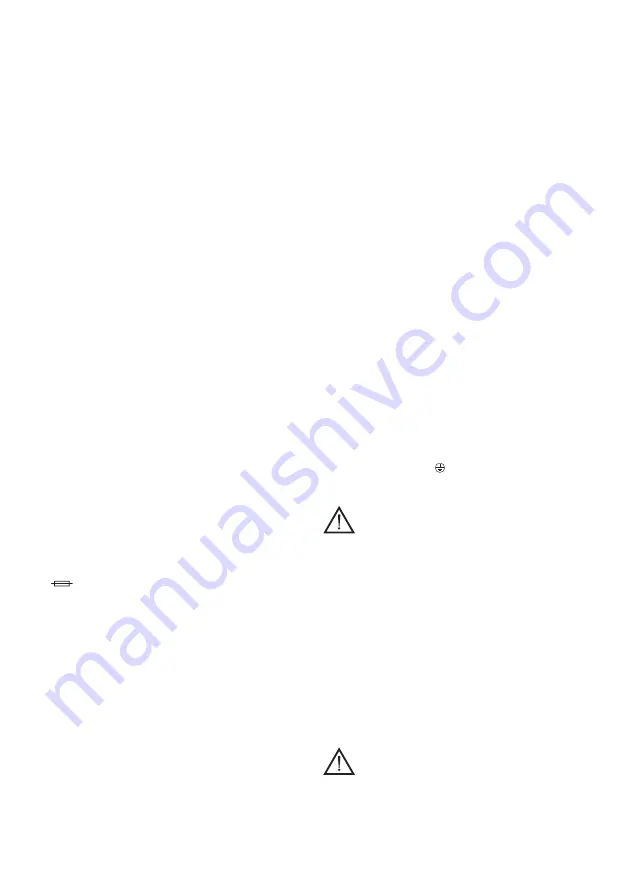
- 6 -
speed and precision of adjustment, give the welding machine excellent
welding quality.
Adjustment with the “inverter” system on the power line (primary) input
also determines a drastic reduction in volume both of the transformer and
the levelling reactance, allowing manufacture of a welding machine with
extremely contained volume and weight, enhancing its manageability
and movement.
STANDARD ACCESSORIES:
- Spot-welding cable with gun.
- Slotted washers kit (see updated catalogue)
3. TECHNICAL DATA
DATA PLATE
The most important data regarding use and performance of the welding
machine are summarised on the rating plate and have the following
meaning:
Fig. A
1-
Protection rating of the covering.
2-
Symbol for power supply line:
1~ : single phase alternating voltage;
3~ : three phase alternating voltage.
3-
Symbol
S
: indicates that welding operations may be carried out in
environments with heightened risk of electric shock (e.g. very close
to large metallic volumes).
4-
Symbol for welding procedure provided.
5-
Symbol for internal structure of the welding machine.
6-
EUROPEAN standard of reference, for safety and construction of arc
welding machines.
7-
Manufacturer’s serial number for welding machine identification
(indispensable for technical assistance, requesting spare parts,
discovering product origin).
8-
Performance of the welding circuit:
- U
0
:
maximum no-load voltage.
- I
2
/U
2
:
current and corresponding normalised voltage that the
welding machine can supply during welding
- X :
Duty cycle ratio: indicates the frequency with which the welding
machine can supply the corresponding current (same column). It
is expressed as a %, on the basis of a fixed welding time equal to
60ms (for example: 2% = 60ms / 3s *100 therefore corresponds to
a spot every three seconds).
If the usage factors (on the plate, referring to a 40°C environment)
are exceeded, the thermal safeguard will trigger (the welding
machine will remain in stand-by until its temperature returns
within the allowed limits).
- A/V-A/V :
shows the range of adjustment for the welding current
(minimum-maximum) at the corresponding arc voltage.
9-
Technical specifications for power supply line:
- U
1
:
Alternating voltage and power supply frequency of welding
machine (allowed limit ±10%):
- I
1 max
:
Maximum current absorbed by the line.
- I
1eff
:
effective current supplied.
10-
:
Size of delayed action fuses to be used to protect the power
line.
11-
Symbols referring to safety regulations, whose meaning is given in
chapter 1 “General safety considerations for arc welding”.
Note: The data plate shown above is an example to give the meaning
of the symbols and numbers; the exact values of technical data for the
welding machine in your possession must be checked directly on the data
plate of the welding machine itself.
OTHER TECHNICAL DATA
- WELDING MACHINE:
- see table 1
(TAB.1)
The weight of the welding machine is given in the table 1 (TAB.1)
4. DESCRIPTION OF THE WELDING MACHINE
The unit is comprised of power modules which have been developed on
a specially printed circuit designed to maximise reliability and reduce
maintainance.
Fig. B
1- Power supply input (1~) / (3~), rectifier group and balancing
capacitors.
2- Transistors and drivers switching bridge (IGBT).
It turns the mains rectified voltage into high frequency alternate
voltage and permits power regulation according to the current/
voltage of the weld to be done.
3- High frequency transformer: the primary windings are fed by the
voltage converted by Block 2, it has the function of adapting voltage
and current to the values required by the arc welding procedure and,
simultaneously, isolates the welding circuit from the mains.
4- Secondary rectifier bridge with inductance: this changes the
alternate voltage/current supplied by the secondary windings into
continuous current/voltage at a low wave-length.
5- Electronic and regulation board: this instantly checks the value of the
welding current against that selected by the user, it modulates the
commands of the IGBT drivers, which control Regulation. Determines
the dynamic response of the current while the electrode melts
(instantaneous short circuits), and supervises the safety systems.
CONTROL, ADJUSTMENT AND CONNECTION DEVICES
WELDING MACHINE
At the front:
Fig. C
1- Positive (+) fast coupling for connecting the welding cable.
2-
YELLOW LED:
normally open, when on it indicates an anomaly that
blocks the welding current for various reasons which can be:
- Thermal protection:
an excess temperature has been reached
inside the welding machine. The machine remains on without
supplying current until a normal temperature is reached. Reset is
automatic.
- Protection against short circuit of the electrodes:
automatically
blocks the welding machine, if the electrodes of the gun are
accidentally placed in short circuit for more than 30s (for example
resting the gun on the sheet metal).
- Protection against repeated welding on the same consumable
(washer/pin):
welding cannot be wrongly repeated on the same
consumable because machine control requires lifting the gun off
the just welded sheet metal.
3-
GREEN LED:
indicates the welding machine is connected to the
mains and is ready for operation.
4- Potentiometer for welding current adjustment with graduated scale
in Amperes.
5- Negative (-) quick coupling for connecting the welding cable;
6- 14 PIN connector to activate the welding gun.
At the back:
Fig. D
1- Power supply cable 2p +
(1~) with EEC plug where planned.
2- Main switch O/OFF - I/ON (light where planned).
5. INSTALLATION
WARNING! CARRY OUT ALL INSTALLATION OPERATIONS
AND ELECTRICAL CONNECTIONS WITH THE WELDING MACHINE
COMPLETELY SWITCHED OFF AND DISCONNECTED FROM THE
POWER SUPPLY OUTLET.
THE ELECTRICAL CONNECTIONS MUST BE MADE ONLY AND
EXCLUSIVELY BY AUTHORISED OR QUALIFIED PERSONNEL.
PREPARATION
Unpack the welding machine, assemble the separate parts contained in
the package.
HOW TO LIFT THE WELDING MACHINE
All the welding machines described in this handbook should be lifted
using the handle or strap supplied if provided for the particular model.
POSITION OF THE WELDING MACHINE
Choose the place to install the welding machine so that the cooling air
inlets and outlets are not obstructed (forced circulation by fan, if present);
at the same time make sure that conductive dusts, corrosive vapours,
humidity etc. will not be sucked into the machine.
Leave at least 250mm free space around the welding machine.
WARNING! Position the welding machine on a flat surface
with sufficient carrying capacity for its weight, to prevent it from
tipping or moving hazardously.
CONNECTION TO THE MAIN POWER SUPPLY
- Before making any electrical connection, make sure the rating data of
the welding machine correspond to the mains voltage and frequency
available at the place of installation.
Содержание 954677
Страница 81: ...81 6 G 1 H 7 IEC EN 60974 4 max 10 bar 8 ON...
Страница 84: ...84 6 G 1 H 7 IEC EN 60974 4 10 8 ON...
Страница 85: ...85 A V A V 6 4 5 9 8 7 FUSE T A 11 10 5 1 2 3 4 POWER MODULE CONTROL MODULE 230V 50 60Hz FIG A FIG B...
Страница 86: ...86 FIG C FIG D 1 5 6 2 3 4 1 2...
Страница 87: ...87 FIG E FIG F 1 2 2mm 1 2 2mm 3 4...
Страница 88: ...88 FIG G FIG H 1 2...