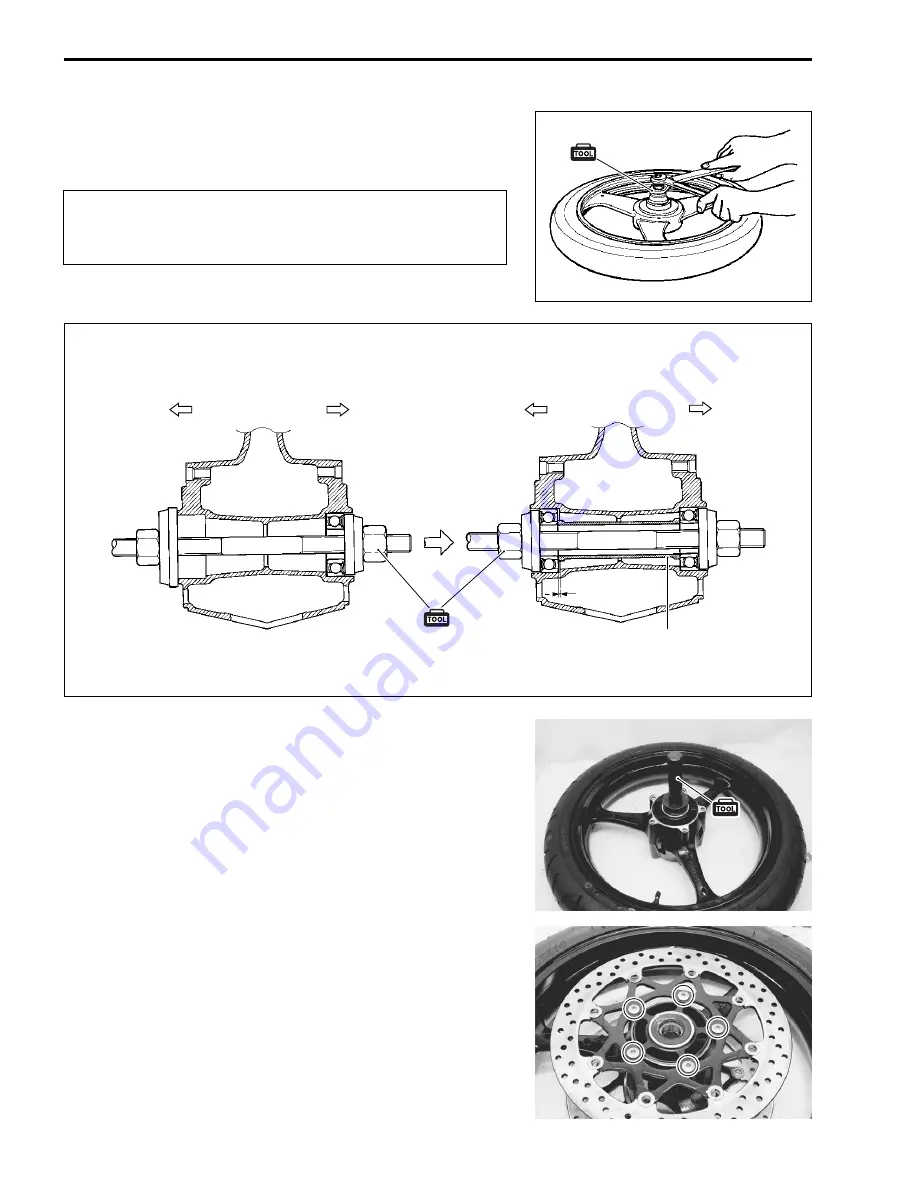
8-14 CHASSIS
• Install the wheel bearings with the special tools as follows.
09924-84510: Bearing installer set
• Install the dust seal with the special tool.
09913-70210: Bearing installer set
• Apply SUZUKI SUPER GREASE “A” to the dust seal lip.
99000-25010: SUZUKI SUPER GREASE “A”
(or equivalent grease)
BRAKE DISC
• Make sure that the brake disc is clean and free of any greasy
matter.
• Apply THREAD LOCK to the disc mounting bolts and tighten
them to the specified torque.
Brake disc bolt (Front): 23 N·m (2.3 kgf-m, 16.5 lb-ft)
99000-32130: THREAD LOCK SUPER “1360”
First install the right wheel bearing, then install the
spacer and left wheel bearing.
The sealed cover of the bearing must face outside.
Left
Right
Left
Right
Clearance
Spacer
Содержание 2006 gsxr 600
Страница 1: ...GSX R750 9 9 5 0 0 3 7 1 3 0 0 1 E ...
Страница 48: ...PERIODIC MAINTENANCE 2 31 ...
Страница 101: ...3 48 ENGINE TRANSMISSION PARTS LOCATION 1 Countershaft 2 Driveshaft ...
Страница 154: ...ENGINE 3 101 10 N m 1 0 kgf m 7 0 lb ft ...
Страница 324: ...7 20 COOLING AND LUBRICATION SYSTEM ENGINE LUBRICATION SYSTEM ...
Страница 325: ...COOLING AND LUBRICATION SYSTEM 7 21 ...
Страница 487: ...10 28 SERVICING INFORMATION SEAT LOCK CABLE ROUTING REAR FENDER INSTALLATION ...
Страница 521: ...Prepared by December 2005 Part No 99500 37130 01E Printed in Japan 524 ...
Страница 522: ...Printed in Japan K6 ...