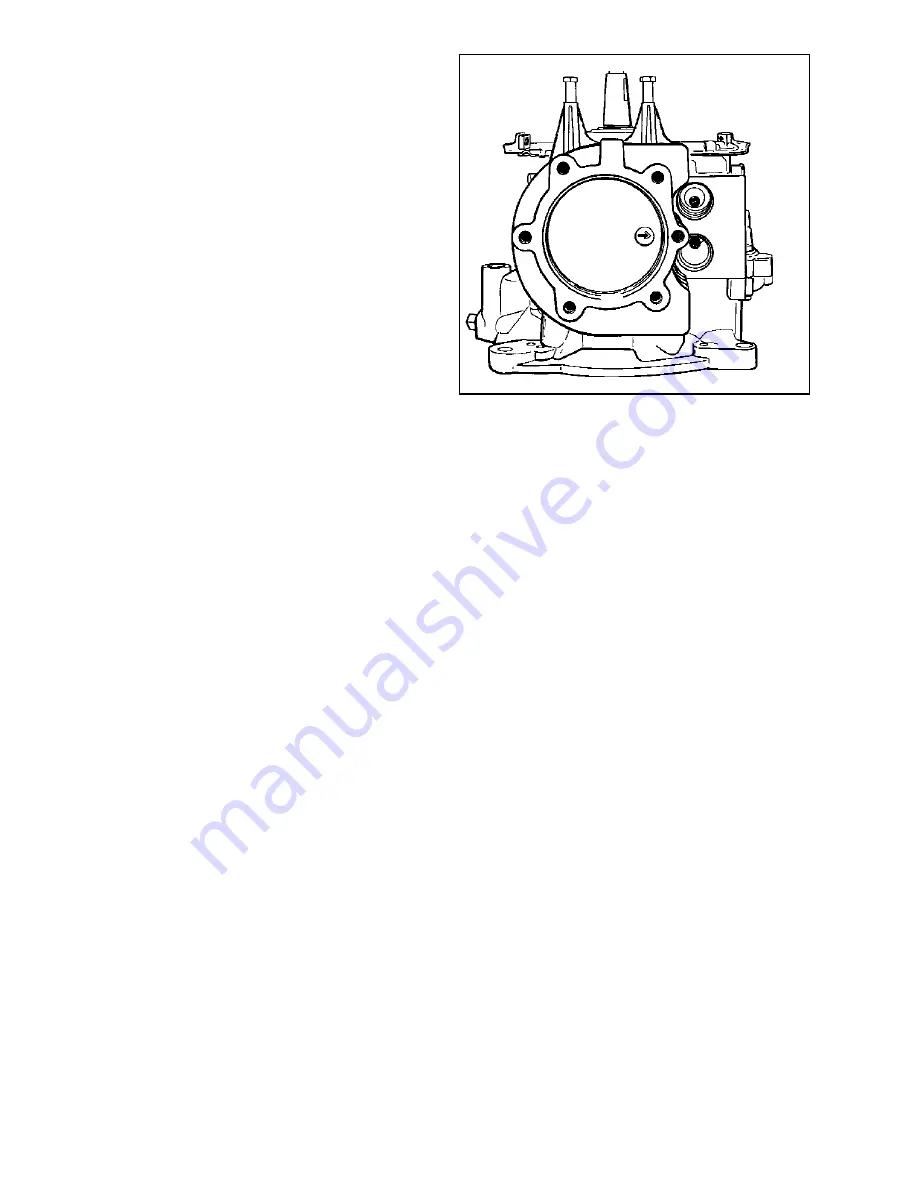
68
CYLINDERS
Visually check the cylinder for broken or cracked fins
or a scored cylinder bore. Check the main bearing for
wear or scoring. If the main bearing is worn or scored
it can be replaced on some models. See "Crankshaft
Bearing Service" in this chapter.
Use a dial bore gauge or transfer gauge with a
micrometer to accurately measure the cylinder bore.
Measure in the piston travel area approximately 1/2"
to 3/4" (12.7-19.05 mm) from the top and the bottom
. Measure at 90 degrees to the piston pin, 45 degrees
to the piston pin, and even with the piston pin as the
piston would appear when assembled. A rigid hone is
recommended to "true" any cylinder irregularities. If
the cylinder bore is worn more than .005" (.127 mm)
oversize, out of round or scored, it should be replaced
or re-sized to .010" or .020" (.254-.508 mm) oversize.
In some cases engines are built with oversize
cylinders. If the cylinder is oversize, the oversize value
will be imprinted in the top of the cylinder (diag. 22).
To recondition a cylinder, use a commercially available hone of the proper size . Chuck the hone in a drill press
with a spindle speed of about 600 R.P.M. Tecumseh recommends 380 grit for finish in a standard cross hatch.
Start with coarse stones and center the cylinder under the drill press spindle. Lower the hone so the lower end
of the stones contacts the lowest point in the cylinder bore.
Rotate the adjusting nut so that the stones touch the cylinder wall and begin honing at the bottom of the
cylinder. A light honing oil should be used to lubricate and cool while honing. Move the hone up and down at a
rate of 50 strokes per minute to avoid putting ridges in the cylinder wall. Every fourth or fifth stroke, move the
hone far enough to extend the stones one inch beyond the top and bottom of the cylinder bore.
Check the bore diameter every twenty or thirty strokes for size and a 35
0
- 45
0
crosshatch pattern. If the stones
collect metal, clean the stones with a wire brush when the hone is removed.
If cylinder oversizing is needed we recommend boring the cylinder. This service is offered by many Service
Dealers. You also may wish to contact a local machine shop.
Clean the cylinder and crankcase with warm, soapy water, rinse with clean water, and dry thoroughly. Continue
the cleaning procedure until a clean white cloth wiped on any internal surface reveals no honing residue or dirt.
Replace the piston and the piston rings with the correct oversize parts as indicated in the parts manual.
.010
.010
22