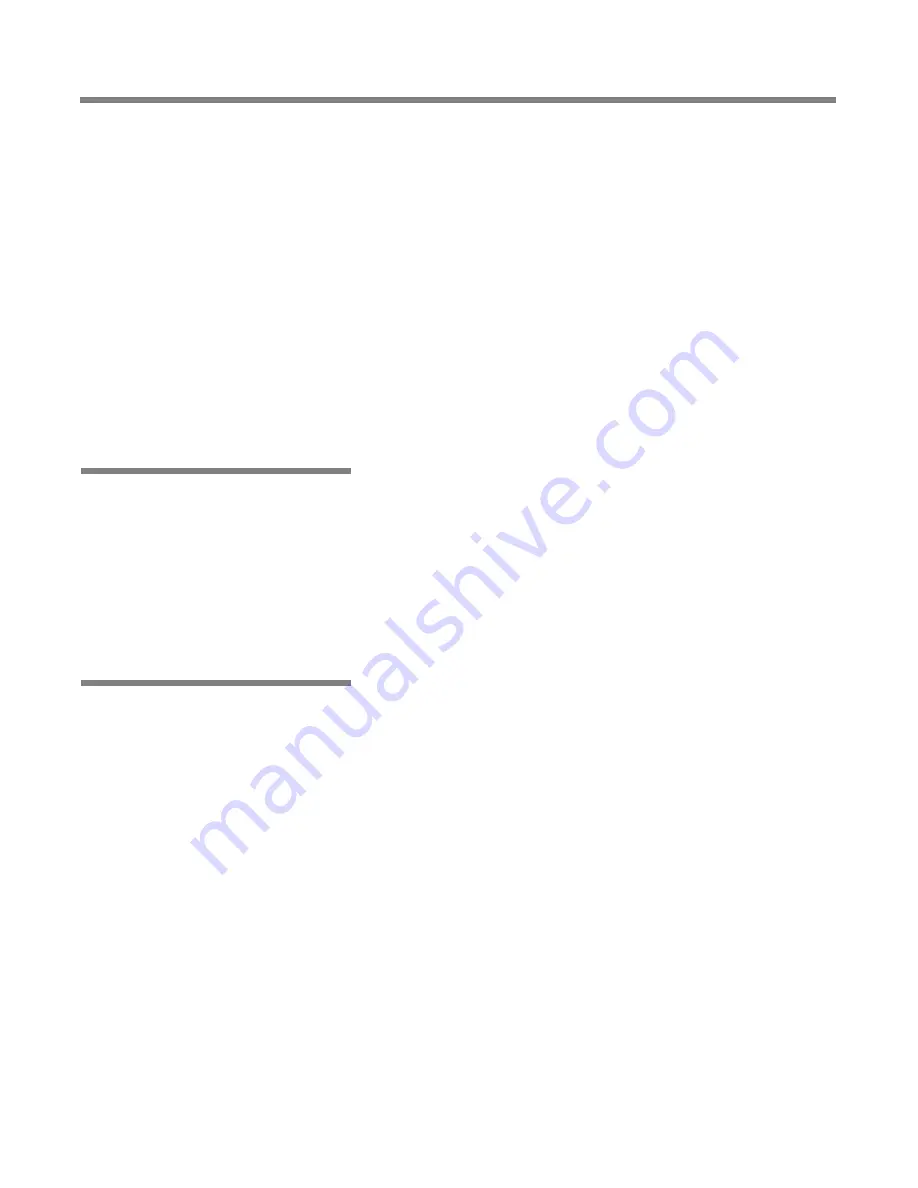
i
Introduction
Operator Manual
920509-645
A WORD FROM STERIS CORPORATION
This manual contains important information on the proper use of this
equipment. Refer to
,
for instruc-
tions in routine care of this washer.
All personnel and department
heads are urged to carefully review and become familiar with the
Safety Precautions and instructions contained herein.
These
instructions are important to protect the health and safety of person-
nel operating this
Basil
®
4700 Cage and Rack Washer
and should
be retained in a conveniently accessible area for quick reference.
This equipment is specifically designed only for the uses outlined in
this manual.
Complete instructions for uncrating and connecting utilities, as well
as equipment drawings, have been provided. If they are missing,
contact STERIS for replacement copies, providing the serial and
model numbers of the unit.
Advisory
IMPORTANT:
A listing of the Safety Precautions to be observed
when operating this washer can be found in S
1. Do not oper-
ate the equipment until you have become familiar with this informa-
tion.
Any alteration of this equipment not authorized or performed by
STERIS will void the warranty. Alteration of equipment which could
adversely affect its operation and efficacy may violate national, state
and local regulations and could jeopardize your insurance coverage.
Indications For Use
The
Basil 4700 Cage and Rack Washer
is specifically designed for
thorough, efficient cleaning of cages, bottles, debris pans and mis-
cellaneous items used in the care of laboratory animals.
This washer is specifically designed to only process goods as out-
lined in this manual. If there is any doubt about a specific material or
product, contact product manufacturer for recommended washing
technique.
©
2008, STERIS Corporation. All rights reserved.
Printed in Canada.
Содержание Basil 4700
Страница 1: ...MAINTENANCE MANUAL Basil 4700 Cage and Rack Washer 2008 10 15 P764333 097 ...
Страница 3: ...OPERATOR MANUAL Basil 4700 Cage and Rack Washer 2008 08 14 P920509 645 ...
Страница 87: ...MAINTENANCE MANUAL Maintenance Instructions Basil 4700 Cage and Rack Washer 2008 10 15 P764333 098 ...
Страница 169: ...MAINTENANCE MANUAL IIlustrated Parts Breakdown Basil 4700 Cage and Rack Washer 2008 10 15 P764333 099 ...
Страница 172: ...2 764333 099 Figure 1 Basil 4700 Cage and Rack Washer Inside Washer Inside Inside Washer ...
Страница 174: ...4 764333 099 Figure 2 Cabinet Assembly Left Side Control Shown ...
Страница 176: ...6 764333 099 Figure 3 Sump and Floor Grating Assembly ...
Страница 178: ...8 764333 099 Figure 4 Door Assembly ...
Страница 180: ...10 764333 099 Figure 5 Double Door Interlock System ...
Страница 182: ...12 764333 099 Figure 6 Interior Light ...
Страница 184: ...14 764333 099 Figure 7 Safety Emergency Stop Cable Assembly ...
Страница 186: ...16 764333 099 Figure 8 Spray Header Assembly ...
Страница 188: ...18 764333 099 Figure 9 Cable and Roller Assembly DETAIL A DETAIL B See Detail A See Detail B ...
Страница 190: ...20 764333 099 Figure 10 Traveler Drive and Limit Switch Assembly See Detail A DETAIL B DETAIL A See Detail B ...
Страница 192: ...22 764333 099 Figure 11 Automatic Water Rack Flush System For Two Racks Option ...
Страница 194: ...24 764333 099 Figure 12 Damper 1 ...
Страница 196: ...26 764333 099 Figure 13 Exhaust Fan ...
Страница 198: ...28 764333 099 Figure 14 Hot Water Line Components 6 5 4 10 10 7 8 9 7 ...
Страница 200: ...30 764333 099 Figure 15 Cold Water Line Components ...
Страница 202: ...32 764333 099 Figure 16 Recirculation Piping ...
Страница 204: ...34 764333 099 Figure 17 Steam Line Components ...
Страница 206: ...36 764333 099 Figure 18 Final Rinse System Assembly ...
Страница 208: ...38 764333 099 Figure 19 Recirculation Pump System and Self Cleaning Filter UC DRAIN TANK 1 TANK 2 SPRAY HEADER ...
Страница 210: ...40 764333 099 Figure 20 Pneumatic Block ...
Страница 212: ...42 764333 099 Figure 21 Peristaltic Chemical Injection Pumps ...
Страница 214: ...44 764333 099 Figure 22 Solution Tank 25 ...
Страница 216: ...46 764333 099 Figure 23 Tank Support Frame ...
Страница 218: ...48 764333 099 Figure 24 Guaranteed Cooldown Tank ...
Страница 220: ...50 764333 099 Figure 25a Electrical Box and Control Column Assembly ...
Страница 226: ...56 764333 099 Figure 26 Control Panel See Detail A DETAIL A ...
Страница 228: ...58 764333 099 Figure 27 Seismic Tie Down Anchorage Option ...
Страница 230: ...60 764333 099 Figure 28 Bottle Washing Cart WA02 010 ...
Страница 232: ...62 764333 099 Figure 29 Bottle Washing Cart WA02 020 ...
Страница 234: ...64 764333 099 Figure 30 Pan Cart WA02 030 Accessory ...
Страница 236: ...66 764333 099 Figure 31 Universal Cage and Pan Wash Cart WA03 100 7 ...
Страница 238: ...68 764333 099 Figure 32 Universal Cage Wash Cart WA02 040 ...
Страница 240: ...70 764333 099 Figure 33 Cart Tilt Ramp WA02 050 ...
Страница 242: ...72 764333 099 Figure 34 Floor Ramp for Floor Mounted Units WA02 060 ...
Страница 244: ......
Страница 245: ......
Страница 246: ......
Страница 247: ......
Страница 248: ......
Страница 249: ......
Страница 250: ......
Страница 251: ......
Страница 252: ......
Страница 253: ......
Страница 254: ......
Страница 255: ......
Страница 256: ......
Страница 257: ......
Страница 258: ......
Страница 259: ......
Страница 260: ......
Страница 261: ......
Страница 262: ......
Страница 263: ......
Страница 264: ......
Страница 265: ......