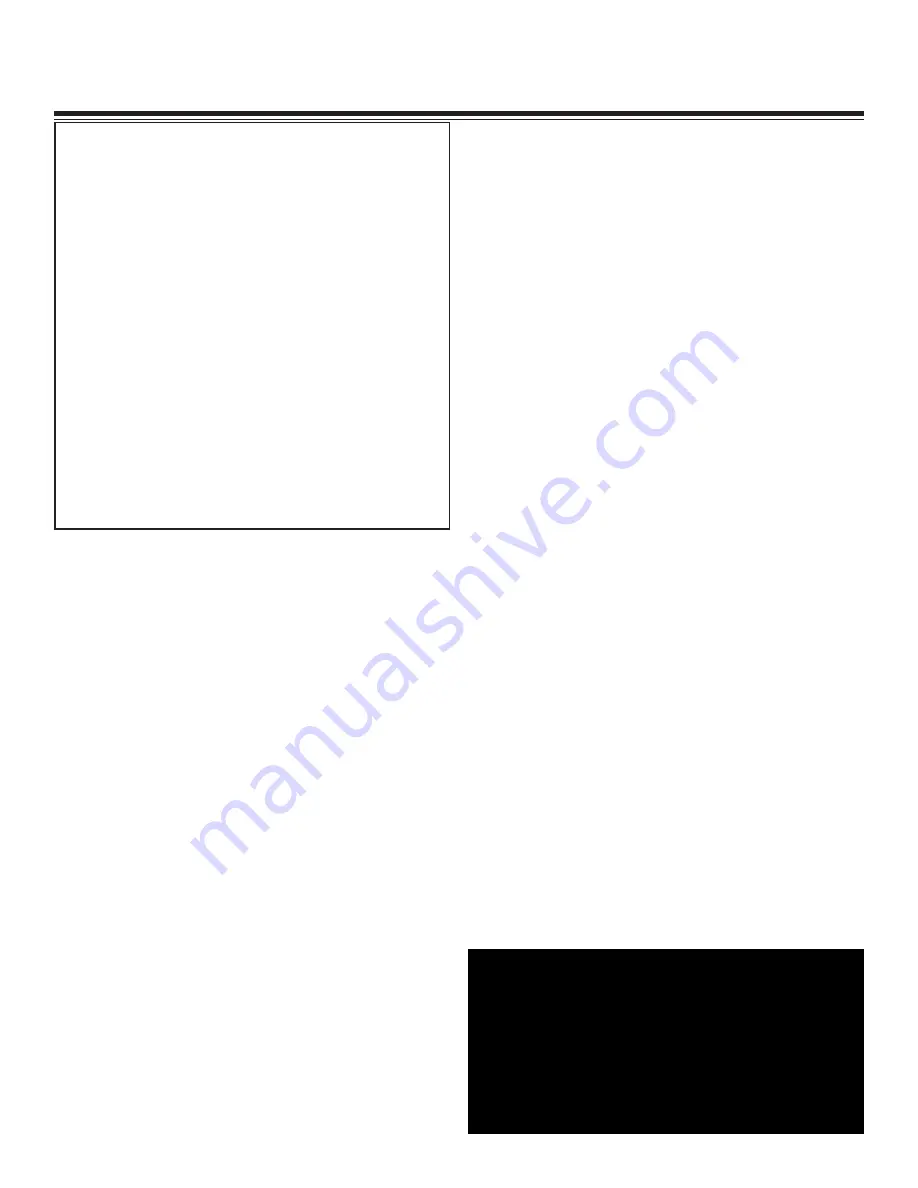
9
Maintenance
9
Chapter 3 - Maintenance
Maintenance Procedures
1. Position the hooklift where it will be out of the way of
other operations or vehicles in the area.
2. Place all controls in the off position and secure oper-
ating features from inadvertent motion.
3. Relieve hydraulic oil pressure from all hydraulic cir-
cuits before loosening or removing hydraulic compo-
nents.
4. Label or tag parts when disassembling.
Periodic Inspection
Periodic Inspection should occur while the hooklift is in
use. For the duration of the usage, inspect the hooklift
for all of the following:
1. Loose bolts and fasteners.
2. All pins, bushings, shafts, and gears for wear, cracks,
or distortion to include all pivot points, and bushings.
3. Hydraulic systems for proper operating pressure.
4. Main frame mount bolts.
5. Cylinders for:
A. Damaged rods.
B. Dented barrels.
C. Drift from oil leaking internally.
D. Leaks at rod seals or holding valves.
6. PTO and hydraulic pump(s) for leaks.
7. Hydraulic hose and tubing for evidence of damage
such as blistering, crushing, or abrasion.
8. Presence of this owner’s manual.
Daily Inspection
Daily Inspection should occur each day before the
hooklift is put into use. Each day, inspect the hooklift for
all of the following:
1. Hydraulic oil level.
2. Loose parts or damage to structures or weld.
3. Cylinder movement due to leakage.
4. Hoses for evidence of oil leaks.
5. Controls for malfunction or adjustment.
6. Parking brake operation.
7. All securing hardware such as cotter pins, snap rings,
hairpins, and pin keepers for proper installation.
8. All safety covers for proper installation.
9. Cylinder holding valves for proper operation.
10. Equipment for missing, illegible, or defaced operat-
ing decals and safety signs.
Monthly Inspection
Monthly Inspection should occur at the beginning of
every work month. Each month, inspect the hooklift for
all of the following:
1. Frame bolt tightness - turn barrel nuts and mounting
bolts during the first month of operation on new
machines and then quarterly thereafter.
2. Cylinders and valves for leaks.
3. Lubrication.
4. Jib hook for cracks.
5. Structural weldments for bends, cracks, or breaks.
6. All pins and keepers for proper installation.
7. All control, safety, and capacity placards for read-
ability and secure attachment.
8. Inspect all electrical wires and connections for worn,
cut, or deteriorated insulationand bare wire. Replace
or repair wires as required.
10. Lubrication of all points requiring lubrication.
General Service
The following general suggestions should be helpful in
analyzing and servicing your hooklift. Using the following
systematic approach should be helpful in finding and
fixing problems:
1. Determine the problem.
2. List and record possible causes.
3. Devise checks.
4. Conduct checks in a logical order to determine the
cause.
5. Consider the remaining service life of components
against the cost of parts and labor necessary to
replace them.
6. Make the necessary repair.
7. Recheck to ensure that nothing has been overlooked.
8. Functionally test the new part in its system.
Please read the following before performing any
maintenance on the hooklift.
1. Only authorized service personnel are to perform
maintenance on the hooklift.
2. Disengage the PTO before any service or repair is
performed.
3. Do not disconnect hydraulic hoses while there is
still pressure in those components.
4. Before disconnecting hydraulic components,
shut off the engine, release any air pressure on
the hydraulic reservoir, and move control levers
repeatedly through their operating positions to
relieve all pressures.
5. Keep the hooklift clean and free from grease
build-up, oil and dirt to prevent slippery condi-
tions.
6. Perform all safety and maintenance checks
before each period of use.
7. Replace parts with Stellar Industries, Inc.
approved parts only.
8. Immediately repair or have repaired any compo-
nents found to be inadequate.
ATTENTION
Every six (6) months, remove the hydraulic
pump from the PTO and lubricate the splines
using Chelsea Lubricant #379831 or Stellar
PN 42042 (packet) or PN 20885 (tube).
Failure to lubricate shaft splines will cause
damage to the PTO and Hydraulic pump
.
Содержание Slider20
Страница 2: ...Slider20 Hooklift Manual Revisions Date of Revision Description of Revision Section Revised...
Страница 14: ...8 Slider20 Owner s Manual...
Страница 33: ...Installation 27 PN 44045 Hydraulic Schematic PN 44045...
Страница 34: ...28 Slider20 Owner s Manual PN 41133 Wiring Schematic PN 41133...
Страница 42: ...36 Slider20 Owner s Manual...