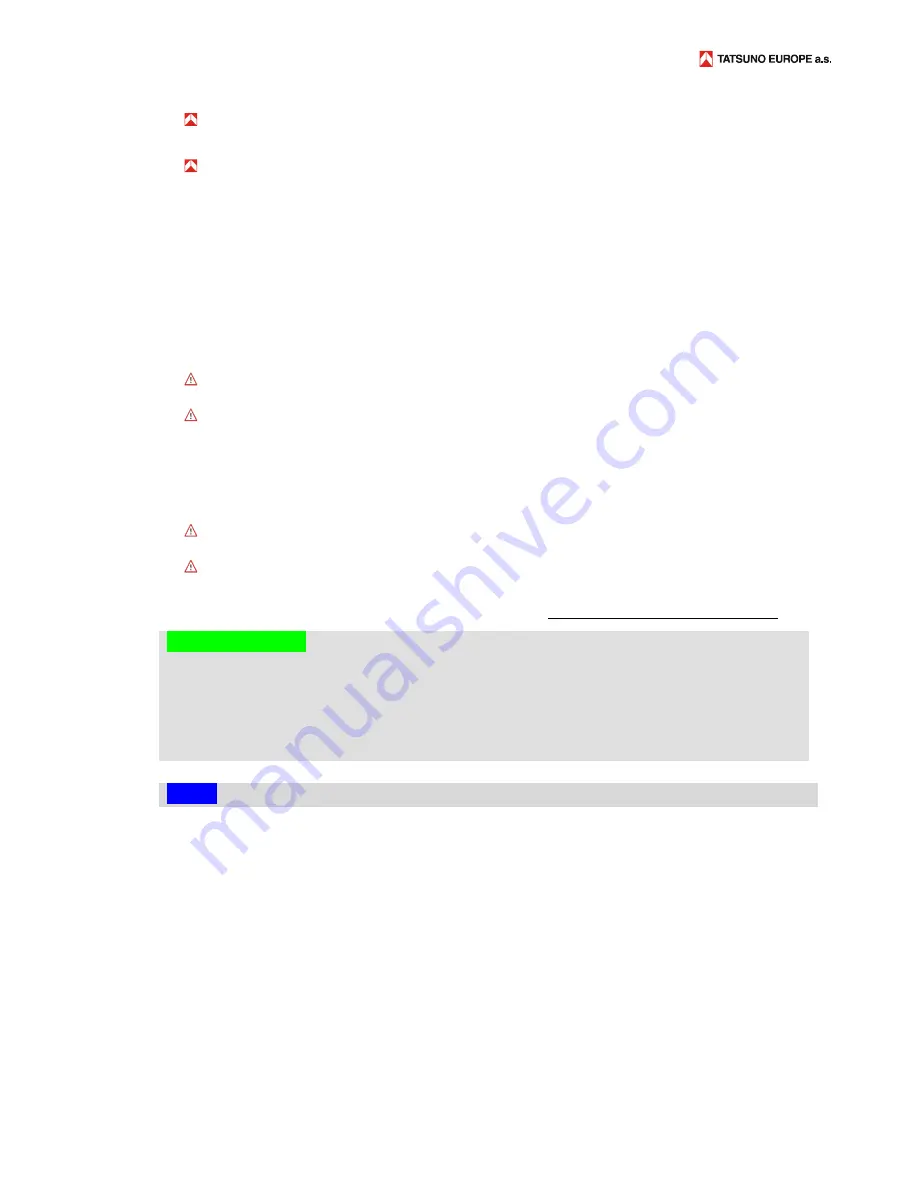
CNG dispensers TATSUNO EUROPE ‐ Quick User Guide
27
inspect the condition of the delivery nozzle, hose and breakaway couplings and decide on repair or
replacement of the delivery nozzle, if necessary, according to the type and size of the defect
care for external cleanliness of the dispenser, pay special attention to counter window cleanliness
4.1.1.
MAINTENANCE OF DISPENSER COVERS
Covers of the dispenser (“body parts”) made of painted steel or stainless steel require regular maintenance. Pay
special attention to the maintenance of such parts particularly in winter season when, due to the activity of
aerosols from chloride agents created from salts used for road maintenance, the paint of unprotected body
parts may be permanently damaged, or inter‐crystal corrosion may appear in case of stainless steel covers.
Recommended maintenance of painted covers:
Wash them with warm water at least twice per month (according to the level of fouling)
At least once a month or after each higher surface fouling with fuels – wash them with detergent,
thoroughly clean the covers from salt residues, dust and grease (according to the level of fouling) +
restore the protective coating on design parts (car cosmetics).
Recommended maintenance of stainless covers:
Wash them with warm water at least twice per month (according to the level of fouling)
At least once a month or after each higher surface fouling with fuels – wash them with warm water,
thoroughly clean the covers from salt residues, dust and grease (according to the level of fouling) +
restore the protective coating on design parts by using a special agent for stainless sheet metal.
RECOMMENDATION
We recommend the following protective agents and detergents for stainless sheet metal:
‐
ULTRAPUR – d
(producer: MMM‐Group, Germany)
‐
NEOBLANK spray
(producer: Chemische Fabrik GmbH, Hamburg, Germany)
‐
ANTOX Surface Care 800 S
(producer: Chemetall AG, Switzerland)
NOTICE
DO NOT WASH STAINLESS COVERS WITH DETERGENTS!
4.1.2.
LEVER‐SHUT‐OFF BALL VALVE
It is located in the lower part of the pressure module on the inlet pipeline – identification OVI, OVM and OVH
on the dispenser diagram – see Appendices 3.2, 3.3 and 3.4. The ball valve is intended for immediate shut off
the media flow rate in case of emergency or service of the dispenser. At multi‐level systems of filling the inlet
pipeline of each pressure level has its own shut‐off ball valve. The valve is normally maintenance‐free. Potential
defects are solved by replacement. Replacement may only be performed by an employee of the authorized
service company.
4.1.3.
FILTER