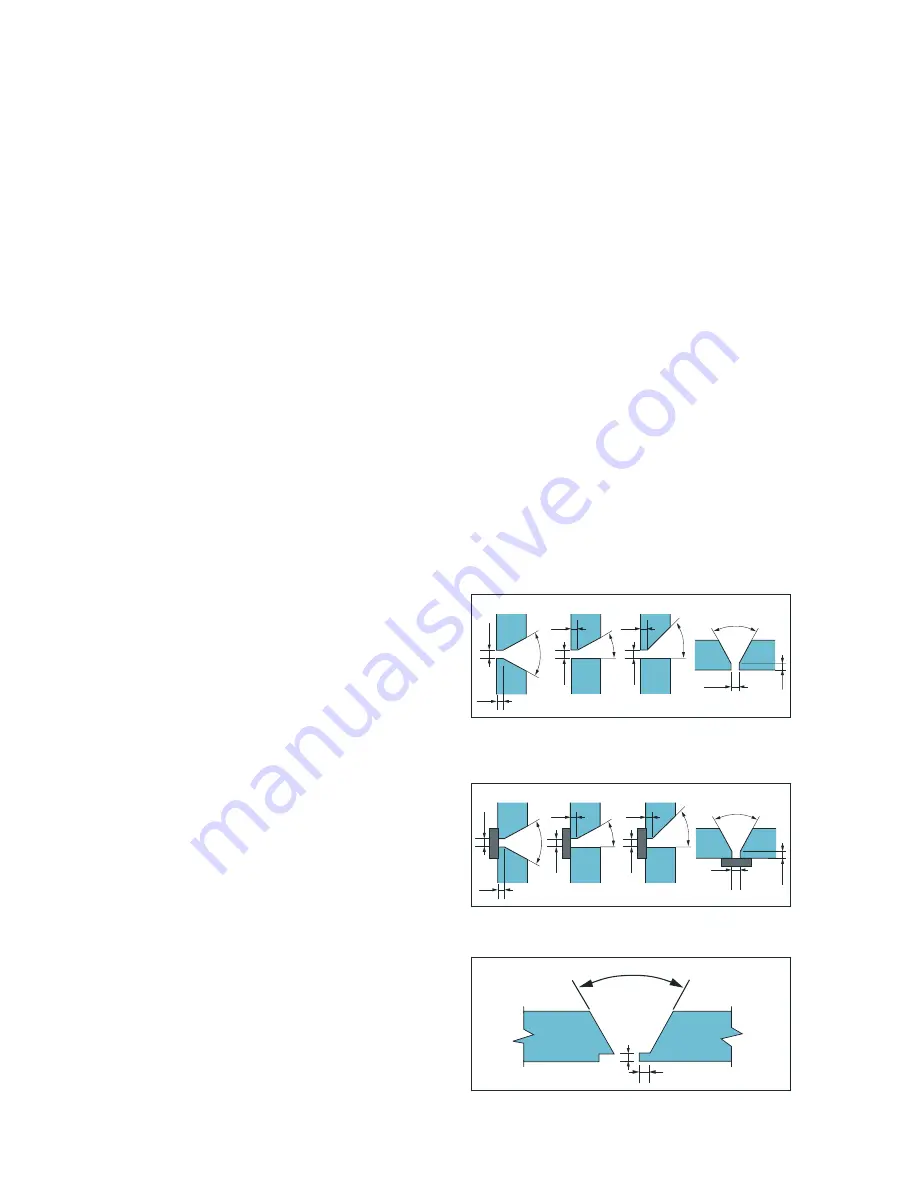
41
sufficiently lit. Anvils should be level and stable so the welder
can carry out his work properly and safely.
For welding in sub-zero conditions, it is important to
provide tolerable working conditions for the welder. When
ambient air is cold, moisture condenses on metal surfaces
which requires preheating them to +50 to +100 °C to
remove the moisture, even though the steel itself requires
no preheating.
Proper earthing is essential in assuring weld quality. The
earth cable must be dimensioned to match the weld cable
and be connected directly to the workpiece. The earthing
point must be metallically clean.
Under humid and wet conditions, the welder must be
properly protected against electrical accidents.
7.5.7 Joint Preparation
Pile pipes are usually delivered from the works with the
ends beveled for welding (30°) and a root face of 1.6 mm
±
0.8 mm. On site, piles are usually cut by a flame cutting or
grinding. It is recommended that the cutting line is marked
all the way around the pile circumference in order that the
cut is made perpendicular to the pile’s centre line. Manual
cutting often leaves a ragged pile end and which is not
sufficiently straight. Such defects must be repaired with
a grinder. The bevels are to be produced by flame cutting
and/or grinding. Flame-cut surfaces must always be
ground to render them clean for welding. For mechanised
welding bevels are to be made by turning.
As pipe piles are welded from the outside, the type of
joint preparation must be such as to enable sufficient
penetration and an even root reinforcement on the inside.
It is particularly important to have a proper air gap to
ensure full penetration.
Recommendations for correct types of joint preparation
are given in Standard EN ISO 9692-1 (Welding and allied
processes. Recommendations for joint preparation. Part
1: Manual metal-arc welding, gas-shielded metal arc
welding, gas welding, TIG welding and beam welding of
steels). Single bevel preparation and single V preparation
are the most common types of joint preparation. Single V
preparation is suitable for welding in all positions. Single
bevel preparation is preferable for welding upright piles.
Single V joint preparation is used to splice full-length piles
delivered from the works. If piles need to be crosscut on
site, the groove may also be prepared as a single bevel
preparation, that is, a square edge against a beveled
edge. Pile ends damaged during transport or installation
must be repaired before splicing. Recommendations for
correct types of joint preparation for welding without
backing are presented in Figure 13.
In splice welding of piles, the use of backing on the inside
of the groove is recommended. A fixed backing should be
of the same steel as the pile sections to be connected.
Ceramic backings can also be used. The backing should
be of sufficient width, usually no less than 50 mm, and at
least 5 mm thick. The backing is to be fitted symmetrically
in relation to the groove and fastened in advance by
intermittent welds (fixed backing) or, for instance, with
adhesive tape (ceramic backing) inside the pile.
When backing is used, the weld reinforcement inside the
pipe is to be ground level with the pipe surface. No air
gap is allowed between the backing and the pipe wall.
Recommended types of joint preparation for welding with
backing are shown in Fig. 14.
The types of joint preparation presented in Figure 13 can
be used for mechanised welding, provided that the root
run is deposited manually. The types of joint preparation
shown in Figure 14 can be used in fully mechanised welding.
There, also the root run is preferably deposited by machine.
A special type of joint preparation has been developed
for that where a machined “tongue” functions as backing
(See Fig. 15). With this type of joint preparation, the welding
parameters should be selected so that the machined
backing (“tongue”) melts, full penetration is achieved, and
lack of fusion and incomplete penetration (“root defects”)
are avoided.
Figure 14. Types of joint preparation for welding with backing.
Figure 15. Joint preparation for fully mechanised welding.
Figure 13. Types of joint preparation for welding without
backing.
°
60
1
1
4-6
0-
2
60
°
0-2
4-
6
60
°
0-2
4-
6
30
°
0-2
4-
6
45
°
0-
2
2-4
60
°
0-2
2-
4
60
°
0-2
2-
4
30
°
0-2
2-
4
45
°