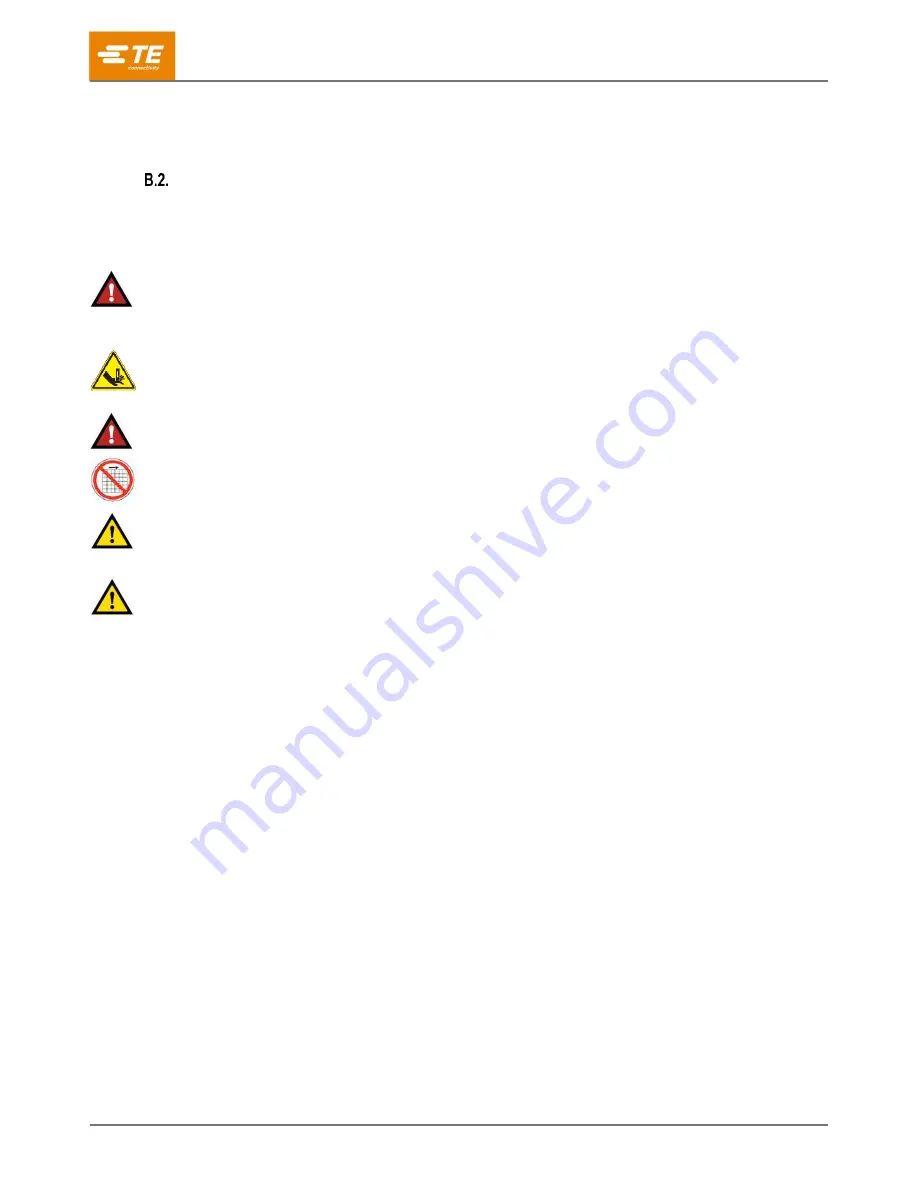
408-10390
Rev
T
16
of 25
h. Cycle the machine back to top-dead-center, causing the feed to shift forward and feeding the
terminal over the anvil.
i.
Repeat substeps d through h until the terminal is centered over the slug blade.
Adjusting the feed speed
The feed mechanism has been adjusted at the factory to ensure that the terminal is advanced at the
lowest possible speed. It requires readjustment
only
in exceptional circumstances. On rare occasions,
the feed speed is not fast enough if the applicator is used on a fully automatic machine. The feed
speed can be adjusted by means of the two exhaust restrictors.
DANGER
To avoid personal injury, do not connect the pressurized air supply until
after
the applicator is properly installed in the
terminating machine. When the machine is manually cycled, the mechanism moves forward and backward once during each
machine stroke, unless the air is disconnected.
DANGER
Moving parts can crush and cut. Never insert hands into installed equipment.
DANGER
Do not wear jewelry, loose clothing, or long hair that can catch in moving parts of the equipment.
DANGER
Do not operate the equipment without guards in place.
CAUTION
The detent screws on feed adjustments (see Figure 3) are set up properly by the factory. Tampering with them causes
damage.
CAUTION
Excessive feed or retract speeds can cause inconsistent feeds or air feed module damage.
To adjust the air feed speed, complete the following steps.
1. Open the exhaust restrictors or forward speed control and retract speed control (Figure 3) to increase
the feed speed.
2. Loosen the locking ring.
3. Adjust the speed by turning the adjustment screw.
Turn the screw clockwise to decrease the speed.
Turn the screw counter-clockwise to increase the speed.
4. Tighten the locking ring.