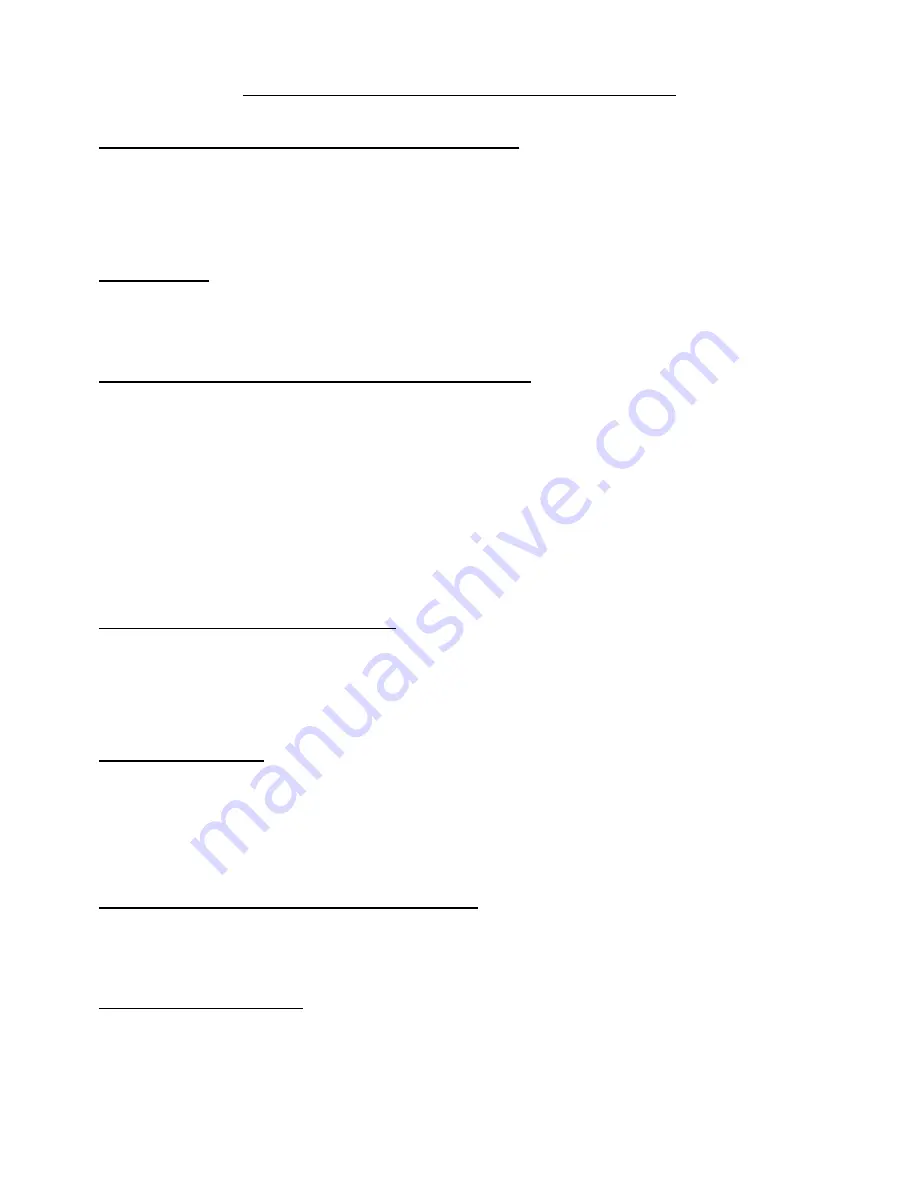
19
USING THE DIGITAL PANEL
1. Setting welding parameters
Set welding parameters using the
“FUNCTION”
(2) keys. For each function selected, the present value appears on
the
DISPLAY (7)
and the LED of the corresponding icon turns on.
Press
“ENTER”:
the measurement symbol flashes. Set the new value with the “
+
” and “
-
“ touch buttons.
Press
“ENTER”
to confirm and move on to the next function with the “
+
” button.
The
KNOB (3)
rules over the maximum current output.
2. Pulse
With the
PULSE
function selected, the display prompts for
ON/OFF
; select the desired mode with the
“ENTER”
button. In the ON mode, the pulsing
DUTY CYCLE
can be varied between
30%
and
80%
, and the frequency
between
1
and
175Hz
. Maximum current output is set with the
Knob (3)
, meanwhile the minimum is the
“BASE”
.
3. Choice of welding procedure
Once programming is ended, 6 different procedures can be selected:
STICK (ELECTRODE)
STICK + ARC FORCE (ELECTRODE WITH OVERCURRENT)
TIG 2T HF (TIG WELDING IN 2 STEP WITH HF)
TIG 4T HF (TIG WELDING IN 4 STEP WITH HF)
TIG 2T NO HF (TIG WELDING IN 2 STEP WITHOUT HF)
TIG 4T NO HF (TIG WELDING IN 4 STEP WITHOUT HF).
The procedure selected appears on the display and the LED of the corresponding icon turns on.
Begin welding. The
“PREVIEW”
display changes to
“WELDING”
and the current shown is what is actually output*.
* In TIG PULSE, the display shows “PREVIEW” and the ammeter shows the maximum current set.
4. Program memories
When there are several, repetitive welding jobs to be done, or different operators are doing jobs with the same
machine, the group of parameters used can be saved in the memory, then called up at any time.
ENTERING DATA IN THE MEMORY:
Set the welding parameters as shown in
(1) above
.
Press the
“MEM, R”
(READ MEMORY) button; select a number from 2 to 18 with the
+
and
–
buttons.
Press the
“MEM, W”
(WRITE MEMORY) button.
READING THE MEMORY
Welding programs that are memorised can easily be called up.
Press the
“MEM, R”
(READ MEMORY) button; the display will show a number from 1 to 18.
Change the number, if necessary, with the
+
and
–
buttons.
Press the
“MEM, R”
button again, to confirm the selection.
If any of the parameters value is changed while a memory is being used, by the next welding session these will
automatically replace the preceding ones.
5. Remote and Foot control
Once the
REMOTE CONTROL
(or
Foot Control
) is connected to the socket
(6)
, output current regulation will be
automatically transferred from the
KNOB
(3)
to these controls.
WARNING:
For remote or foot control operation, the
SLOPE-UP
and
SLOPE-DOWN
times must be set to zero (
0)
6. Overheating
Particularly high environment temperatures, when combined with heavy-duty machine jobs, may cause the word
“OVERLOAD”
appearing on the display; this means that the generator has been overheated.
At the end of the cooling cycle, the indicator automatically returns to
“PREVIEW”
.
Содержание Ergus WIG 160 CDI
Страница 1: ...MANU 115 M TIG 00 INDUSTRIE LINE WIG 160 DCi CDI WIG 201 DCi CDI USER MANUAL...
Страница 23: ...23 BLOCK DIAGRAM WIG 160 DCi...
Страница 24: ...24 WIG 160 CDI...
Страница 25: ...25 WIG 201 DCi...
Страница 26: ...26 WIG 201 CDI...
Страница 27: ...27 REMOTE CONTROL CONNECTION DIAGRAM WIRING OF CONNECTORS...
Страница 29: ...29 WIG 160 DCi...
Страница 31: ...31 WIG 160 CDI...
Страница 33: ...33 WIG 201 DCi...
Страница 35: ...35 WIG 201 CDI...