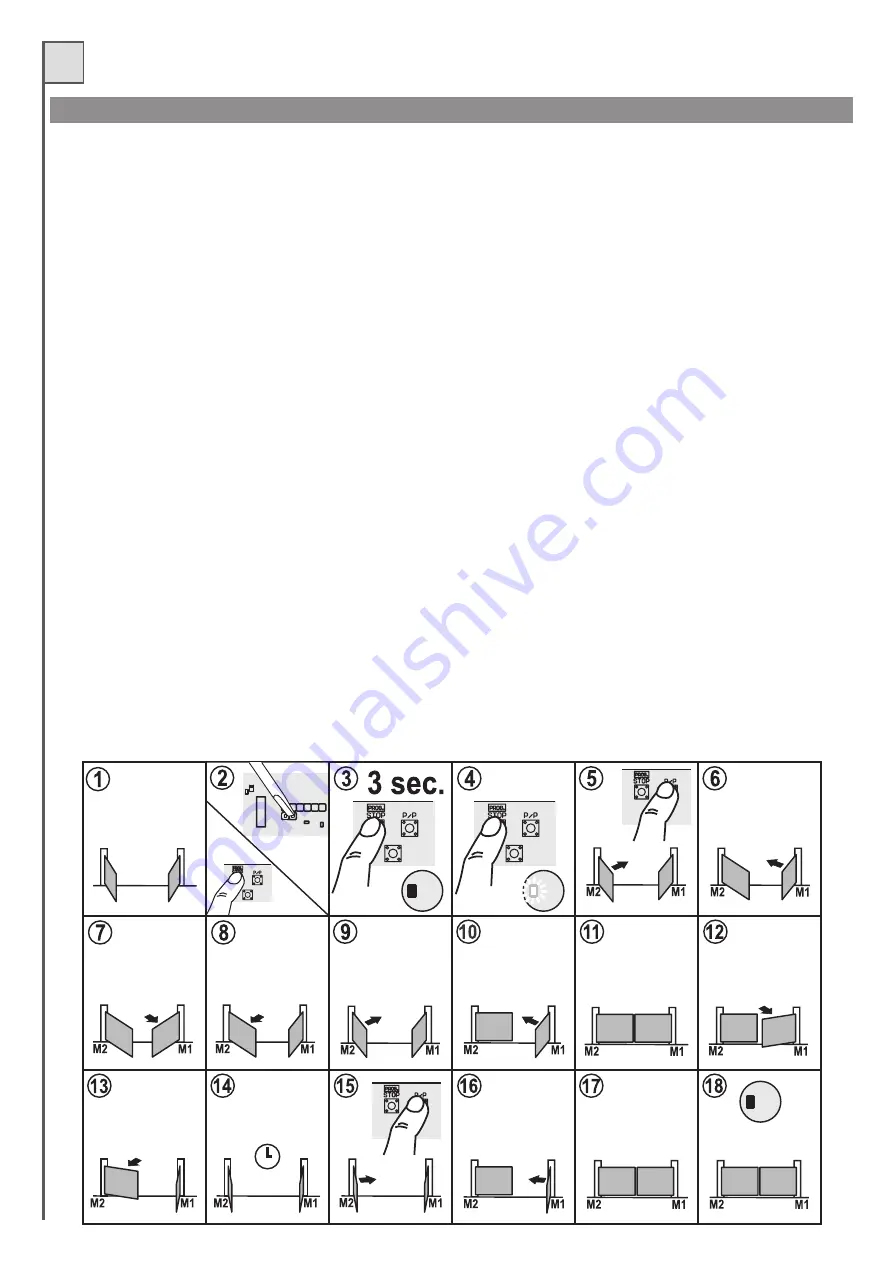
GB
44
AUTOMATIC PROGRAMMING (simplified)
Procedure:
1 - Position the leafs (or single leaf) in the nearly open position: the leafs must be positioned with enough space to move for approx. 5 seconds in closing
mode. If the leafs are not in position the procedure described in the paragraph above can be used.
2- Press and hold Prog to reset, and use a screwdriver to short the jump Reset (detail 20 of fig. 1).
3- Keep the Prog key pressed.
4-After three seconds led LD3 (and the flashing light) turns on. Programming procedure activated
5- Press the S/S button to start the self-learning process. Leaf M2 starts on closing for 3-5 sec (approx.) and then stops
6- Leaf M1 performs the same movement immediately afterwards.
7- Leaf M1 starts on opening for 3-5 sec and then stops
8- Leaf 2 performs the same movement immediately afterwards (opens for 3-5 sec and then stops).
9- Leaf with M2 closes completely
10- M1 also closes
11-12- When both leafs are closed, M1 is started up automatically in opening.
13- When M1 is open M2 also opens completely.
14- When the two leafs are both in the open position, the pause time memorisation phase is started.
15- Once the required pause interval has elapsed, press the S/S button and motor M2 starts closing.
16- When M2 reaches the end stop, M1 closes.
17- Gate completely closed
18- End of programming (the control unit sets automatically to normal operating mode).
MPORTANT: in this movement the leafs must not come into contact with the end stop; if this occurs repeat the self-learning procedure
(positioning the gate leafs so that they can close for 5 seconds without coming into contact with the end stop).
IMPORTANT: also during this movement the leafs must not come into contact with the end stop; if this occurs, correct positioning and
repeat the self-learning procedure. At this point the control unit has read all parameters of the two leafs (encoder presence/absence and
relative speed, current on motors).
- During this manoeuvre, the control unit detects the presence of the encoders on the motors: IT IS NOTADMITTED to have one motor with
an encoder and the other without; if this occurs (for example due to an encoder fault on one of the motors) the control unit emits an error
signal of ten flashes of the led LD3 and indicator light.
- Correct detection of encoder presence can be verified by checking the motor operation leds (detail 9 and 21 of Fig. 1), if the led related to
the motor running is flashing, this means that the relative encoder has been detected.
If the led remains permanently lit the encoder has not been detected.
- If the control unit does not detect encoders on either motor, obstacle detection can be checked by monitoring current during operation.
- The memorised values remain stored until a new programming cycle is performed.
- This simplified programming procedure automatically sets the leaf delay value and the deceleration points using the default settings.
- Should these settings prove unsuitable for the specific installation, the advanced programming procedure should be followed, as
described in the next section.
P3
P3
P3
LD3
LD3
Reset
P3
P3
LD3
PAUSE
Time
End
Содержание T224
Страница 11: ...TAB 2 I 11...
Страница 23: ...F 23 TAB 2...
Страница 35: ...E 35 TAB 2...
Страница 47: ...GB 47 TAB 2...
Страница 59: ...D 59 TAB 2...
Страница 71: ...NL 71 NL TAB 2...
Страница 74: ...NOTE 74...
Страница 75: ...75...