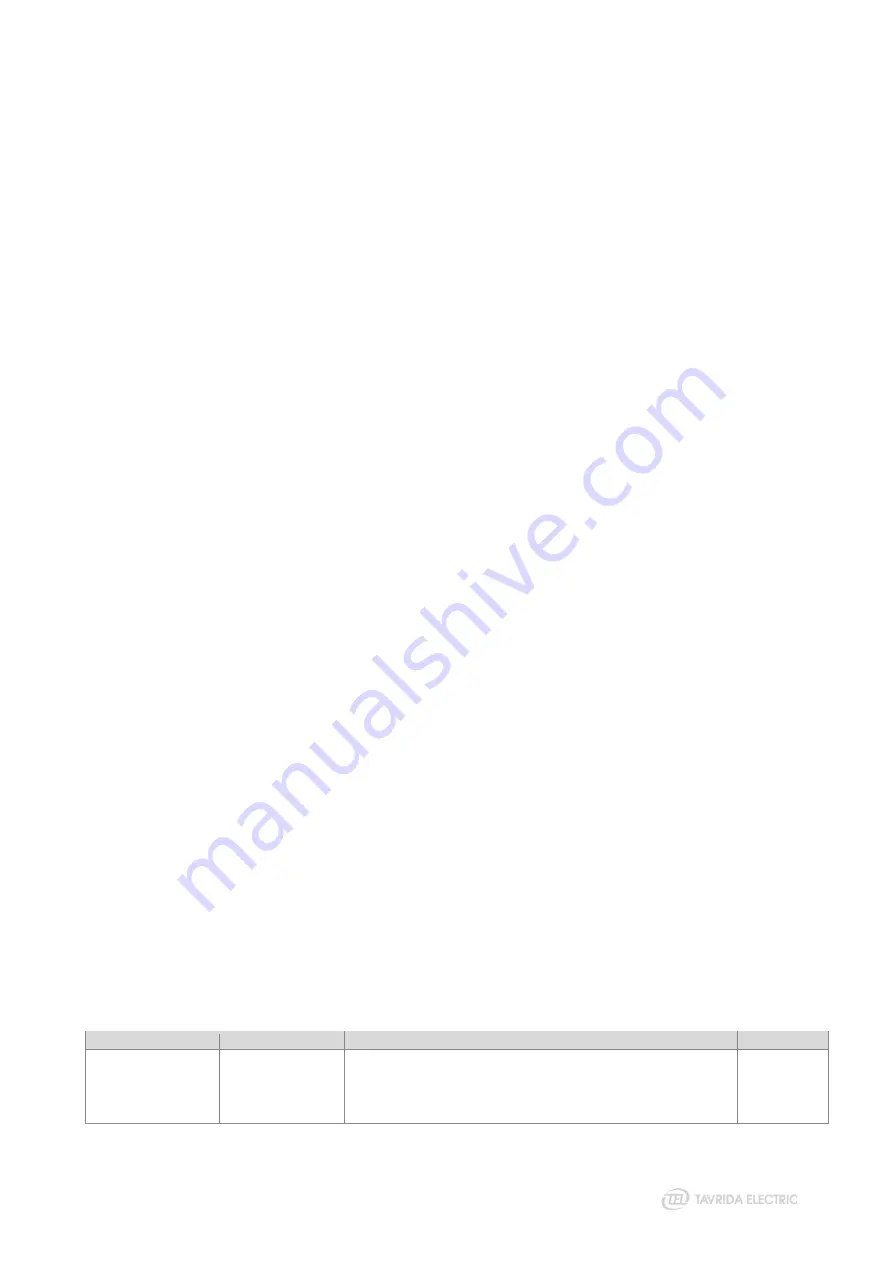
31
OC protection consists of six (6) individual overcurrent elements providing three stages of protection for both
the Forward () and Reverse (Source-) power flow directions: OC1+, OC1-, OC2+, OC2-, OC3+, OC3-
.
OC1
Phase overcurrent low set element OC1 is designated to provide time delayed trips. It is enabled in any
selected sequence in t
he Overcurrent Reclosing element. „I“ (Instantaneous) stands for accelerated and „D“
(Delayed) for delayed step of overcurrent protection in an autoreclosing sequence.
OC2
Phase overcurrent low set element OC2 is designated to provide accelerated trips. If a sequence step in the
Overcurrent Reclosing Element is set „D“ OC2 element is disabled. If a sequence step in the Overcurrent
Reclosing element is set „I“ OC2 element is enabled.
OC3
Phase fault high set instantaneous element provides protection against phase high current faults with a
reduced number of trips to lockout. If there is no intention to reduce the number of trips to lockout at high
current faults, enabling this element is not recommended. OC1 and OC2 allow reduction of tripping time to any
desired value at high currents.
For details on available TCC refer to Table 20 of this guide.
OC3 element settings are described in Table 21.
Earth Fault (EF)
This element is available
for OCR mode “Recloser” only.
This element provides protection against single phase and double phase earth faults.
EF protection consist of six (6) individual overcurrent protection elements providing three stages of protection
for both the Direct () and Reverse power flow (Source-) directions: EF1+, EF1-, EF2+, EF2-, EF3+,
EF3-.
EF1
Earth fault low set element EF1 is designated to provide time delayed trips. It is enabled in any selected
sequence in the Overcurrent Reclosing element. „I“ (Instantaneous) stands for accelerated and „D“ (Delayed)
for delayed step of overcurrent protection in an autoreclosing sequence.
EF2
Earth fault low set element EF2 is designated to provide accelerated trips. If a sequence step in the Overcurrent
Reclosing Element
is set „D“ EF2 element is disabled. If the sequence step in the Overcurrent Reclosing
element is set „I“ EF2 element is enabled.
EF3
Earth fault high set instantaneous element provides protection against high earth current faults with a reduced
number of trips to lockout. If there is no intention to reduce the number of trips to lockout at high current faults,
enabling this element is not recommended. EF1 and EF2 allow reduction of tripping time to any desired value
at high currents.
For details on available TCC refer to Table 17 of this guide.
EF3 element settings are described in Table 18.
Table 17
– TCC types
Settings
Designation
Range
Default
Type of time current
characteristic
TCC
ANSI: Extremely Inverse (EI), Moderately Inverse (MI), Very Inverse (VI)
IEC: Extremely Inverse (EI), Very Inverse (VI), Inverse (I)
Definite Time (TD)
Custom: custom curves are available on request. Contact Tavrida
Electric representative.
TD
Содержание Rec15
Страница 1: ......
Страница 5: ...1 Introduction...
Страница 9: ...2 Technical Parameters...
Страница 14: ...3 Product Description...
Страница 26: ...26 Figure 25 Anti vandal housing...
Страница 27: ...4 Functionality...
Страница 56: ...5 Product Handling...
Страница 69: ...6 Installation...
Страница 81: ...7 Commissioning...
Страница 84: ...8 Operation...
Страница 99: ...99 Figure 76 Settings uploading wizard...
Страница 100: ...9 Maintenance and Troubleshooting...
Страница 114: ...114 Figure 90 Securing the trip hook shaft against rotation...
Страница 115: ...10 Product Coding...
Страница 122: ...11 Appendices...
Страница 128: ...128 Appendix 4 Recloser Control Drawings Figure 99 Dimensions of RC5_4...
Страница 131: ...131 Figure 103 Dimensions of substation recloser package Figure 104 Placement of substation recloser components in a box...
Страница 133: ...133 Figure 106 Dimensions of standard OSM mounting kit arrangement for lateral installation...
Страница 134: ...134 Figure 107 Dimensions of interface bracket...
Страница 135: ...135 Figure 108 Dimensions of OSM mounting kit with M16 pole interface front installation...
Страница 136: ...136 Figure 109 Dimensions of OSM mounting kit with M16 pole interface lateral installation...
Страница 137: ...137 Figure 110 Dimensions of OSM mounting kit with M20 pole interface front installation...
Страница 138: ...138 Figure 111 Dimensions of OSM mounting kit with M20 pole interface lateral installation...
Страница 139: ...139 Figure 112 Dimensions of OSM mounting kit for installation through the pole front installation...
Страница 140: ...140 Figure 113 Dimensions of OSM mounting kit for installation through the pole lateral installation...
Страница 149: ...149 Figure 122 Dimensions of OSM substation mounting kit...
Страница 150: ...150 Figure 123 Dimensions of RC mounting kit for around the pole installation 500 mm U profiles 450 mm M16 threaded rods...
Страница 152: ...152 Figure 125 Dimensions of RC mounting kit for through the pole installation...
Страница 153: ...153 Figure 126 Dimensions of RC substation mounting kit...
Страница 154: ...154 Figure 127 Dimensions of VT mounting kit One VT holder...
Страница 157: ...157 Figure 132 Dimensions of VT mounting kit Two VT holders two 500 mm U profiles and M16 threaded rods...
Страница 158: ...158 Figure 133 Dimensions of VT mounting kit Two VT holders two 700 mm U profiles and M20 threaded rods...
Страница 159: ...159 Figure 134 Dimensions of VT mounting kit Two VT holders four 500 mm U profiles and M16 threaded rods...
Страница 163: ...163 Appendix 8 Connectors Drawings Figure 141 Dimensions of aerial connector...
Страница 164: ...164 Figure 142 Dimensions of bird guards for aerial connector...
Страница 165: ...165 Figure 143 Dimensions of two hole NEMA connector...
Страница 166: ...166 Figure 144 Dimensions of bird guards for two hole NEMA connector...
Страница 167: ...167 Figure 145 Dimensions of four hole NEMA connector...
Страница 168: ...168 Figure 146 Dimensions of bird guards for four hole NEMA connector...
Страница 169: ...169 Figure 147 Dimensions of Burndy NEMA connector...
Страница 170: ...170 Appendix 9 Recloser Control Wiring Diagram Figure 148 RC5_4 wiring diagram...
Страница 172: ......