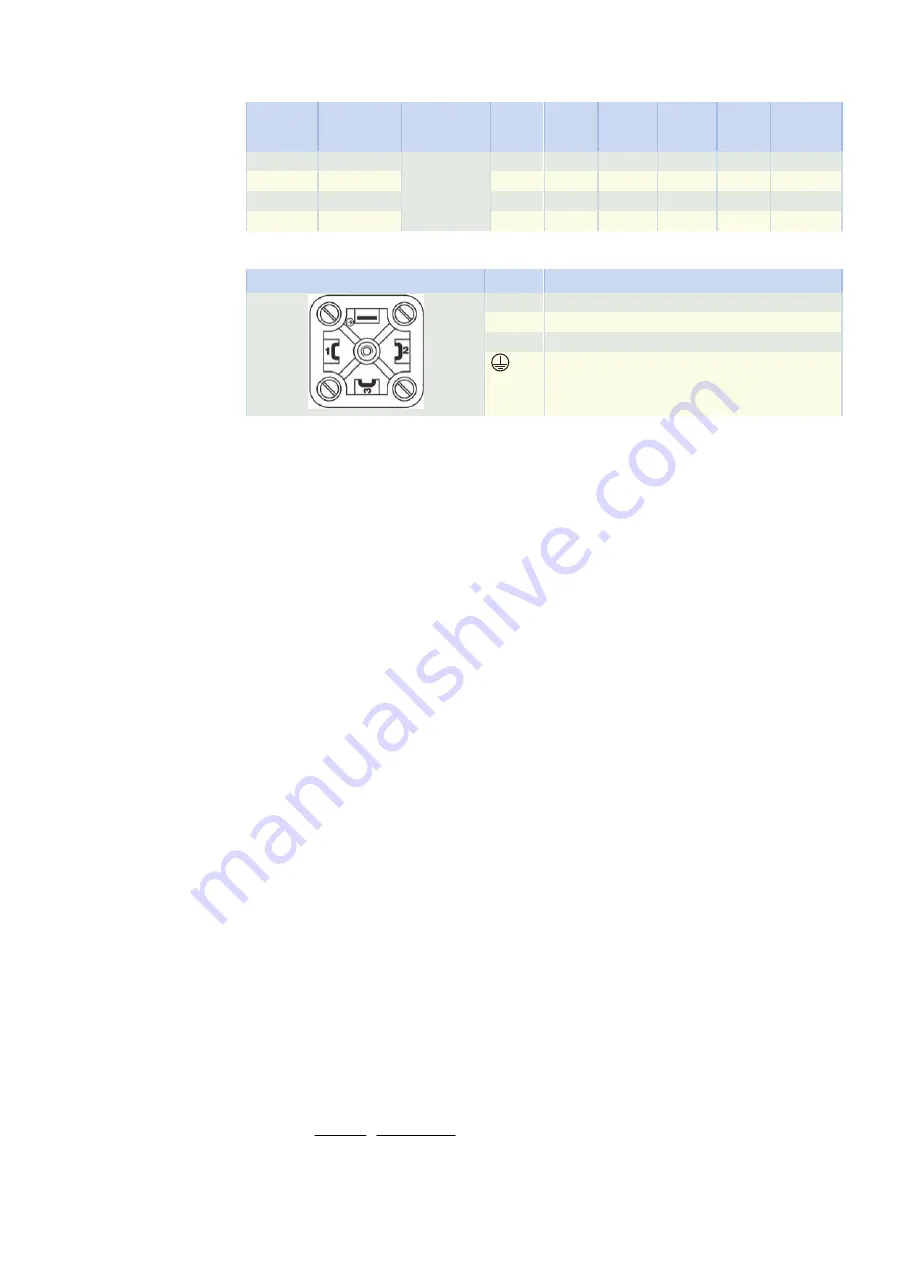
Technical data
Motor
Forced venti-
lation unit
U
N,F
[V]
I
N,F
[A]
P
N,F
[W]
q
vF
[m³/h]
L
pA,F
[dBA]
m
F
[kg]
Protection
class
EZ4_B
FL4
230 V ± 5%,
50/60 Hz
0.07
10
59
41
1.4
IP44
EZ5_B
FL5
0.10
14
160
45
1.9
IP54
EZ7_B
FL7
0.10
14
160
45
2.9
IP54
EZ8_B
FL8
0.20
26
420
54
5.0
IP55
Terminal assignment for forced ventilation unit plug connectors
Connection diagram
Pin
Connection
1
L1 (phase)
2
N (neutral conductor)
3
Grounding conductor
11.6.7
Holding brake
STOBER synchronous servo motors can be equipped with a backlash-free holding brake using permanent
magnets in order to secure the motor shaft when at a standstill. The holding brake engages automatically if
the voltage drops.
The holding brake is designed for a high number of operations (B
10
= 10 million operations, B
10d
= 20 million
operations).
Nominal voltage of permanent magnet holding brake: DC 24 V ± 5%, smoothed.
Observe the following during project configuration:
•
The holding brake is designed to keep the motor shaft from moving. Activate braking processes during
operation using the corresponding electrical functions of the drive controller. In exceptional circum-
stances, the holding brake can be used for braking from full speed (following a power failure or when
setting up the machine). The maximum permitted work done by friction W
B,Rmax/h
may not be exceeded.
•
Note that the braking torque M
Bdyn
may initially be up to 50% less when braking from full speed. As a re-
sult, the braking effect has a delayed action and braking distances become longer.
•
Regularly perform a brake test to ensure the functional safety of the brakes. Details can be found in the
documentation of the motor and the drive controller.
•
Connect a varistor of type S14 K35 (or comparable) in parallel to the brake coil to protect your machine
from switching surges. (Not necessary for connecting the holding brake to STOBER drive controllers of
the 5th and 6th generation with a BRS/BRM brake module).
•
The holding brake of the motor does not offer adequate safety for persons in the hazardous area of
gravity-loaded vertical axes. Therefore take additional measures to minimize risk, e.g. by providing a
mechanical substructure for maintenance work.
•
Take into consideration voltage losses in the connection cables that connect the voltage source to the
holding brake connections.
•
The holding torque of the brake can be reduced by shock loading. Information about shock loading can
be found in the "Ambient conditions" chapter.
•
At operating temperatures from −15 °C to 0 °C, a cold holding brake in the released state may cause op-
erating noises. As the temperature of the holding brake increases, these noises decrease such that op-
erating noises are not heard when using holding brake at operating temperature in the released state.
Calculation of work done by friction per braking process
×
=
×
>
±
2
Bdyn
tot
B,R/B
Bdyn
L
Bdyn
L
M
J
n
W
, M
M
182.4 M
M
The sign of M
L
is positive if the movement runs vertically upwards or horizontally and it is negative if the
movement runs vertically down.
11 EZ synchronous servo motors
11.6 Product description
403
Содержание EZ
Страница 1: ...Synchronous servo geared motors with redundant brake ...
Страница 2: ......
Страница 3: ...Synchronous servo geared motors with redundant brake ...
Страница 12: ...1 Selection tool 1 3 Synchronous servo motors 12 ...
Страница 20: ...2 2 Selection tables 2 P planetary geared motors 20 ...
Страница 40: ...2 7 Additional documentation 2 P planetary geared motors 40 ...
Страница 46: ...3 2 Selection tables 3 PH planetary geared motors 46 ...
Страница 84: ...4 7 Additional documentation 4 PHQ planetary geared motors 84 ...
Страница 110: ...5 2 Selection tables 5 C helical geared motors 110 ...
Страница 136: ...5 7 Additional documentation 5 C helical geared motors 136 ...
Страница 184: ...6 7 Additional documentation 6 F offset helical geared motors 184 ...
Страница 200: ...7 2 Selection tables 7 PK right angle planetary geared motors 200 ...
Страница 222: ...7 7 Additional documentation 7 PK right angle planetary geared motors 222 ...
Страница 238: ...8 2 Selection tables 8 PHK right angle planetary geared motors 238 ...
Страница 258: ...8 7 Additional documentation 8 PHK right angle planetary geared motors 258 ...
Страница 276: ...9 2 Selection tables 9 PHQK right angle planetary geared motors 276 ...
Страница 298: ...9 7 Additional documentation 9 PHQK right angle planetary geared motors 298 ...
Страница 374: ...10 7 Additional documentation 10 K helical bevel geared motors 374 ...
Страница 416: ...11 8 Further information 11 EZ synchronous servo motors 416 ...
Страница 445: ...13 Connecting to drive controllers of third party manufacturers 13 7 Connection to Allen Bradley drive con trollers 445 ...
Страница 448: ...448 ...
Страница 456: ...15 3 Sales terms and delivery conditions 15 Appendix 456 ...
Страница 457: ......
Страница 458: ......
Страница 459: ......