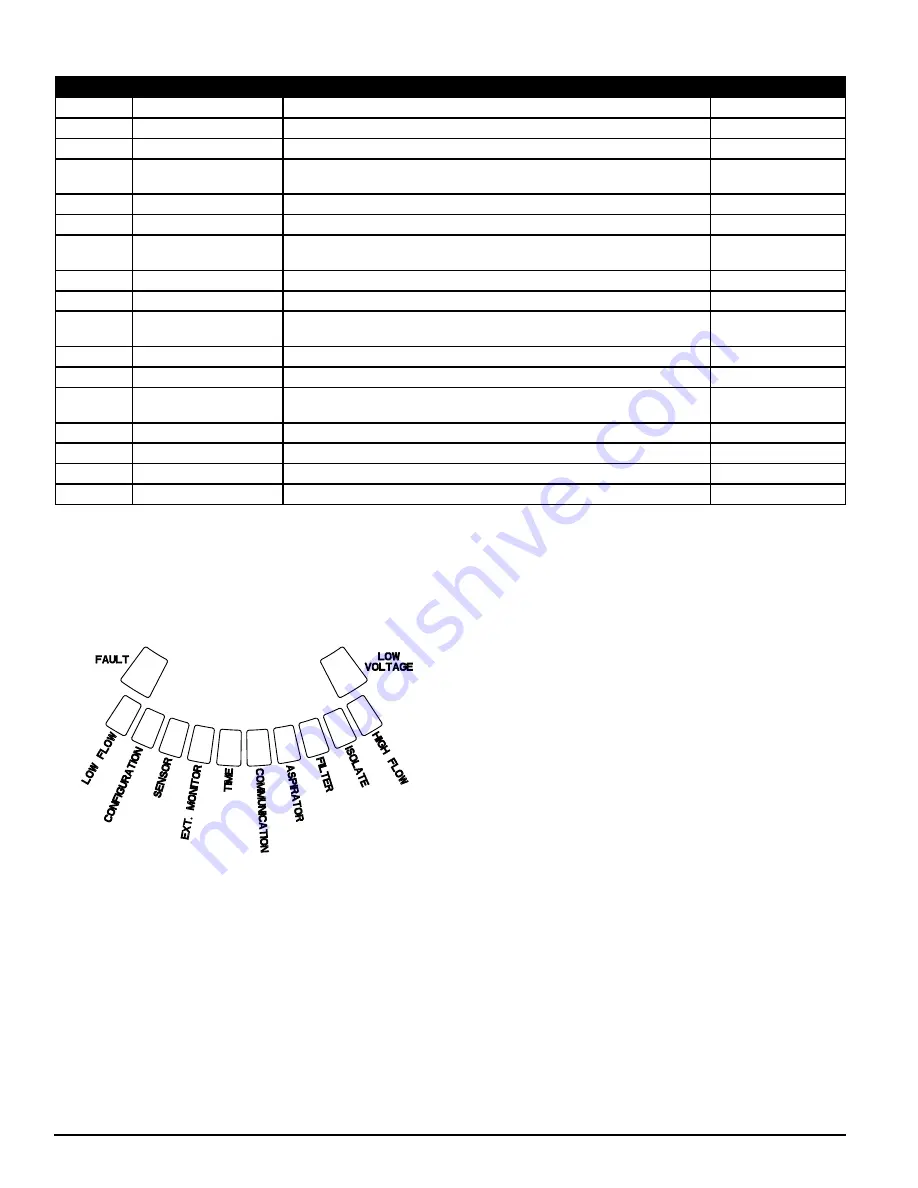
SS-400-012 8 I56-3749-006
FIGURE 13. FAULT DISPLAY
ASP13-00
NUMBER
NAME
DESCRIPTION
ACTIVATED RELAY
1
Low Flow Fault
Device has decreased airflow of 20%.
Minor Fault
Device has decreased airflow of 50%.
Urgent Fault
2
Configuration
Configuration of device with configuration software has failed.
Minor Fault
Device was interrupted with a power loss during configuration. A Reset will clear
this fault and device will revert back to it's last good configuration.
Minor Fault
Device is new and has not been configured.
Urgent Fault
Device has corrupt configuration and is unable to operate.
Urgent Fault
3
Sensor Fault
Device has problem with the particulate sensor and needs immediate replace-
ment.
Urgent Fault
4
External Monitor Fault
External monitor detects open.
Minor Fault
5
Time Fault
Internal Time base needs updating.
Minor Fault
6
Communication Fault
Device has failed to communicate to one of it's peripherals and cannot function
properly.
Urgent Fault
7
Aspirator Fault
Indicates the fan has stopped working and requires immediate attention.
Urgent Fault
8
Filter Fault
Device filter is clogged and requires replacement.
Minor Fault
Device filter is clogged and has not been replaced 72 hours after giving the Filter
Fault with Minor Fault Relay set.
Urgent Fault
9
Isolate Fault
Device has been put in isolate mode.
Isolation Fault
10
High Flow Fault
Device has Increased airflow of 20%.
Minor Fault
Device has Increased airflow of 50%.
Urgent Fault
11
Low Voltage Fault
Device Input voltage is low.
None
TABLE 5. FAULT DESCRIPTION
FAULTS
Whenever a fault occurs, the general FAULT indicator illuminates amber and
the flow status bar oscillates between flow status (green) and a detailed fault
status (amber). Table 5 shows the number, name, description and the acti-
vated relay for each fault. The fault display on the user interface is shown in
Figure 13.
REAL–TIME CLOCK
The unit is equipped with a real-time clock and power supply that allows
the FAAST system to maintain the date and time for up to 72 hours after a
loss of power. Date and time are configured through the PipeIQ software. The
real-time clock is used to maintain a time base for the device. This time base
is used to time stamp all log entries, as well as determine when it is time to
transfer from day, night and weekend modes. If the device loses power for
more than 72 hours the device sets the TIME fault indicating the time needs
to be updated.
LOGS
Event Log
The FAAST system is equipped with internal memory that can be configured
to log detector events. Up to 18,000 events can be stored. Events that are
tracked include alarms, faults and user actions. Event tracking data may be
accessed via the network through the PipeIQ software or the Web server in-
terface. Configuration and management of the log are done using the PipeIQ
software.
Data Trend Log
The FAAST system tracks trend data for each 24 hour time period, up to 1
year. The device records the minimum, maximum and average reading of the
sensor and flow values for each day.
Message Log
The message log allows the user to enter generic text messages into the sys-
tem’s memory. Messages may be retrieved for viewing at a later time. These
messages may be used to track service history, configuration changes, etc. A
maximum of 300 messages may be stored.
EXTERNAL MONITOR/RESET
The FAAST system has an external monitor that can detect an open or a short
when the supplied 47 K-ohm end of line resistor is used. When the device
senses an open circuit it sets the External Monitor fault indicator and sets the
Minor fault relay. When a short circuit is detected the device performs a Reset.
This provides the ability to reset alarm latches remotely.
ETHERNET CONNECTION
The FAAST system is a network capable device that is compatible with standard
Ethernet networking equipment. Connectivity is provided by an onboard RJ-45
connector located on the bottom of the unit, as shown in Figure 14. The network
interface is required for initial detector configuration. Once initial setup is com-
plete, the Ethernet connection provides optional remote access, monitoring and
e-mail notification through the unit’s Web server and SMTP client.
NOTE: Class 1, Div 2 - RJ45 Connector is for maintenance use only and shall
not be used while in a Hazardous Location unless power has been removed or
the area is known to be non-hazardous.
PIPE NETWORK
The unit can monitor up to 8,000 sq.ft. (approx. 743 sq. m) with a properly
designed pipe network. The pipe network must be properly configured using
the PipeIQ software. The pipe network accommodates a maximum single pipe
length of 262 ft. (80 m). If two branches are used, the maximum single pipe
length is 165 ft. (50 m). The device is capable of both metric 25 mm and IPS
1.05 in. pipe outside diameters without the use of an adaptor. The internal
pipe diameter can range from .591-.827 inches (15-21mm). Only 1 inlet and 1
outlet pipe are used at a time. Pipe networks may be constructed of various
materials such as ABS, cPVC, PVC, copper or stainless steel pipe. Travel time
from the furthest hole depends on the application of the device, but is limited
to a maximum of 120 seconds by the PipeIQ software. Refer to local agency
requirements and PipeIQ software for proper configuration.