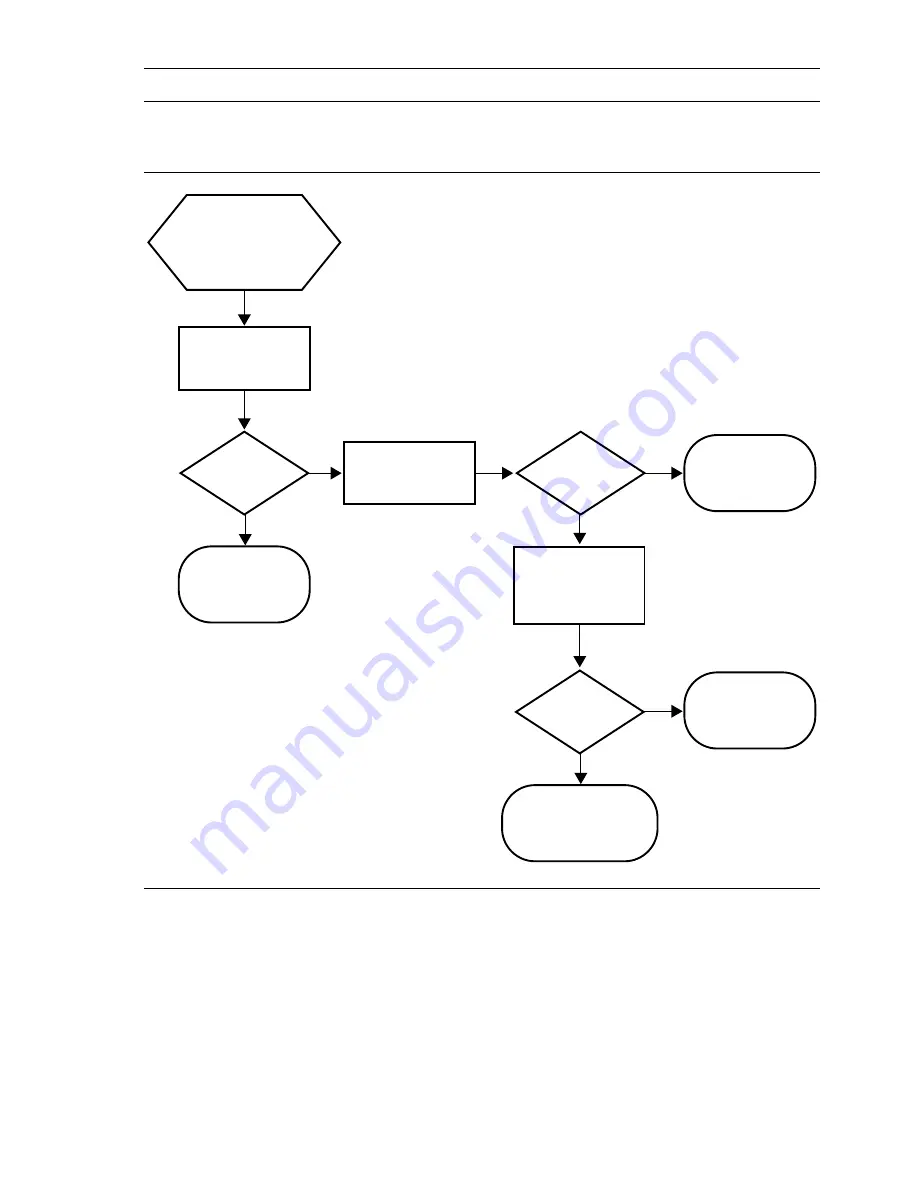
Service Guide
37
7,004.46:
PM_FAULT_DM_CAM_
SENSOR_BAD
The drum-maintenance cam sensor did not see the
sensor’s interrupt flag as expected. The sensor may be
failing or the drum-maintenance cam may be jammed.
Table 4 Front panel and fault history log error codes and messages
Error code
Meaning
7,004.46
Maintenance blade position
sensor (right I/O board) failed
to detect transitions of the
drum-maintenance
home flag
Observe drum-
maintenance home
flag motion while
turning on the printer
Does flag
rotate during power
on sequence?
Check operation of the
compound gear, belt,
and drive train
Does process
gear train rotate
smoothly?
Replace or reseat
gears; replace or
retension belt
Remove maintenance
drawer and inspect
drum-maintenance cam,
bushings, and
cam lifters
All parts
installed
correctly?
Replace (in this order):
• drum-maintenance clutch
• I/O board
• Power control board
Reinstall or
reseat the parts
Replace I/O
right board
No
No
No
Yes
Yes
Yes
0388-83
Содержание Phaser 840
Страница 11: ...xii Phaser 840 and 850 Color Printers ...
Страница 65: ...54 Phaser 840 and 850 Color Printers ...
Страница 101: ...90 Phaser 840 and 850 Color Printers ...
Страница 125: ...114 Phaser 840 and 850 Color Printers ...
Страница 134: ...Service Guide 123 Clearing PostScript NVRAM menu item ...
Страница 135: ...124 Phaser 840 and 850 Color Printers ...
Страница 166: ...Service Guide 155 Figure 1 Cabinet FRUs 7 5 6 8 1 2 4 0388 21 3 9 9 ...
Страница 168: ...Service Guide 157 Figure 2 Imaging FRUs 4 2 3 6 5 7 8 11 9 13 15 17 16 12 14 1 2 0388 79 18 10 19 ...
Страница 170: ...Service Guide 159 Figure 3 Paper path FRUs 0388 80 2 1 5 11 10 9 12 6 4 3 7 13 8 11a 11b ...
Страница 172: ...Service Guide 161 Figure 4 Motor and fan FRUs 0388 14 7 4 3 5 6 2 1 ...
Страница 174: ...Service Guide 163 Figure 5 Circuit board FRUs 4 3 5 2 1 9 7 6 8 10 11 13 0388 81 12 7a ...
Страница 176: ...Service Guide 165 Figure 6 Solenoid and clutch FRUs 4 5 3 2 1 0388 23 ...
Страница 178: ...Service Guide 167 Figure 7 Gear and belt FRUs 0388 22 9 7 3 4 2 13 15 11 5 10 6 14 12 16 17 18 19 1 8 ...
Страница 180: ...Service Guide 169 Figure 8 Sensor and flag FRUs 0388 15 7 3 2 1 4 5 9 8 10 16 12 17 14 18 19 6 11 13 15 ...
Страница 182: ...Service Guide 171 Figure 9 High capacity PaperTray 0388 65a 1 2 ...
Страница 201: ...190 Phaser 840 and 850 Color Printers ...