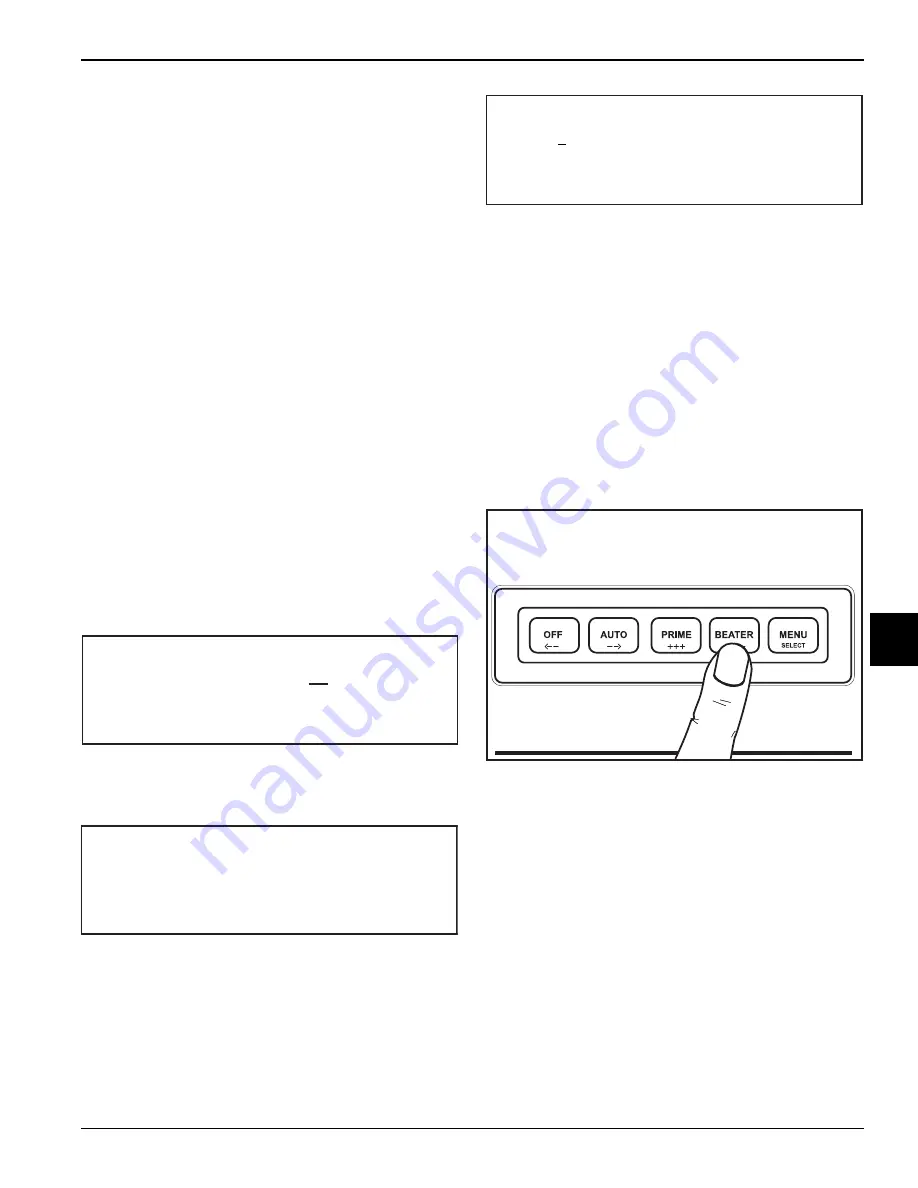
OPERATING PROCEDURES
6-11
Model C303 & C314
Operating Procedures
6
5.
Allow the rinse water to flow into the cylinder
until it is approximately 2/3 full. With a pail under
the door spout, open the draw valve and drain
the rinse water.
Repeat this procedure
until the
rinse water being drawn is clear
6.
Repeat step 1 through step 5 for the remaining
freezing cylinder.
7.
When draining is complete, press the OFF (<- -) key.
Cleaning
1.
Prepare an approved 100 PPM cleaning solution.
(examples: 2-1/2 gal. [9.5 liters] Kay-5
®
or 2 gal. [7.6
liters] Stera- Sheen
®
). Use warm water and follow the
manufacturer's specifications.
Important!
Make sure the cleaner is completely
dissolved.
2.
Pour the cleaning/sanitizing solution into a clean,
empty pail. Place the syrup line with the old syrup
connector into the pail of cleaner.
3.
To place a freezing cylinder in the SANITIZE mode,
press the MENU SELECT key. Move the cursor by
pressing the AUTO (- ->) key until the third line
indicates RINSE / SANITIZE.
4.
Press the MENU SELECT key. Move the cursor
under the word "SANITIZE" by pressing the OFF (<- -
) key.
5.
Pressing the MENU SELECT key will give you the
option for sanitizing a freezing cylinder. Move the
cursor under the desired barrel.
6. Press the MENU SELECT key to start the sanitize
mode.
7. Repeat step 3 through step 6 for the remaining
freezing cylinder.
8. Open the prime plugs. Allow each cylinder to fill
approximately 2/3 full. Close each prime plug.
9. Continue filling the freezing cylinders with sanitizing
solution until the solution purges out of each relief
valve and begins draining into the front drip tray. The
relief valves are located at the top of each mix tank.
Press the OFF (<- -) key.
10. Press the BEATER (- - -) key to agitate the solution in
each freezing cylinder for five minutes.
Figure 6-40
11. With a pail beneath the door spouts, open the draw
valves and drain all the solution from the freezing
cylinders. Press the OFF (<- -) key and close the
draw valves.
OPERATOR MENU
A B C D E F G H I
RINSE / SANITIZE
L
E
S
>
-
-
-
-
<
RINSE / SANITIZE
RINSE
SANITIZE
EXIT
- - - - -
L
E
S
>
-
-
-
-
<
SEL
<- - - ->
EXIT
BRL 1
2
3
SANITIZE
13040
Содержание C303
Страница 14: ...3 4 SAFETY Model C303 C314 Safety 3 Notes...
Страница 41: ...OPERATING PROCEDURES 6 13 Model C303 C314 Operating Procedures 6...
Страница 43: ...7 2 OPERATOR CHECKLIST Model C303 C314 Operator Checklist 7 Notes...
Страница 47: ...9 2 PARTS REPLACEMENT SCHEDULE Model C303 C314 Parts Replacement Schedule 9 Notes...
Страница 53: ...11 4 LIMITED WARRANTY ON PARTS Model C303 C314 Limited Warranty on Parts 11 Notes...