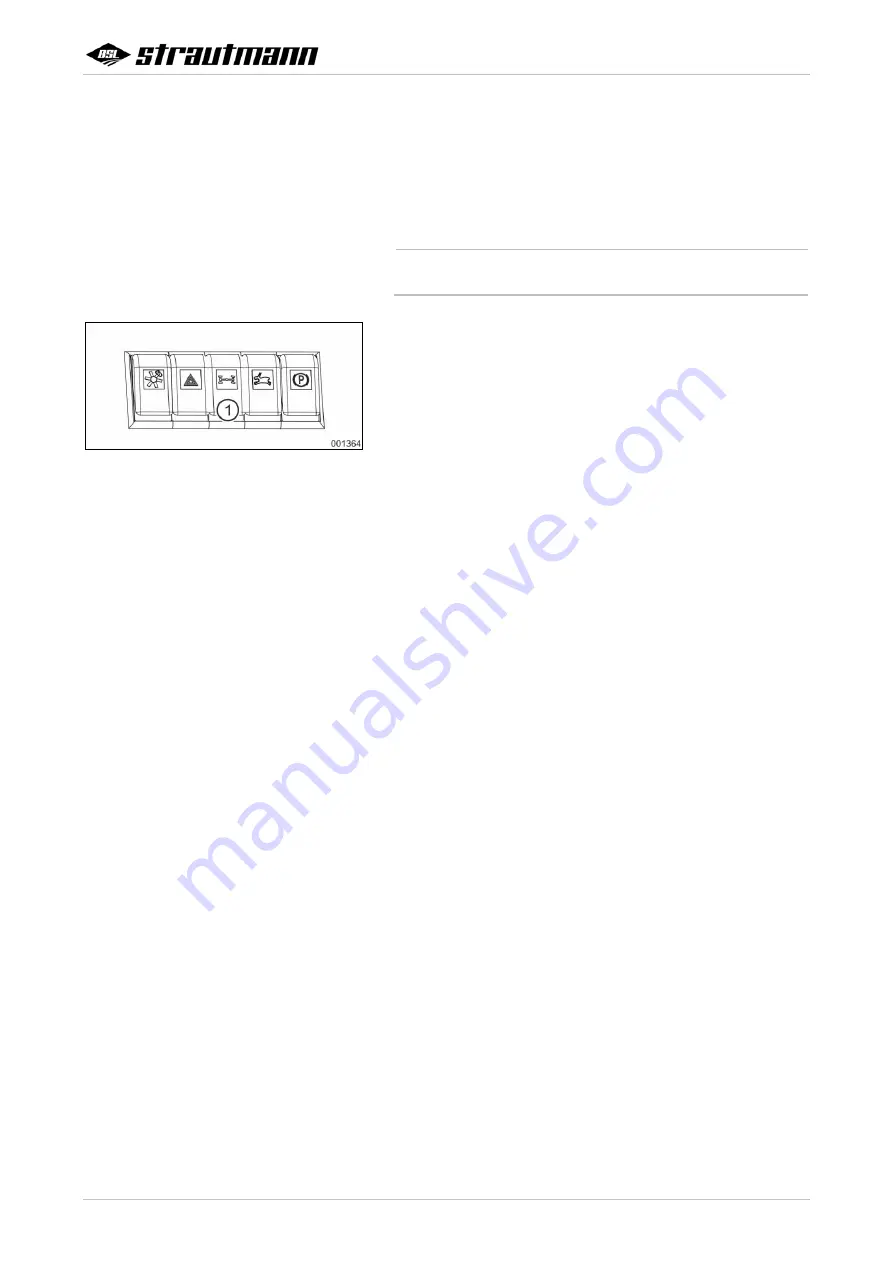
Operation
Sherpa 120, 140 | 06.19
99
7.4
Travelling with differential lock
Only use the differential lock to start travelling on smooth or
soft ground.
NOTE
Only switch the differential lock on with the machine being
stationary.
1. Switch differential lock on.
–
Press the switch (1) down.
2. Carefully start travelling if the differential lock has not
completely engaged.
–
Avoid cornering.
–
Do not exceed a travelling speed of 5 km/h.
3. Switch differential lock off.
–
Unlock the switch (1) and push it up.
Fig. 69
7.5
Turn off diesel engine
1. Switch the parking brake on.
2. Set the manual throttle lever to idle position.
–
Let the diesel engine run in idle position for
5 minutes, in order to allow hot engine components
to cool down and prevent a heat build-up in the
engine compartment.
3. Turn the ignition key to position 0.
→ The diesel engine stops and the ignition is off. The
terminal goes out.
4. Pull the ignition key out before leaving the driver's cabin.
5. Top up the fuel tank.
–
Thus, condensation is minimised. If the fuel tank is
topped up after operation of the machine, the humid
air is pushed out of the tank.
6. Switch the battery disconnector off.
→ The power supply is disconnected.
Содержание Sherpa 120
Страница 2: ......