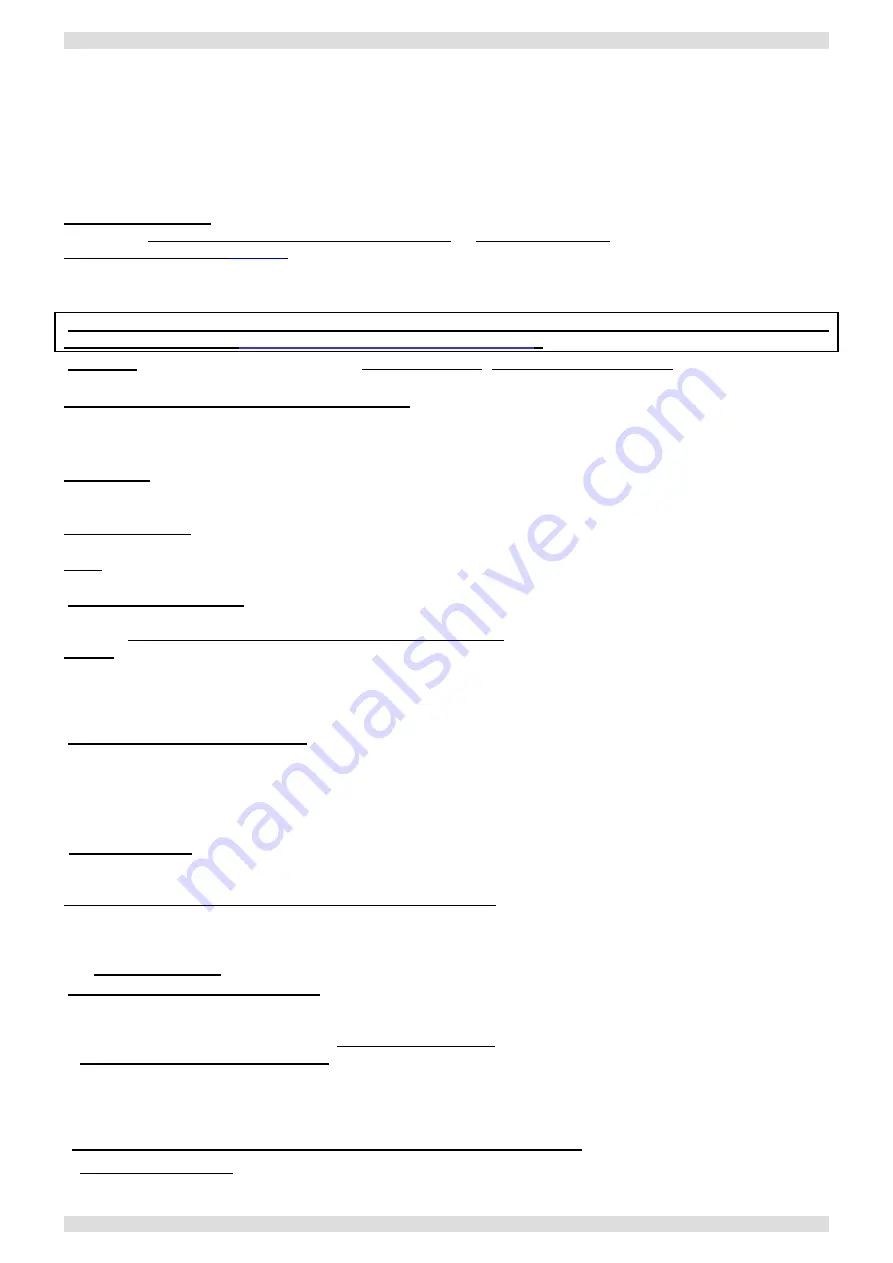
IST-2282.EO01.01
Istruzione / User’s Manual / Manuel d’utilisation
Pag.5/9
TECNOCONTROL S.r.l. Via Miglioli 47 SEGRATE ( MI )
Tel. +39 02 26922890 - Fax +39 02 2133734
tion in Air”
then disconnect and connect the unit, finally try to replace a new
“Cartridge Sensor
”. If the condition is
not change, it will be necessary to replace the unit and/or send it back to the supplier to repair.
Only with Red set-up “activate” all LED activates (
>24 mA output signal
):
this happens when the “
Cartridge
Sensor
” is not working or gas concentration is out of scale (higher than 30%v/v O
2
) If there are not any gas leaks
and the condition is not change, it will be necessary to replace the unit and/or send it back to the supplier to repair.
INSTALLATION
The detector must be accurately installed according to the national dispositions in force on the safety of the plants
and installation of electric devices.
Detector positioning
:
The
Fig.2
shows the instrument size. The unit must be positioned vertically with the sensor
downwards.
It should be fixed at 1.60 m from the floor (the O
2
gas is lighter as air).
Electrical Connection
(
see Fig.2
)
: the maximum distance to install each detector from the Central Unit is show in
the
Table 1
. Normally use a tree wire shielded cable.
The terminals
(+ - S
), are plug-in type, it is necessary to extract them to make the connection. Pay attention when
you insert them again, being polarized.
Note: Dip-Switch should be set with instrument powered off. Dip-Switch 1 settled ON activates ALARM Led
indication (see Table 2) (
see also Operational Description > Faults
).
Important:
Once installation is completed,
power up the unit, wait about
20÷30 minutes
and then to adjust the
sensor to the environment,
only if it is necessary
,
carry out the
Calibration in Air
(
see
Test and Calibration
).
COMPATIBILITY WITH OTHER CENTRAL UNITS: In case of a central unit other than Tecnocontrol,
please
verify the max load resistor as shown in
Fig.4
.
The max load resistor is 50 ohm with 12Vdc power supply, while is
400 ohm with 24Vdc power supply.
We suggest using 24Vdc power supply.
WARNING
Average life
: The sensitive element used in this detector has an excellent stability in time. In fresh air and in nor-
mal working condition the
sensor's life is
about 2 years
. After this period the yellow LED “
FAULT
” flashes every 4
seconds, is necessary replacing the “
Cartridge Sensor
”.
Periodical testing
: we advise to carry out working tests every 6 or 12 months as explained on page 4 chapter
“
Tests and Calibration
”.
Note:
the detector is not able to detect Oxygen gas occurring outside the room where it is installed, either inside
walls or under the floor.
Sensor operating limits:
the electro-chemical cell, in any case, should not be exposed to temperatures lower
than -40° or higher than 60°C. The electrochemical cell should not be exposed to an over-range concentration of
30 % O
2
. If this condition occurs, we suggest replacing the sensor.
Safety:
Oxygen sensors contain a small quantity potassium acetate solution which is corrosive. Normally this mate-
rial would only leak out as a result of either mechanical damage or an incorrect instrument use beyond the limits of
its operational functioning. These sensors also contain small amounts of lead, lead oxide, platinum, silver, carbon
and antimony. If the user comes into contact with the oxygen sensor contents the affected area should be washed
with a copious supply of water.
Cross sensitivity to other gases:
The electrochemical cell employed has a good resistance towards products
such as sprays, detergents, ammonia, glues and paints.
However, in case of products containing substances in
great quantity, these could interfere with the Sensor and cause false alarms.
We recommend ventilating the room
when products like these are used. Volatile organic solvents in great quantity cause false alarms, and then the cell
needs one or more hours in clean air to recover the normal sensitivity conditions.
TEST and CALIBRATION
PAY ATTENTION
:
This procedure has to be made with extreme attention and by authorized and trained
people; because starting this procedure it will increase mA Output causing the activation of connected
alarm devices to the gas Central Unit.
Operation Check, Calibration in Air and Fine mA ADJ Output
:
are different code protected functions. To access
these functions is necessary to insert the relevant “
Code
" through the keys F1s and F2. To have the key pressure
recognized, hold pressing it for around a second (
until the Green Led doesn't switch off for a moment
). Then the next key
can be pressed. In case of error all it takes is waiting around 10 seconds and the sequence is automatically erased.
The
Calibration Check
is a function code free.
Calibration Kit, Sample Gas Bottles
(
for Calibration Check
) please, using a mixture:
about 16%v/v Oxygen (O
2
) in Nitrogen
It is possible to use either the disposable cylinders with adjust valve or the high pressure ones with reduction gear.
It is necessary to use
the calibration kit
Tecnocontrol model TC011
(
for non-corrosive gases
)
or TC014 (
Stainless steel
).
“INSTRUMENT OPERATION CHECK” (
Check Code
: F2, F2, F1, F1)
:
this function allows to effect a functional test
of the equipment. After having put the system in safety and inserted the "
Code Test
", all Led are switched off. Then
they will switch on in sequence, the Led, from the yellow up to the red. At the end all the Led will remain lighted for
around 5 seconds, then the central returns at the conditions of normal operation. It is advisable to perform this op-
eration every 6-12 months according to the use.
Note: this function is not working if the red Led have already turned on.
“CALIBRATION IN AIR” (
Calibration Code
: F2, F2, F2, F1, F2, F1)
:
this function allows completely recalibrate the
sensor at 20.9%v/v in air. This procedure when it is launched will automatically until the end.