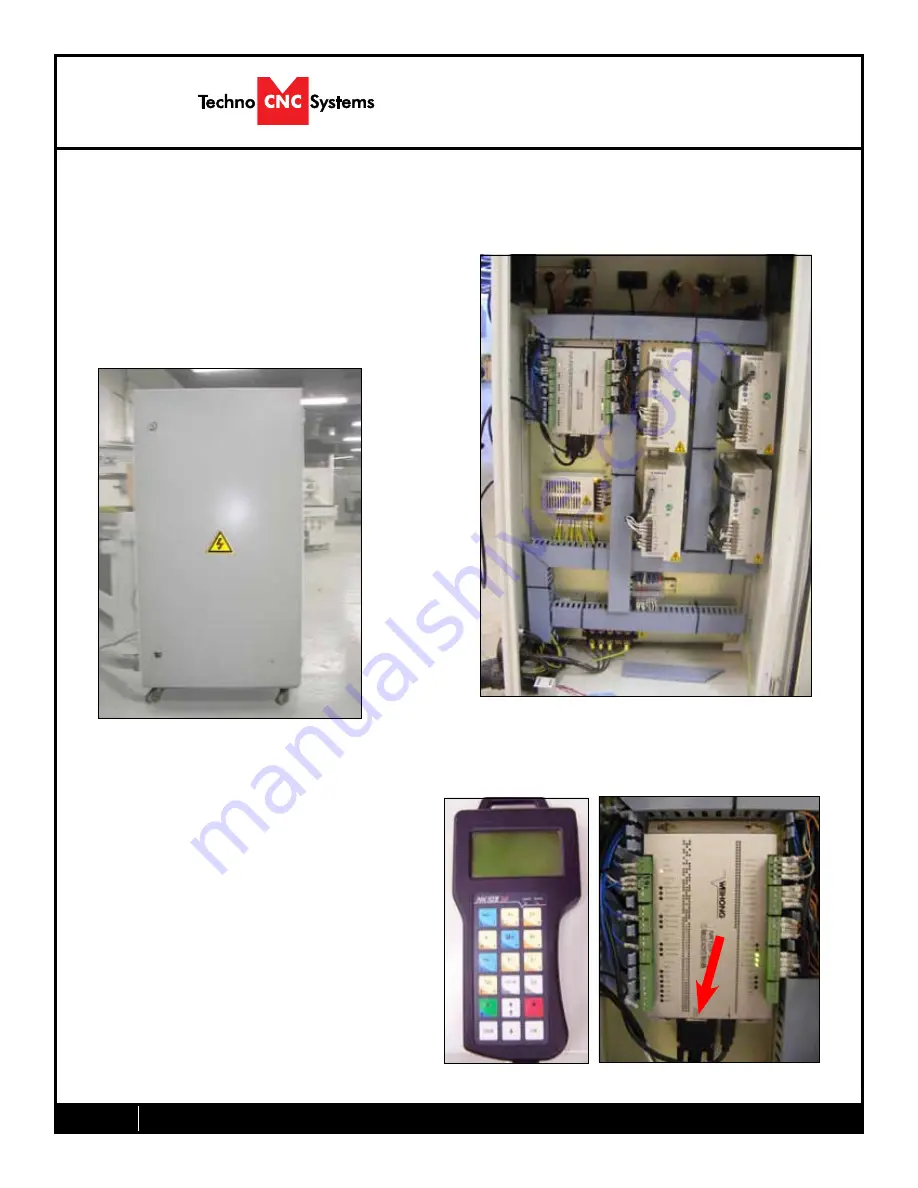
10
Call: 1-631-648-7481 or Visit: support.technocnc.com
HD Series Manual
NK105G2
1.3
Take the black connector coming from the Hand-
held controller (fig 1.3a,) and guide it through
the hole in the side of the box.
Locate the controller board (fig 1.3b) and attach
the block connector as shown by the red arrow.
Fig. 1.3a
Fig. 1.3b
I.2
Open the back of the controller box (shown in Fig 1.2a) with the key provided. The
electronics will now be exposed and components identified in Fig 1.2b.
Fig. 1.2a
Fig. 1.2b
A
B
A- Controller Board.
B- 24Volt PSU.
C- Stepper Driver.
D- 220Volt In.
D
C