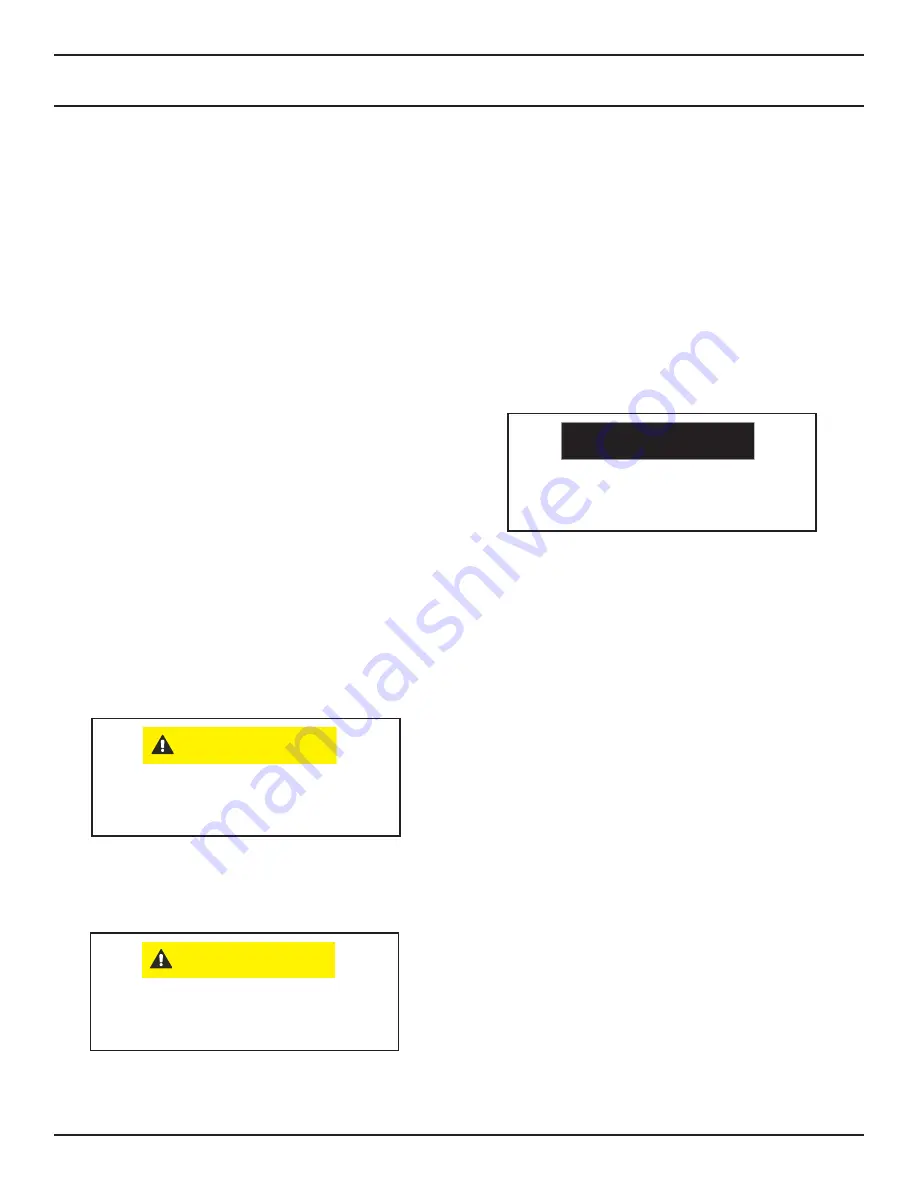
20
1. To remove the engine, follow steps 1 through 4 under
"Fuel Tank Removal".
2. Disconnect the wiring harness (See Figure 4 & 4A, Wir-
ing Diagrams for the correct connections).
3.Follow steps 1 through 4 under "Manifold Assembly Re-
moval".
4. Disconnect the 12 Volt plug wiring harness (if so
equipped). Remove the RED wire attached to the starter
solenoid and the BLACK wire to ground.
5. Follow steps 1 through 3 under "Choke Cable Assembly
Removal".
6. Follow steps 1 through 6 under "Hydraulic Tank, Cooler
and Filter Removal".
7. Follow steps 1 through 5 under "Blower Housing, Blower
Hub & Bushing Removal.
From this point there are two options, to remove the engine
with the pump and pump mount attached
A) Lift straight up after removing the frame weldment.
or
B) Remove the wheel from one side of the unit and slide
the engine out the side of the unit.
OPTION A
Remove the frame weldment by removing the two hex
fl ange bolts (17, fi g. 2) and two hex fl ange bolts (47, fi g. 1
& 1A).
Remove the two capscrews (21, fi g. 1 & 1A) that hold the
cooler guard (20, fi g. 2). Lift off the frame weldment.
SERVICE
CAUTION
Make sure the frame base is on blocks or
supported before removing the wheel.
CAUTION
Make sure the frame base is on blocks or
supported before removing the wheel.
OPTION B
Block up the unit to keep it from tipping over.
Remove the handle bumper (42, fi g. 1 Briggs) or (88 fi g. 1A
Honda) from one end of the axle.
Remove the retaining ring and washer (48, 49, fi g. 1 & 1A)
and remove the wheel. The engine and hydraulic tank can
now be removed from the side of the unit.
ELECTRICAL
Refer to the wiring diagram in this manual for the correct
connections, wire sizes and colors.
BLOWER HOUSING, BLOWER HUB AND
BUSHING REMOVAL
(SEE FIGURE 1 & 1A)
1. Follow steps 1 through 6 of the Hydraulic Tank, Cooler
and Filter Assembly removal procedure.
2. Follow steps 1 through 4 of the Blower Wheel removal
procedure.
3. Remove one hex fl ange bolt (30, fi g. 1 Briggs or 42, fi g.
1A Honda), from the bottom of the blower housing.
4. The blower housing can now be removed.
5. To remove the blower hub and bushing, remove the 3
capscrews (14, fi g. 1 & 1A).
NOTE:
This hub as well as the bushing each have 6 holes (3
drilled and three tapped).
Reinstall the 3 capscrews back into the 3 tapped holes
in the blower hub. Screw all 3 down until they touch the
bushing. Screw in one at a time in rotation until the ta-
pered bushing releases from the blower hub. If installed,
loosen the set-screw in the bushing fl ange, then slide
both from the shaft.
6. Reverse the above procedure to reinstall the blower
housing, blower hub and bushing.
IMPORTANT
Never change any wiring connections. If
wires are not connected correctly, compo-
nenets could be damaged.
Содержание GT18
Страница 2: ......