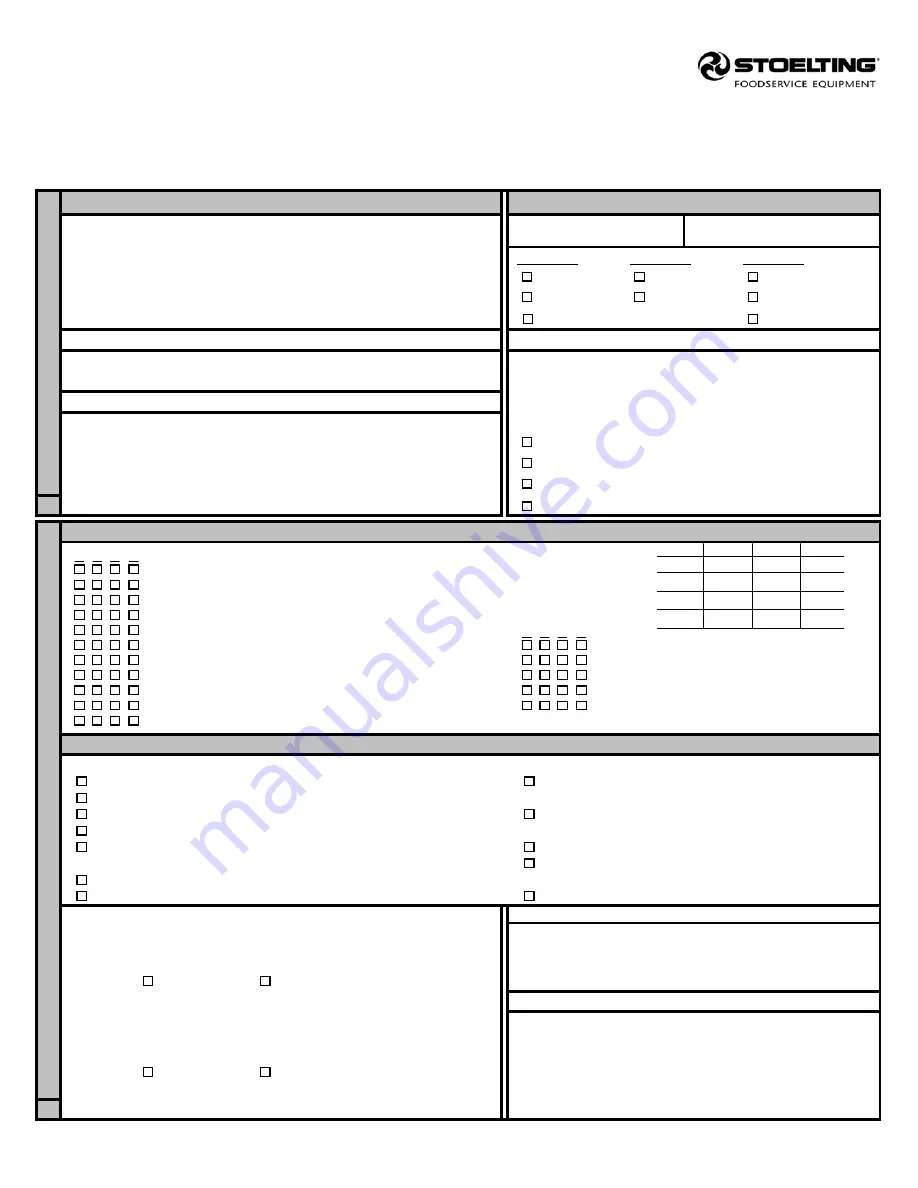
Custard Freezer Start-Up and Training Checklist
Distributor Instructions:
Complete this form, obtain customer comments and signature and send to:
502 Hwy 67
Kiel WI 53042
NOTE:
A separate form must be submitted for each individual freezer.
BUYER INFORMATION
FREEZER INFORMATION (See freezer I.D. plate)
Installed at (business name): ____________________________________
Contact person: _______________________________________________
Check one:
Check one:
Check one:
Address: ____________________________________________________
115 volts
single phase
air-cooled
City: ________________________________________________________
208 volts
three phase
water-cooled
State:________ Zip: __________ Phone: ( ) __________________
230 volts
air remote
DISTRIBUTOR INFORMATION
APPOINTMENT SCHEDULES
Business Name: _______________________________________________
Check-out/start-up scheduled for: ___/___/___ at _____AM/PM
Account Number: ______________________________________________
Appointments arranged by: ____________________________
AUTHORIZED SERVICE COMPANY (IF DIFF. THAN DISTR.)
with (buyer contact): _________________________________
Business Name: ______________________________________________
NOTE:
Before leaving for appointment, phone to see that:
____________________________________________________________
electrical complete
Address: ____________________________________________________
water & drain complete (water-cooled)
City: ________________________________________________________
mix, cones, cups, syrup, etc. available
A
State:________ Zip: __________ Phone: ( ) __________________
trainee personnel available
CHECK-OUT START-UP CHECKLIST (Each column represents a freezing cylinder)
1 2 3 4
(Check a column for each freezing cylinder)
Proper voltage, phase, breaker (check against nameplate)
Proper wire size per local code
High or unstable leg to L-2 (3-phase only)
Freezer level, front-to-back and side-to-side
Parts and accessories kit complete
1 2 3 4
Nuts, bolts, screws, electrical tight
Checked low pressure switch settings.
Drive belt tension/no lubricant leaks/check pulley and set screws
Locked thermostat settings.
Auger rotating counterclockwise
Water lines flushed before connection
(W/C)
Checked pressures on high side, suction side and barrel.
Proper water and drain size
(W/C)
Refrigeration level during operation (clear sight glass)
Proper clearance for air circulation
(A/C Remote)
Checked alignment
TRAINING CHECKLIST
Check off as completed:
Reviewed Owner's Manual with trainees.
Check for auger seal, bearing & flight wear each time the
Reviewed Operator's Safety Precautions in Owner's Manual
freezer is cleaned.
Reviewed Warranty Shown in Owner's Manual
Point out where Service Information Decal/Label is placed by
Disassemble, wash all parts, sanitize, lubricate & assemble.
the Distributor or Service Contractor.
Sanitize and start-up.
Key points: minimum mix level in hopper, etc.
Note:
Sanitizing must be done immediately before starting freezer.
Explain how foam in the hopper can prevent the low mix light
Check product temperature ___________ °F, overrun _____________
from illuminating.
Shutdown and cleaning procedure.
Discuss returning included survey if they choose.
LIST OF TRAINEES - Name of Trainees -
Training conducted by:
___________________________________________________
___________________________________________________
Name: _________________________________ Date: _____/_____/_____
___________________________________________________
Check one: Distributor Authorized Service Agency
SIGNATURE REQUIRED
Inspection/Checkout done by:
Inspection, check-out and operator training has been performed
on the above freezer. I have read and understand the warranty
Name: _________________________________ Date: _____/_____/_____
shown in the Owner's Manual.
Check one: Distributor Authorized Service Agency
x _________________________________________________
Signature, Buyer/Manager/Supervisor Date
Completed forms must be returned to Stoelting by mail, fax (800-545-0662), or email ([email protected]).
Form #721-064 Rev. 0
IMPORTANT:
THIS SHEET MUST BE COMPLETED AND MAILED, FAXED, OR EMAILED WITHIN 30 DAYS
OF START-UP BY THE DISTRIBUTOR OR END-USER TO STOELTING IN ORDER TO REGISTER THE UNIT
UNDER WARRANTY. IF WE DO NOT RECEIVE IT, WE CANNOT PROCESS FUTURE WARRANTY CLAIMS.
B
Thi
s secti
on to be com
p
le
ted at i
n
stal
la
ti
on si
te.
Model No.
Serial No.
Thi
s secti
on to be com
p
le
ted before vi
si
ti
ng si
te.
Actual Settings 1 2 3 4
Supply Voltage
Head Pressure
Suction Pressure
Barrel Pressure
Содержание M202A
Страница 1: ...Model M202A Ser 0 25244 OPERATORS MANUAL Manual No 513614 Rev 5...
Страница 2: ......
Страница 12: ......
Страница 14: ......
Страница 16: ...001 1332808 2...
Страница 26: ......
Страница 30: ......
Страница 32: ......